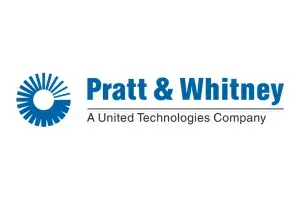
Pratt & Whitney Saved $100k On A Single Project With eMaint CMMS
Customer Since: 2015 | Industry: Manufacturing
Pratt & Whitney is a market leader in the design and aircraft engine manufacturing. The company wanted to maximize uptime, manage inventory, and develop a maintenance program to improve processes. With eMaint CMMS, on one project alone the company saved $100,000 by having the right parts on hand and three months of downtime based on past experiences.
BACKGROUND
A subsidiary of United Technologies Corporation, Pratt & Whitney is a market leader in the design and aircraft engine manufacturing. The company’s aircraft engines are widely used in both civil, commercial and military aviation. The AutoAir division of Pratt & Whitney is undergoing very exciting changes with a growth program for their energy-efficient PurePower engine. Bruce Gallagher, Maintenance Facilities Supervisor for Pratt & Whitney AutoAir, is responsible for overseeing maintenance for engine production and shipment.
THE CHALLENGE
For Pratt & Whitney, equipment uptime is the primary goal. Their legacy system required a great deal of administrative overhead, and the team experienced 12-24 hour delays in receiving corrective work orders. They did not have a method in place to assign work criticality or priority. The team wanted to develop an effective program to improve response time, assess and identify maintenance, and perform Daily Walk Arounds (DWAs). They looked for a flexible CMMS system to execute these goals and support compliance.
IMPLEMENTATION
To kick off implementation, Pratt & Whitney scheduled an onsite visit with an eMaint Sr. Consultant to assess how the system would be used for DWAs and to prioritize work requests. The team also used eMaint University to learn best practices, and leveraged the knowledge of machine operators to understand and schedule the who, what, when, where, why and how of preventive maintenance. To collect and manage data on equipment, the maintenance team uses eMaint to perform DWAs three times daily. Work orders are both texted and emailed to technicians.
Gallagher notes that his keys to successfully managing spare parts inventory are having the right team, having the right parts on hand, and correctly identifying where parts belong in a physical inventory environment. Parts are also assigned A, B or C level criticality, and stocked based on those levels.
RESULTS
On one project alone, the company saved $100,000 by having the right parts on hand and three months of downtime based on past experiences. Effective inventory management helps ensure equipment uptime, and decreases the lead time for critical spare parts. Inventory, as well as accessing reports and dashboards, enables the team to track usage and life expectancy of parts. This is critical, as uptime and PM closeout are key metrics for Pratt & Whitney.
By analyzing data from reports and dashboards, the company is no longer “going through the motions” of maintenance. Gallagher’s team is able to see how often work is being performed to explore process and efficiency problems, discuss issues with technicians and identify the root cause of downtime.
Pratt & Whitney achieved best-in-class performance for PM closeout percentage, and plants currently using eMaint serve as a model for future plants. With the control and visibility into intervals and frequency of failure, the team is able to consistently optimize PM schedules.