
Based on 268+ reviews



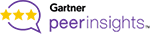
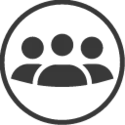
150,000+
USERS
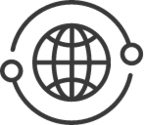
116
COUNTRIES
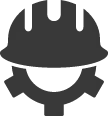
7,400+
MAINTENANCE TEAMS HELPED
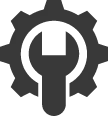
3.4 Million
MACHINES FIXED
eMaint CMMS simplifies work order management.
Your day shouldn’t be spent searching through stickie notes or firefighting maintenance emergencies—you should be free to focus on the bigger picture, charting a course to increased uptime and strengthened reliability. That’s where eMaint comes in.
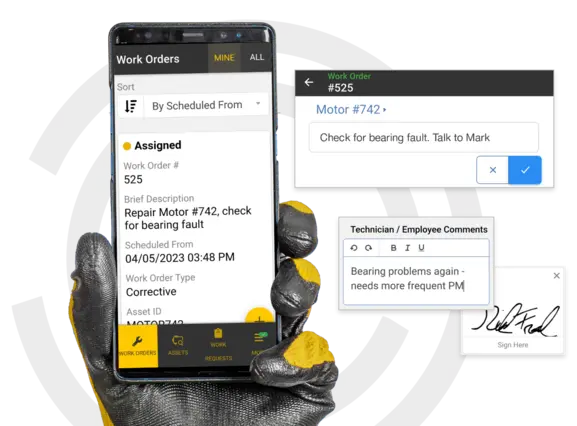
Work Order Software, Your Way
Manage work orders and work requests. Customize to your heart’s delight. Automate processes to save time.
Say goodbye to pen & paper chaos and firefighting unplanned downtime.

Simple, configurable, flexible interface
Organize, create, assign, and track work orders and work requests. Get in and get out with eMaint search functionality. Make your workspace your own—rename labels, drag and drop columns, and prioritize work orders as you see fit.

A work order for everything
Create multi-asset work orders configured to each job. Quickly fire off route-based inspection work orders. Design work order templates with built-in procedures to standardize your maintenance strategy across the enterprise.

Automate work, maximize uptime
Automatically move work orders through approval levels with intuitive workflows. Get safety, quality, sanitation, and purchasing involved. Automate work orders to trigger when asset condition data indicates a failure is coming—preventing downtime disaster.

Easy Drag & Drop Work Order Management Scheduling
Finish your maintenance planning in a few clicks. Get a bird’s eye view of team schedules and quickly resolve conflicts.
You’re busy. Let eMaint take care of the maintenance scheduling madness.

Seamless PM planning: save time, reduce costs
Establish routine preventive maintenance and recurring work orders, Schedule PMs to trigger based on equipment usage. Automate work orders to trigger based on asset condition data like vibration or temperature.

Simple drag & drop work order scheduler
Envision and plan out your work orders and PMs with the intuitive eMaint Scheduler, an interactive, drag & drop calendar. Assign work quickly. Customize and filter your view to see only the work that matters to you.

Automatic notices solve scheduling conflicts
Get automatic notifications of work schedule conflicts as you go and resolve them quickly. Receive overscheduling alerts related to workers’ overall weekly assignments and level-load work distribution.
Mobile Work Orders: Work in the Field & Offline
The eMaint mobile app connects your teams, whether they’re sending off a work request on the factory floor or completing a work order at an offline worksite.

Missing info and siloed teams lead to maintenance nightmares—that’s where a mobile CMMS comes in.

Mobile saves time, unites teams, and makes life easy
Take care of work orders, approve work requests, and book parts in the field. Snap a photo, check off routine inspection tasks, and access key documents. Track your work hours and require digital signatures for work order completion.

Asset details are a few taps away
Find assets quickly, attach to work orders, and view work history. Scan barcodes in the field for instant asset data. Knock out many birds with one stone: you can see nearby open work orders when you’re already in the field for one of them.

Connect your team in the field and offline
Talk to your team 24/7. receive mobile push notifications for work order updates. Anyone can scan QR codes to submit work requests. Work offline in remote or network-unfriendly areas: your changes will sync automatically once a connection is re-established.
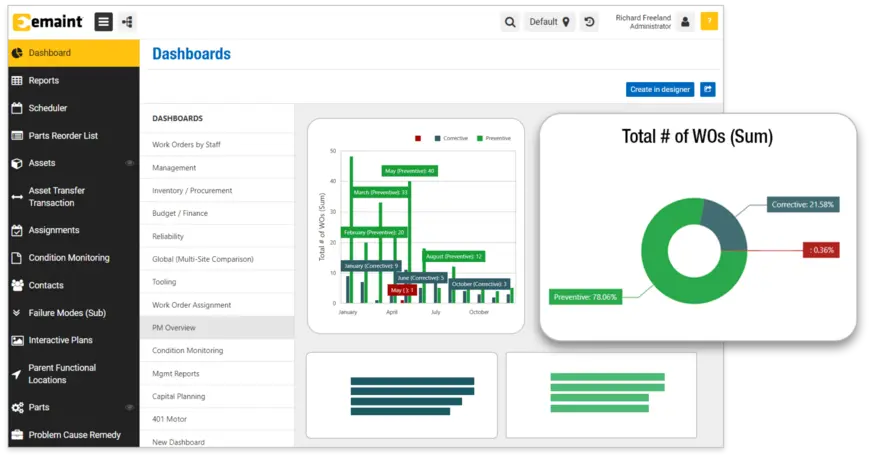
Simple, Intuitive Work Order Management Reports & Dashboards
Work order reporting and analytics are a breeze with eMaint. Manage work, track KPIs, and prepare for audits with ease.
Seamless CMMS Integration: Your Key Business Systems, Connected
Connect your CMMS to 1000+ apps, ERPs, SCADA & PLC systems, and beyond
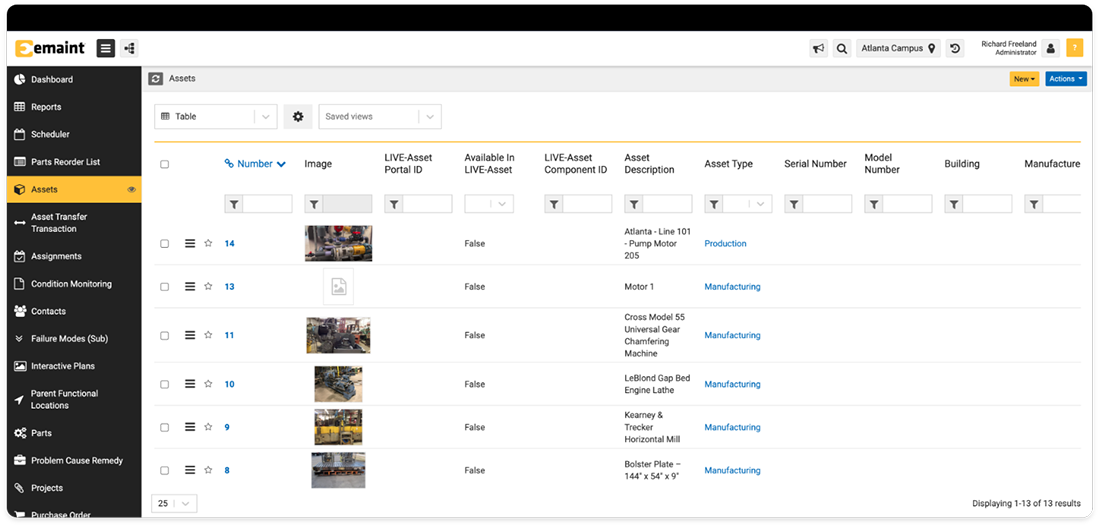
Case Studies
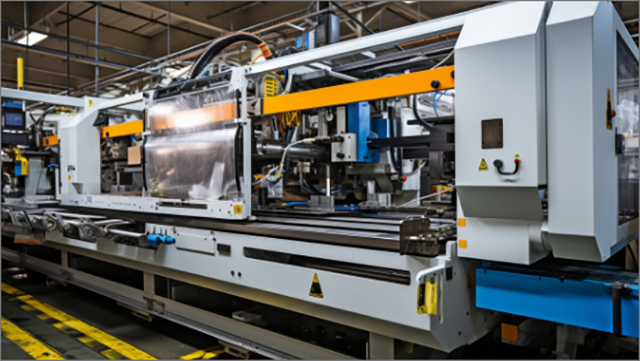
Materials Manufacturing
Whether you’re manufacturing plastics, sealants, or any other product, eMaint empowers your team to focus on preventive maintenance through easy work order management and automated reports that highlight trends and help you ensure compliance with standards like OSHA.
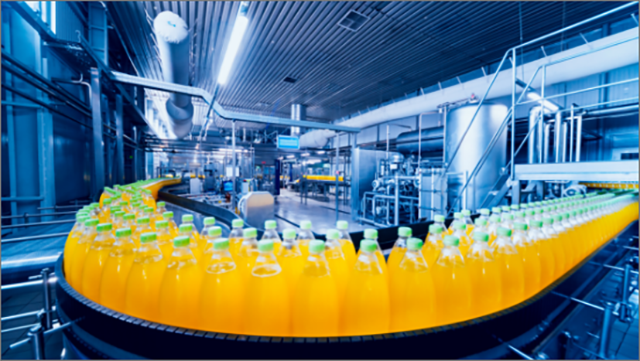
Food Manufacturing
eMaint reduces the labor that goes into maintenance planning, increases the uptime of vital assets, and makes audits effortless for manufacturers of food, beverage, and related products.
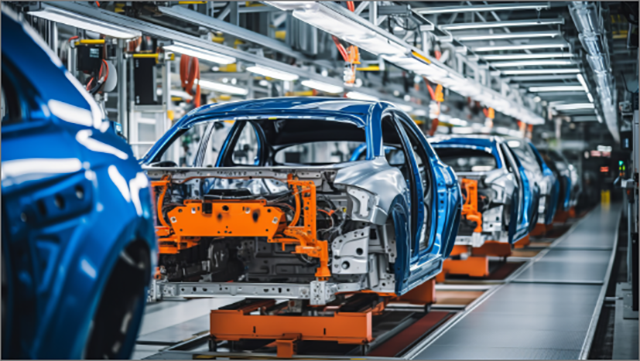
Automotive Parts Manufacturing
Manufacturers in the automotive industry, especially in the competitive electric vehicle (EV) industry, must meet rigorous quality standards and supply demands. eMaint lets you effortlessly track assets, spare parts, and machine performance so that unplanned downtime and product defects are a thing of the past.

Aviation and Aerospace Manufacturing
In the aviation industry, where product quality and total reliability are paramount, maintenance overtime often runs rampant. eMaint is designed to simplify work order management to reduce administrative overhead, boost uptime, and achieve best-in-class performance.
You don’t have to be a data analyst to gain powerful, revenue-driving insights from eMaint.

Take the helm of a work order command center
Easily build dashboards that give you quick insight into your team’s daily work. See work order status and completion rate at a glance. Look at your maintenance schedule daily, weekly, or monthly view. Discover trends and action on them to strengthen reliability.

A wealth of data at your fingertips
Review work order history, PM completion, and overdue work. Establish and track maintenance KPIs for metrics like uptime, MTTR, and OEE. Find savings by analyzing wrench time, labor costs, and parts charges.

Be ready for audits and confident in your compliance
eMaint serves as a compliance hub for standardizing processes and housing documents, Establish controls, procedures, and approvals for work orders. The eMaint audit trail tracks user changes and requires e-signatures where you specify. Build dashboards that make audits painless, getting auditors in and out.