Was ist ein Arbeitsauftrag?
Ein Arbeitsauftrag ist ein autorisiertes Dokument, das für Wartungs-, Reparatur- oder Betriebsaufgaben ausgestellt wird und in dem die Arbeitsdetails, die erforderlichen Ressourcen und die Anweisungen für die Ausführung angegeben sind. Er ist ein wichtiges Instrument, das alles enthält, was für die Durchführung von Instandhaltungsaufgaben erforderlich ist. Er hilft bei der Verwaltung, Zuweisung und Nachverfolgung von Instandhaltungsaktivitäten und stellt sicher, dass diese effizient und im Einklang mit den Betriebszielen durchgeführt werden.
Arbeitsaufträge sind ein grundlegender Bestandteil Ihrer Wartungsarbeiten. Wenn sie gut ausgeführt werden, helfen sie Ihnen und Ihrem Team, die Arbeit zu organisieren und zu erledigen. Ein Arbeitsauftrag kann Informationen enthalten wie:
- Wer den Arbeitsauftrag anfordert
- Wer autorisiert den Arbeitsauftrag?
- Der Ort der Aufgabe
- Was ist die Aufgabe?
- Wer wird die Arbeit ausführen?
- Wann der Arbeitsauftrag erledigt werden muss
- Wie die Aufgabe zu erledigen ist, einschließlich der erforderlichen Teile und anderer Hinweise
Arbeitsaufträge können manuell durch eine von einem Mitarbeiter, einem Kunden oder einem Mieter eingereichte Arbeitsanforderung erstellt werden. Sie können auch automatisch durch eine Software zur Verwaltung von Arbeitsaufträgen oder einen Zeitplan für die vorbeugende Wartung (PM) generiert werden. Arbeitsaufträge können auch über Folgemaßnahmen zu Inspektionen oder Audits generiert werden. Die Verwendung eines CMMS wie eMaint vereinfacht den Arbeitsauftragsprozess.
Welche Arten von Arbeitsaufträgen gibt es?
Es gibt verschiedene Arten von Arbeitsaufträgen, die ein Unternehmen zur Verwaltung seiner Instandhaltung verwenden kann. Die Verwendung der richtigen Art von Arbeitsaufträgen ist entscheidend für die Organisation und Effizienz der Instandhaltung.
Arbeitsaufträge für Inspektionen: Mit Inspektionsaufträgen wird ein Techniker beauftragt, eine bestimmte Anlage zu inspizieren. Wenn während eines Inspektionsauftrags ein Problem festgestellt wird, wird ein neuer Arbeitsauftrag erstellt, um das Problem zu beheben. Was einen Inspektionsauftrag auslöst, hängt von Ihrer Wartungsstrategie ab.
Arbeitsaufträge zur vorbeugenden Wartung: Arbeitsaufträge für die vorbeugende Wartung dienen der Planung von Routinewartungen für Ihre gesamte Ausrüstung. Sie können routinemäßige Reinigung, Schmierung und andere vorbeugende Wartungsaufgaben umfassen, um eine gleichbleibende Leistung der Anlagen zu gewährleisten.
Arbeitsaufträge zur korrektiven Wartung: Arbeitsaufträge zur korrektiven Wartung werden erteilt, um neue Probleme zu beheben, bevor sie ernst werden. Techniker könnten bei Routineinspektionen ein Problem entdecken, oder Ihre AI-Tools könnten einen neuen Fehler in Ihrer Ausrüstung diagnostizieren. Ein Instandsetzungsauftrag kann die Reparatur oder den Austausch von verschlissenen oder beschädigten Teilen an Ihrer Anlage beinhalten.
Notfall-Arbeitsaufträge: Notfall-Arbeitsaufträge werden als Reaktion auf einen unerwarteten Ausfall erstellt. Diese Arbeitsaufträge erfordern eine sofortige Reaktion, um kostspielige Ausfallzeiten zu vermeiden. Bei der Beantwortung von Notfallaufträgen sollten die Techniker aufzeichnen, warum die Anlage ausgefallen ist, was getan wurde, um den normalen Betriebszustand wiederherzustellen, und Empfehlungen geben, wie diese Art von Ausfall vermieden werden kann.
Elektrischer Arbeitsauftrag: Bei elektrischen Arbeitsaufträgen geht es um die Reparatur oder Installation von elektrischen Geräten. Dabei kann es sich um die Installation neuer Leitungen, die Reparatur von Lampen oder die Behebung von Problemen mit der Stromversorgung handeln.
Sonderprojekt-Arbeitsauftrag: Bei Sonderprojekt-Arbeitsaufträgen geht es um neue und verbesserte Ausrüstung. Diese Art von Arbeitsaufträgen ist immer dann erforderlich, wenn eine neue Anlage installiert werden muss. Sie können aus einer Vielzahl von Gründen verwendet werden, z. B. zur Verbesserung der Effizienz des Betriebs oder zum Ersatz veralteter Anlagen.
Wofür wird ein Arbeitsauftrag verwendet?
Arbeitsaufträge dienen der formalen Verfolgung von Wartungs-, Reparatur- und Serviceaufgaben innerhalb einer Organisation. Sie enthalten detaillierte Anweisungen und weisen Ressourcen für Aufgaben zu, indem sie sowohl dokumentieren, was getan werden muss, als auch die dafür erforderlichen Informationen bereitstellen. Arbeitsaufträge tragen dazu bei, dass die Wartung systematisch und effizient durchgeführt wird, wodurch Ausfallzeiten verringert und die Zuverlässigkeit erhöht werden. Sie dienen auch als Nachweis für die durchgeführten Arbeiten und ermöglichen die Einhaltung von Sicherheits- und Regulierungsstandards. Durch die Verwendung von Arbeitsaufträgen können Unternehmen:
- Erklären Sie ein Problem, eine Reparatur oder eine Installation
- Planung der für die Wartung benötigten Ressourcen und Werkzeuge
- Techniker mit detaillierten Anweisungen versorgen
- Dokumentieren Sie den Arbeitsaufwand, die Materialien und die Ressourcen, die für die Ausführung der Arbeiten verwendet wurden.
- Verfolgen Sie alle Wartungsarbeiten, die an den einzelnen Anlagen durchgeführt wurden.
Warum sind Arbeitsaufträge wichtig?
Arbeitsaufträge sind für einen reibungslosen Produktionsbetrieb und die Maximierung der Betriebszeit unerlässlich. Sie ermöglichen eine effektive Planung der Instandhaltung, um die Zuverlässigkeit und Lebensdauer der Anlagen zu erhöhen. Da ein Arbeitsauftrag alle Anweisungen enthält, die für die Durchführung einer Wartungsaufgabe erforderlich sind, ist er im Grunde das Rückgrat eines jeden guten Wartungsplans.
Der Name des Spiels mit Arbeitsaufträgen ist Effizienz. Traditionell geht es darum, den Wartungsprozess zu rationalisieren und zu organisieren. Der Einsatz einer CMMS-Software für die Verwaltung von Arbeitsaufträgen hebt diese Effizienzgewinne auf die nächste Stufe. Wartungsteams können genaue Aufzeichnungen über ihre Anlagen führen, Arbeits- und Bestandskosten verfolgen, Trends bei Geräteausfällen verfolgen und Kosten schätzen. Letztlich können sie ihre Anlagen proaktiv verwalten, indem sie Einblicke in alle Anlagen erhalten.
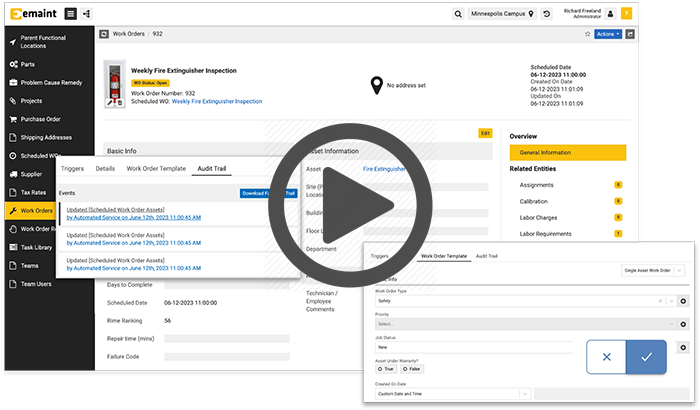
Arbeitsauftrag-Prozess: Etappen eines Arbeitsauftrags
Der Prozess der Erstellung und Genehmigung eines Arbeitsauftrags besteht aus sechs Schritten:
1. Identifizieren Sie die Aufgabe
Der Arbeitsauftragsprozess beginnt, wenn es eine Aufgabe gibt, die erledigt werden muss. Dies wird oft durch unvorhergesehene Probleme wie eine neue Serviceanfrage oder einen Notfall ausgelöst. Er kann aber auch durch vordefinierte Aktivitäten wie vorbeugende Wartungsaufgaben oder Routineinspektionen ausgelöst werden. Der Prozess ist viel einfacher, wenn die Wartung geplant ist und die Ressourcen im Voraus zugewiesen werden können.
2. Erstellen Sie einen neuen Arbeitsauftrag
Sobald die Aufgabe identifiziert ist, wird eine Wartungsanforderung an das Wartungsteam übermittelt. Wenn z. B. eine Maschine unerwartet ausfällt, wird eine Arbeitsanforderung zur Reparatur eingereicht. Wenn eine Wartungsaufgabe geplant ist, kann ein CMMS wie eMaint automatisch eine Arbeitsanforderung zum entsprechenden Zeitpunkt ausgeben.
3. Setzen Sie Prioritäten bei der Arbeit
Wenn Anfragen eingereicht werden, ist es Sache des Wartungsteams, die Dringlichkeit und Durchführbarkeit der Anfrage zu bestimmen. Einige Anfragen sind zeitkritischer als andere, je nachdem, wie sie sich auf den Betrieb auswirken. Wird die Arbeitsanforderung genehmigt, werden das richtige Personal und die richtigen Teile bestimmt, und die Anforderung wird in einen Arbeitsauftrag umgewandelt.
4. Einen Arbeitsauftrag erstellen
Sobald die Arbeitsanforderung genehmigt und nach Prioritäten geordnet wurde, wird offiziell ein Arbeitsauftrag erstellt. Er sollte alle Informationen enthalten, die für die Erledigung der Aufgabe erforderlich sind, und die Ressourcen sollten bereits zugewiesen und bereit sein.
5. Fertigstellung und Dokumentation der Arbeiten
Der Arbeitsauftrag wird dann einem Techniker zur Ausführung zugewiesen. Dieser führt die Aufgabe aus und dokumentiert sie in den Aufzeichnungen der Anlage.
6. Analysieren Sie die Ergebnisse
Bleiben Sie nicht dabei stehen. Die Wartung mag abgeschlossen sein, aber es gibt immer Raum für Verbesserungen. Ihre Auftragshistorie bietet wertvolle Einblicke in Ihre Ausrüstung und Ihre bestehenden Prozesse, um kontinuierliche Verbesserungen vorzunehmen. Stellen Sie sicher, dass Sie messen und bei Bedarf anpassen.
Welche Informationen in einem Arbeitsauftrag enthalten sein müssen
Nachdem wir nun die einzelnen Schritte des Arbeitsauftragsprozesses besprochen haben, ist es wichtig, genau zu wissen, was in einem Arbeitsauftrag selbst enthalten sein sollte. Im Allgemeinen sollte eine Arbeitsauftragsbeschreibung Folgendes enthalten:
- Wer autorisiert den Arbeitsauftrag?
- Wer wird die Arbeit ausführen?
- Was ist die Aufgabe?
- Wann der Arbeitsauftrag erledigt werden muss
- Wo der Arbeitsauftrag ausgeführt werden muss
- Wie die Aufgabe zu erledigen ist, einschließlich der erforderlichen Teile und anderer Hinweise
Das Verfassen des eigentlichen Arbeitsauftrags ist nicht so entmutigend, wie es vielleicht scheint. Es geht lediglich darum, die erforderliche Wartung oder Aufgabe genau zu beschreiben. Beginnen Sie damit, den Anforderer zu identifizieren und seine Kontaktinformationen anzugeben. Beschreiben Sie das Problem oder die Aufgabe klar und deutlich, einschließlich relevanter Details wie den Standort und die betroffene Ausrüstung. Geben Sie die Prioritätsstufe an, um den Wartungsteams zu helfen, ihre Arbeit zu priorisieren. Fügen Sie alle notwendigen Anhänge wie Fotos oder Diagramme bei, die zusätzlichen Kontext liefern können. Weisen Sie Ressourcen wie Personal und Material zu, die für die Durchführung der Aufgabe benötigt werden. Geben Sie schließlich ein Zieldatum für die Fertigstellung an, um die Erwartungen festzulegen und die Arbeitsbelastung zu steuern. Durch die Verwendung eines strukturierten Formats wie diesem wird sichergestellt, dass alle wichtigen Informationen erfasst werden, was eine effiziente und effektive Ausführung erleichtert.
Bewährte Praktiken für die Verwaltung von Arbeitsaufträgen
Eine effiziente Verwaltung von Arbeitsaufträgen umfasst mehrere bewährte Verfahren.
- Stellen Sie sicher, dass Arbeitsaufträge detailliert und vollständig sind: Ein Arbeitsauftrag sollte alle für die Ausführung der Aufgabe erforderlichen Informationen enthalten. Jede fehlende Information führt zu einer Verlangsamung der Instandhaltung. Verwenden Sie ein zentrales System, wie z. B. ein CMMS, um Arbeitsaufträge zu verfolgen und zu verwalten, um Transparenz und Zugänglichkeit zu gewährleisten.
- Standardisieren Sie Ihren Prozess: Vereinfachen Sie den Arbeitsauftragsprozess, indem Sie ihn jedes Mal gleich gestalten. Erstellen Sie eine Arbeitsauftragsvorlage und stellen Sie sicher, dass jeder weiß, wie man sie korrekt ausfüllt. Führen Sie Richtlinien für die Einreichung von Arbeitsaufträgen ein und vermeiden Sie Unstimmigkeiten bei Ihren Wartungsarbeiten.
- Definieren Sie Rollen und Zuständigkeiten klar und deutlich: Eine klare Rollenverteilung in Ihrem Arbeitsauftragsprozess kann zu einer effizienteren und präziseren Aufgabenausführung beitragen. Indem Sie klären, wer befugt ist, Arbeitsaufträge zu erstellen, zuzuweisen, zu priorisieren, abzuschließen und zu überprüfen, vermeiden Sie Doppelarbeit und nicht autorisierte Arbeiten. Fördern Sie eine klare Kommunikation zwischen Instandhaltungsteams und Anforderern, um Fragen oder Änderungen umgehend zu klären.
- Legen Sie Ihre Wartungsziele und KPIs fest: Klare Ziele und Leistungskennzahlen bieten einen Rahmen für die Bewertung Ihrer Arbeitsaufträge. Sie helfen dabei, die Instandhaltungsstrategie Ihres Unternehmens zu definieren und Ihr Team auf Kurs zu halten.
- Automatisieren Sie Ihre Arbeitsaufträge: Nutzen Sie ein CMMS zur Automatisierung von Arbeitsaufträgen auf der Grundlage von Ausfällen, zeit-, ereignis-, nutzungs- und zustandsabhängigen Auslösern. eMaint ermöglicht beispielsweise die automatische Planung von Arbeitsaufträgen auf der Grundlage von Zustandsdaten der Ausrüstung, sodass Sie Probleme frühzeitig beheben können, bevor sie zu einem Ausfall führen.
- Analysieren und verbessern Sie Ihren Arbeitsauftragsprozess laufend: Denken Sie daran, dass eine effektive Verwaltung von Arbeitsaufträgen keine einmalige Aufgabe ist. Es ist ein kontinuierlicher Prozess der Verfeinerung und Anpassung. Analysieren Sie Ihren Prozess ständig, um sicherzustellen, dass sich Ihr Team an die bewährten Verfahren hält. Dies wiederum wird die Produktivität und die Wartungsergebnisse verbessern.
Beispiel eines Arbeitsauftrags
Ein effektiver Arbeitsauftrag sollte klar, spezifisch und detailliert sein. Er muss außerdem präzise formuliert sein, um Verwechslungen zu vermeiden, und einen eindeutigen Dokumentationspfad für die Wartungshistorie der Anlage bieten.
Ein Beispiel für einen Arbeitsauftrag könnte ein Dokument sein, das zur Reparatur einer defekten HLK-Anlage in einem Bürogebäude ausgestellt wird. Darin würden die Art des Problems, der Standort, der beauftragte Techniker, die erforderlichen Werkzeuge, die geschätzte Fertigstellungszeit und alle Sicherheitsvorkehrungen angegeben.
Wenn ein Arbeitsauftrag erstellt wird, sollte er das vorliegende Problem beschreiben und die folgenden Fragen beantworten:
- Welche Anlage muss repariert werden? Wo befindet sich das Objekt?
- Welche Teile müssen ggf. ersetzt werden?
- Welche Werkzeuge muss das Wartungsteam mitbringen?
- Wie viele Arbeitnehmer werden für diese Tätigkeit benötigt? Welche Fähigkeiten müssen sie haben? Werden Sie externe Arbeitskräfte hinzuziehen müssen?
- Wie sieht der Zeitplan für die Durchführung dieser Aufgabe aus? Handelt es sich um ein präventives Wartungsprojekt, das zu einem festen Termin durchgeführt werden muss? Handelt es sich um eine dringende Reparatur an einer wichtigen Anlage, die sofort erledigt werden muss?
- Welche Kosten sind mit dieser Arbeit verbunden?
- Wer hat die Arbeit in Auftrag gegeben? Wer hat die Arbeit genehmigt?
Der Unterschied zwischen einem Arbeitsauftrag und einer Arbeitsanforderung
Es gibt einen feinen, aber wichtigen Unterschied zwischen Arbeitsaufträgen und Arbeitsanfragen. Eine Arbeitsanforderung, auch bekannt als Serviceanforderung, bezieht sich in der Regel auf eine Situation, in der ein Nicht-Instandhaltungsmitarbeiter oder ein Kunde einen Antrag auf Instandhaltung gestellt hat. Ein Arbeitsauftrag bezieht sich auf eine Instandhaltungsmaßnahme, für deren Durchführung das Instandhaltungsteam eine Genehmigung erhalten hat.
Arbeitsanforderungen haben eine andere Funktion, aber sie sehen auch ein wenig anders aus. Eine Arbeitsanforderung beschreibt kurz das Problem, um den Beginn eines Wartungsablaufs zu markieren. Sie wird in der Regel nach der Art der Branche, des Unternehmens oder der Priorität der Aufgabe klassifiziert, z. B. als Notfallanforderung, wenn ein Chemieunfall entdeckt wird.
In der Zwischenzeit wird ein Arbeitsauftrag erst nach Genehmigung eines Antrags erteilt, wobei das vorhandene Budget, die Kritikalität und das Alter der Anlage berücksichtigt werden. Erst nachdem ein Arbeitsauftrag erstellt wurde, kann die Arbeit beginnen.
Was ist der Unterschied zwischen einem Arbeitsauftrag und einer Bestellung oder Rechnung?
Ein Arbeitsauftrag, eine Bestellung und eine Rechnung dienen sehr unterschiedlichen Zwecken in einem Unternehmen. Ein Arbeitsauftrag dient der Instandhaltung und beschreibt die auszuführenden Aufgaben. Im Gegensatz dazu ist eine Bestellung ein Dokument, das an Lieferanten geschickt wird, um Waren oder Dienstleistungen zu beschaffen, und in dem die Artikel, Mengen und vereinbarten Preise angegeben sind. Eine Rechnung ist eine Rechnung, die von einem Lieferanten ausgestellt wird, um die Zahlung für gelieferte Waren oder Dienstleistungen zu verlangen. Ein Arbeitsauftrag initiiert Instandhaltungsmaßnahmen, eine Bestellung initiiert Einkaufsaktivitäten, und eine Rechnung erleichtert finanzielle Transaktionen und die Zahlungsabwicklung.
Was ist der Unterschied zwischen Arbeits- und Wartungsaufträgen?
Wir haben uns zwar hauptsächlich auf Arbeitsaufträge bezogen, die sich auf Instandhaltungsarbeiten beziehen, aber sie sind vielseitiger als das. Ein Arbeitsauftrag kann sich auf verschiedene betriebliche Aufgaben beziehen, z. B. Wartung, Bau oder IT-Dienstleistungen. Ein Wartungsauftrag bezieht sich ausdrücklich auf Arbeitsaufträge, die für die Instandhaltung, Reparatur oder Inspektion von Geräten und Anlagen erstellt werden. Alle Wartungsaufträge sind Arbeitsaufträge, aber nicht alle Arbeitsaufträge sind Wartungsaufträge.
Digitalisieren von Arbeitsaufträgen zur Verbesserung der Effizienz
Manuell erstellte Arbeitsaufträge sind seit langem Teil der Welt der Instandhaltung. Obwohl papierbasierte Arbeitsaufträge in mancher Hinsicht einfacher sein können, sind sie in großem Umfang nicht gut geeignet. Arbeitsaufträge in Papierform können zu Verzögerungen bei der Kommunikation, zu zusätzlichen Kosten für die Dateneingabe und zu Kopfschmerzen bei der sicheren Aufbewahrung der Aufträge führen. Vor allem aber sind sie einfach nur langsam. In der heutigen schnelllebigen Welt der Instandhaltung sind papierbasierte Arbeitsaufträge ineffizient - ganz zu schweigen von ihrer Umweltfreundlichkeit.
Computergestützte Instandhaltungsmanagementsysteme helfen Unternehmen, die Leistungsfähigkeit cloudbasierter Online-Arbeitsauftragssoftware zu nutzen und wiederholte Telefonanrufe, Haftnotizen und fehlenden Papierkram zu vermeiden. Die Zentralisierung und Rationalisierung des Arbeitsauftragsprozesses verbessert die Übersichtlichkeit und sorgt für eine pünktliche Erledigung der Arbeit.

Apps für Arbeitsaufträge
Eine Arbeitsauftrags-Software-App, auch bekannt als mobiles CMMS, ist die Smartphone- oder Tablet-Version einer Arbeitsauftrags-Software. Arbeitsauftrags-Software-Apps ermöglichen es Technikern, Daten von mobilen Geräten aus einzugeben, während sie Arbeitsaufträge erledigen. Für die Planung und Terminierung von vorbeugenden Wartungsaufgaben können Techniker ihre Geräte verwenden, um laufende Arbeitsaufträge sowie Anlagen, die noch gewartet werden müssen, zu verfolgen. Mit der App haben sie Informationen über die historische Leistung und Inspektionsaufzeichnungen direkt zur Hand, was die Wartung vor Ort einfacher denn je macht.
Die Vorteile der Software für digitale Arbeitsaufträge
Eine Software für digitale Arbeitsaufträge, wie z. B. ein CMMS, bietet große Vorteile, damit Ihre Wartungsarbeiten reibungslos ablaufen können.
Verbesserte Effizienz: Indem manuelle und oft papierlastige Prozesse durch automatisierte digitale Workflows ersetzt werden, können Wartungsteams Aufgaben wie das Erstellen, Zuweisen und Verfolgen von Arbeitsaufträgen rationalisieren und beschleunigen. Darüber hinaus ermöglichen Statusaktualisierungen in Echtzeit den Teams eine schnelle Reaktion auf veränderte Umstände. Diese verbesserte Geschwindigkeit und Flexibilität spart wertvolle Zeit und Ressourcen und kann dazu beitragen, unerwartete Ausfallzeiten zu reduzieren.
Weniger Fehler: Digitale Systeme für Arbeitsaufträge tragen auch dazu bei, die mit der manuellen Dateneingabe verbundenen Fehler zu reduzieren. Genaue Daten sind sowohl für eine fundierte Entscheidungsfindung als auch für die Einhaltung von Vorschriften entscheidend. Durch die Zentralisierung aller Informationen in einer einzigen, leicht zugänglichen Plattform gewährleistet CMMS-Software konsistente und zuverlässige Daten.
Bessere Kommunikation: Digitale Software für Arbeitsaufträge erleichtert die Kommunikation zwischen den Teammitgliedern. Da alle Daten zentral gespeichert und in Echtzeit verfügbar sind, haben die Teams sofortigen Zugriff auf alle Informationen, die sie für ihre Arbeit benötigen. Dies fördert die Transparenz und die Zusammenarbeit, ermöglicht eine schnellere Problemlösung und verhindert mögliche Engpässe.
Wie man ein CMMS für die Verwaltung von Arbeitsaufträgen einsetzt
Arbeitsaufträge sind das Herzstück eines Wartungsprogramms. Die Tools in einem CMMS helfen Unternehmen, über Arbeit, Projekte und Ressourcen auf dem Laufenden zu bleiben. Ein CMMS kann Unternehmen dabei helfen, ihren Arbeitsrückstand zu kontrollieren, die Produktivität zu steigern und die Einhaltung von Vorschriften zu verwalten. Es ist der Schlüssel zu einer effektiven Verwaltung von Arbeitsaufträgen.
Was ist Work Order Management?
Die Verwaltung von Arbeitsaufträgen bezieht sich auf den Prozess der Priorisierung, Fertigstellung und rechtzeitigen Dokumentation von Wartungsaufträgen. Auch wenn dies einfach klingt, ist der Prozess zeitaufwändig und fehleranfällig, wenn er von Hand durchgeführt wird. Auf Papier ausgefüllte und in Schränken abgelegte Arbeitsaufträge können leicht verlegt werden, und manuelle Kalkulationstabellen lassen sich nur langsam mit neuen Informationen aktualisieren. Der Einsatz einer robusten Software für die Verwaltung von Arbeitsaufträgen hingegen beschleunigt und rationalisiert diesen Prozess und gewährleistet gleichzeitig eine genaue, aktuelle Dokumentation. Wenn dieser Ansatz effektiv umgesetzt wird, kann er in einer Anlage erschwinglich und skalierbar sein und ermöglicht es den Wartungsteams, ungeplante Ausfallzeiten von Anlagen zu reduzieren und Geld zu sparen.
Lebenszyklus eines Arbeitsauftrags: Prozess der Arbeitsauftragsverwaltung
Der Prozess der Arbeitsauftragsverwaltung beginnt in der Regel damit, dass ein Wartungsmanager eine Arbeitsanforderung annimmt und sie in einen robusten Arbeitsauftrag umwandelt. Das ist aber nur der Anfang, denn der gesamte Prozess lässt sich durch einen Lebenszyklus von sechs Schritten zusammenfassen.
- Identifizierung von Aufgaben: Ermitteln, was zur Lösung eines Problems getan werden muss.
- Arbeitsauftrag erstellen: Füllen Sie ein Arbeitsauftragsformular aus, um Wartungsarbeiten zu genehmigen.
- Genehmigung des Arbeitsauftrags:Das Wartungsmanagement entscheidet, ob ein legitimer Bedarf besteht. Wenn dies der Fall ist und die Aufgabe in einem angemessenen Zeitraum erledigt werden kann, wird ein offizieller Arbeitsauftrag erteilt.
- Zuweisung von Prioritäten: Arbeitsaufträge werden unter Berücksichtigung der Dringlichkeit, des vorhandenen Rückstands und der Verfügbarkeit des Teams bewertet.
- Verteilung und Ausführung: Genehmigte und nach Prioritäten geordnete Arbeitsaufträge werden ausgedruckt und an die Techniker zur Durchführung der erforderlichen Tätigkeit weitergegeben.
- Dokumentation der Ergebnisse: Die Arbeiter dokumentieren die Vorgänge genau und rechtzeitig. Der Arbeitsauftrag kann geschlossen werden, wenn alle Leistungen erbracht wurden und die Arbeit abgeschlossen ist.
Was sind die verschiedenen Ansätze für die Verwaltung von Arbeitsaufträgen?
Es gibt zwei Hauptansätze für die Verwaltung von Arbeitsaufträgen: manuell und automatisiert. Bei einem manuellen Ansatz werden Stift und Papier, Tabellenkalkulationen, Whiteboards oder eine Kombination aus allen drei Methoden verwendet. Bei einem automatisierten Ansatz wird eine Software für die Verwaltung von Arbeitsaufträgen eingesetzt, um die Erstellung von Arbeitsaufträgen und die Dokumentationsabläufe zu automatisieren.
Manuelle Arbeitsauftragsmethoden waren früher alles, was den Wartungsteams zur Verfügung stand. Für kleinere Unternehmen, die ein geringes Auftragsvolumen bewältigen, können sie durchaus noch effektiv sein. Ein CMMS ist jedoch ein weitaus zuverlässigeres System, das die Priorisierung von Arbeitsaufträgen erleichtert, ohne dass man sich durch einen Berg von Papierkram wühlen muss. Es kann Arbeitsaufträge automatisch an verfügbare Techniker verteilen und Wartungsaufzeichnungen sofort mit Echtzeitinformationen aktualisieren.
Verwaltung von Arbeitsauftragsanfragen
Nicht alle Arbeiten lassen sich im Voraus planen. Es muss ein Anforderungssystem geben, wenn Korrekturarbeiten erforderlich sind oder Kundenwünsche auftauchen. Instandhaltungsleiter sollten die Arbeitsabläufe für die Einreichung, Genehmigung, Ablehnung und Erledigung von Anfragen an die spezifischen Bedürfnisse ihres Unternehmens anpassen. Die frühzeitige Festlegung eines Workflow-Prozesses gewährleistet:
- Standardarbeitsanweisungen (SOPs) werden von allen Anwendern befolgt
- Die Arbeit durchläuft einen Genehmigungsprozess
- Zuständigkeitsbereiche und Erwartungen sind für die Nutzer klar
- Regelmäßige Prozessaudits werden durchgeführt
- Es werden gültige Daten in ein CMMS eingegeben
- Effizienter Kommunikationsfluss zwischen allen Beteiligten
Mit eMaint können Unternehmen aus drei Optionen für die Einreichung von Arbeitsaufträgen wählen:
- Arbeitsanforderer erhalten ein eMaint-Benutzer-Login, mit dem sie Anfragen einreichen und den Verlauf und Status dieser Anfragen einsehen können.
- Arbeitsanforderer senden eine E-Mail an eine bestimmte E-Mail-Adresse, die in eine eMaint-Arbeitsanforderung umgewandelt wird.
- Die Antragsteller übermitteln ihre Anträge an eMaint über ein individuelles Webformular, das in die Website oder das Intranet eines Unternehmens eingebettet ist.
Tools für Arbeitsanfragen wie diese reduzieren Kommunikationsfehler. Unternehmen können Antragstellern automatische E-Mail-Benachrichtigungen senden, wenn ein Arbeitsauftrag genehmigt oder abgelehnt wird, gefolgt von einer automatischen E-Mail-Benachrichtigung mit einer Zufriedenheitsumfrage, sobald die Arbeit abgeschlossen ist.
Mit modernen mobilen CMMS-Lösungen können Anforderer jederzeit und überall mit ihrem Mobilgerät einen Arbeitsauftrag erteilen. Die Antragsteller können ihren Anträgen Bilder beifügen, einschließlich der zu reparierenden Geräte.
Was ist eine Software für Arbeitsaufträge?
Die Software für Arbeitsaufträge macht es Unternehmen leicht, die termingerechte Fertigstellung von Arbeiten zu erhöhen, die Effizienz der Arbeitsabläufe zu verbessern, die Fälligkeitstermine von Projekten im Auge zu behalten und vieles mehr.
- Zuweisung von Arbeitsaufträgen - Mit Hilfe von Funktionen wie den Wartungsplanungswerkzeugen von eMaint können Wartungsplaner und Disponenten Arbeitsaufträge direkt an Mitarbeiter, Auftragnehmer oder Lieferanten für bestimmte Tage, Zeiten und Orte zuweisen. Zugewiesene und nicht zugewiesene Arbeitsaufträge können auch auf einer Kalenderanzeige angezeigt werden, und die Arbeit kann bei Bedarf leicht neu zugewiesen werden.
- Terminplanungskalender - Zeigen Sie einen Kalender nach Tag, Woche oder Monat mit allen Arbeitsressourcen und offenen Arbeitsaufträgen an. Sie können auch Kalenderansichten anpassen und die Arbeit nach Mitarbeitern, Arbeitsauftragstyp und mehr filtern. Unternehmen können auch die Funktion PM-Projektion nutzen, um anstehende Arbeiten zu planen und sicherzustellen, dass die richtigen Teile, Arbeitskräfte und Werkzeuge verfügbar sind.
- Berichte und Dashboards - Nutzen Sie Berichte und Dashboards, um auf dem Laufenden zu bleiben. Kategorisieren Sie Arbeitsaufträge nach Typ, Techniker, Abteilung oder jedem anderen benutzerdefinierten Feld.
- Mobile Instandhaltung - Mit mobilen CMMS-Wartungsdiensten wie MX Mobile von eMaint können Unternehmen in Echtzeit auf Daten zugreifen und Funktionen in ihren Einrichtungen und unterwegs ausführen, wie z. B. das Einreichen und Genehmigen von Arbeitsanforderungen, das Unterzeichnen und Abschließen von Arbeitsaufträgen und vieles mehr.
- Nachverfolgung von Projekten - Große Überholungs- und Renovierungsprojekte können Kopfzerbrechen bereiten, aber der Verwaltungsprozess muss es nicht. Mit den Projektmanagement-Tools von eMaint können Unternehmen auf einfache Weise Projekte erstellen und Arbeitsaufträge vom Projektbeginn bis zum Abschluss zuweisen und verfolgen. Anlagen, Bestände und Maßnahmen, die sich auf betriebliche Ziele auswirken, können über eine einzige Plattform abgewickelt werden. Mit Gantt-Diagrammen erhalten die Benutzer ein klares visuelles Verständnis der Fertigstellungsraten von Arbeitsaufträgen im Vergleich zum Enddatum eines Projekts.
Häufig gestellte Fragen zum Arbeitsauftrag
Was bedeutet "Arbeitsauftrag"?
Ein Arbeitsauftrag ist, einfach ausgedrückt, ein Auftrag für Wartungsarbeiten. Ein Arbeitsauftrag ist ein Dokument oder eine digitale Aufgabe, in der Wartungsarbeiten, Teile und Prozesse für Anlagen detailliert beschrieben werden. Arbeitsaufträge sind der Schlüssel zur Organisation einer Instandhaltungsstrategie.
Was ist ein Instandhaltungsarbeitsauftrag?
Ein Instandhaltungsauftrag ist eine formale Richtlinie, die bestimmte Instandhaltungsaufgaben an Geräten oder Anlagen genehmigt. Er enthält eine detaillierte Auftragsbeschreibung, die erforderlichen Ressourcen und Ausführungsschritte und bietet einen strukturierten Ansatz für Instandhaltungsteams. Er ist wichtig für die Verfolgung, Planung und Gewährleistung der Verantwortlichkeit von Instandhaltungsmaßnahmen.
Was ist der Unterschied zwischen einer Arbeitsanfrage und einem Arbeitsauftrag?
Eine Arbeitsanfrage ist eine informelle Mitteilung über ein Problem oder eine erforderliche Aufgabe, die in der Regel von Mitarbeitern oder Kunden eingereicht wird. Im Gegensatz dazu ist ein Arbeitsauftrag ein formelles Dokument, das als Antwort auf eine Arbeitsanfrage ausgestellt wird und die erforderlichen spezifischen Aufgaben autorisiert und detailliert beschreibt. Er enthält zugewiesene Ressourcen, Zeitvorgaben und Anweisungen und liefert umsetzbare Schritte zur Erledigung der erforderlichen Arbeiten.
Was ist der Zweck eines Arbeitsauftragssystems?
Der Zweck eines Arbeitsauftragssystems besteht darin, den Prozess der Abwicklung von Wartungsaufgaben von der Einleitung bis zum Abschluss zu rationalisieren und zu verwalten. Es hilft bei der Verfolgung des Fortschritts, der Planung von Ressourcen und der Pflege historischer Aufzeichnungen über die geleistete Arbeit. Der Einsatz eines Systems zur Verwaltung von Arbeitsaufträgen trägt zur Verbesserung der betrieblichen Effizienz und der Anlagenverwaltung bei.
Wie füllt man einen Auftrag für Wartungsarbeiten aus?
Um einen Instandhaltungsauftrag effektiv auszufüllen, stellen Sie sicher, dass er alle folgenden Informationen enthält:
- Beschreibung des Problems: Beschreiben Sie klar und deutlich das Problem oder die Wartungsaufgabe.
- Ort: Geben Sie an, wo die Arbeiten ausgeführt werden sollen.
- Priorität: Weisen Sie eine Prioritätsstufe zu, um rechtzeitiges Handeln zu ermöglichen.
- Zugewiesen an: Geben Sie an, wer für die Erledigung der Aufgabe verantwortlich ist.
- Geschätzte Zeit: Geben Sie an, wie lange die Aufgabe voraussichtlich dauern wird.
- Erforderliche Werkzeuge und Materialien: Führen Sie alle erforderlichen Werkzeuge und Materialien auf.
- Sicherheitshinweise: Geben Sie alle Sicherheitsvorkehrungen oder relevanten Vorschriften an.
Was sind die Funktionen eines Arbeitsauftrags?
Zu den Funktionen eines Arbeitsauftrags gehören:
- Autorisierung: Legitimierung des Beginns einer Aufgabe.
- Dokumentation: Aufzeichnung von Aufgaben, Ressourcen und Zeit.
- Koordinierung: Sicherstellen, dass Ressourcen geplant und verfügbar sind.
- Verfolgung: Überwachung der Fortschritte und Statusaktualisierungen.
- Analyse: Bereitstellung von Daten für betriebliche Erkenntnisse und Zukunftsplanung.
Was sollte in einem Arbeitsauftrag stehen?
Ein Arbeitsauftrag sollte Folgendes enthalten:
- Beschreibung der Arbeit: Detaillierte Erläuterung der Aufgabe.
- Informationen zum Antragsteller: Wer die Arbeit angefordert hat, und seine Kontaktinformationen.
- Beauftragtes Personal: Namen und Funktionen der für die Durchführung verantwortlichen Personen.
- Zeitplan: Anfangs- und Enddatum, einschließlich etwaiger Meilensteine.
- Ressourcen: Liste der benötigten Materialien und Geräte.
- Anweisungen und Normen: Spezifische Verfahren oder Standards, die zu befolgen sind.
- Genehmigungsunterschriften: Für den Beginn und den Abschluss der Arbeiten sind Genehmigungen erforderlich.