Maintenance software, evolved.
Maximize uptime and unlock the power of connected reliability.
Meet eMaint, the revolutionary CMMS, EAM, and IIoT software from Fluke Reliability that connects hardware and software in a cloud-based ecosystem — empowering you to boost uptime, strengthen reliability, and drive production.

Based on 268+ reviews



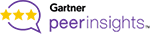
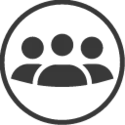
150,000+
USERS
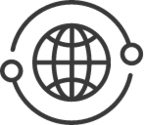
116
COUNTRIES
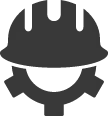
7,400+
MAINTENANCE TEAMS HELPED
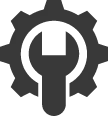
3.4 Million
MACHINES FIXED
Maintenance teams like yours have used eMaint to:
Explore eMaint CMMS
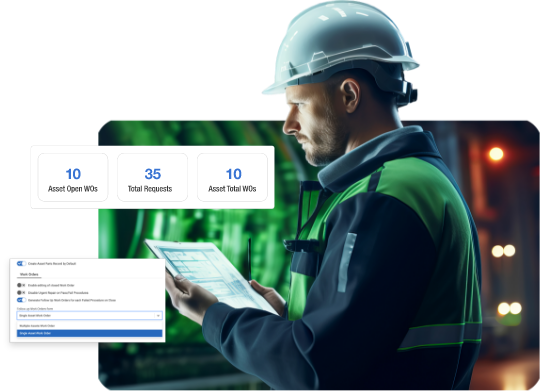
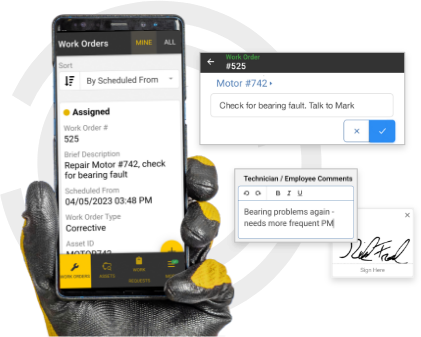
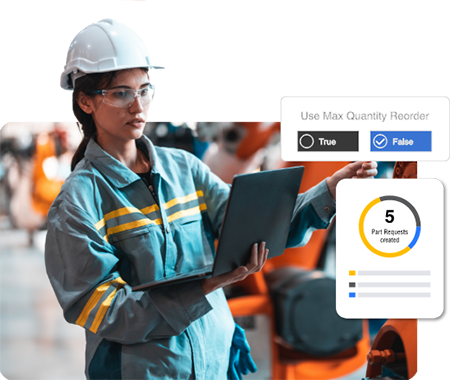
“Now we’re not only getting our preventive maintenance where it needs to be, we’ve also moved into the predictive maintenance side… I like the way that it does the reporting and auto-generates the work orders when it’s out of its threshold — over the temperature or vibration.”
Enterprise Asset Management
eMaint is the leading EAM software when it comes to customer care, time-to-value, and ROI.
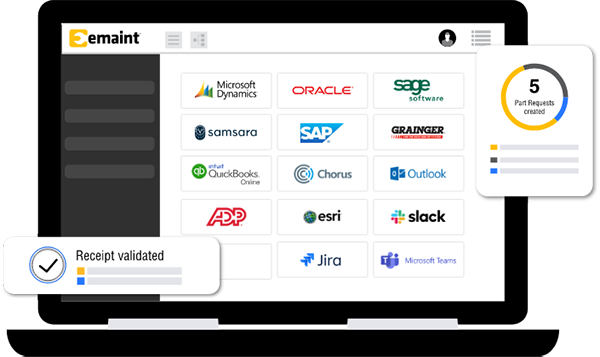
Detailed asset info, status, and maintenance hsitory is a few clicks away. Manage the lifecycle of your assets, from purchase to EOL.
Manage maintenance and standardize your strategy across work sites, languages, and currencies. Simplify enterprise-level reporting and streamline audit compliance.
Software & hardware integrations
Simplified workflows and seamless data sharing with 1000+ apps. Connect to Fluke sensors, tap into siloed SCADA & PLC system data, and integrate with ERP and BI platforms.