
Based on 268+ reviews



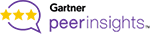
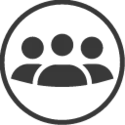
150,000+
USERS
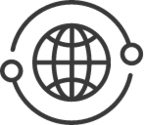
116
COUNTRIES
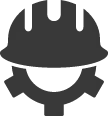
7,400+
MAINTENANCE TEAMS HELPED
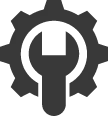
3.4 Million
MACHINES FIXED
Spare parts management is easy with eMaint CMMS.
With the right parts inventory management software, you can be confident your team is equipped with the parts they need and discover how to minimize spend while maintaining your inventory.
Be ready for unplanned downtime — when critical spares make the difference between crises averted and costly shutdowns.
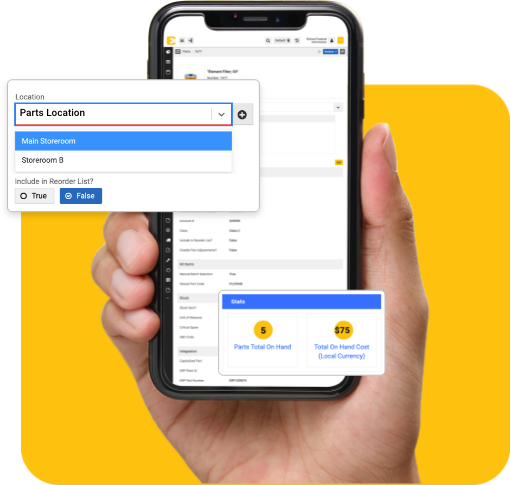
Parts Inventory Management Software, Simplified
Quickly locate and assign parts to work orders. Oversee parts inventory management and spending. Book parts in the field and offline with the mobile app.
You’re busy. Let eMaint take care of the spare parts management madness.

Spare parts at the ready
Track your spare parts, search for what you need, and easily assign to work orders. Make sure critical spares are on hand for emergencies. Your view is configurable – drag & drop columns, edit labels, and personalize your workspace.

Get inventory just right: always in stock, never out of budget
Optimize your inventory levels to prevent both shortages of critical spares and overspending on unnecessary inventory. The eMaint Parts Reorder List notifies you when parts dip below your set limits. Gain visibility on slow-moving parts orders and plan accordingly.

Our mobile app makes life easy
Manage work orders, view asset info, and book spare parts on the go with the eMaint mobile app. Take a photo of a machine failure in the field, upload it, and submit a work request – then, book relevant parts to get the job done. Work offline, your updates syncing automatically once a connection is re-established.

Simple, Drag & Drop Maintenance Scheduling for Parts Inventory Management
Manage parts assignments, work orders, and preventive maintenance with an intuitive, interactive calendar.
Eliminate the hours spent planning, cross-referencing availability, and scratching your head over schedule conflicts.

Streamlined planning: save time & make sure work is assigned
Manage and plan out maintenance. Schedule PMs to trigger based on equipment usage or asset health data. Ensure your team has the right parts for the job.

Easy, drag & drop PM calendar
Map out work orders and PMs with the eMaint Scheduler, and intuitive, interactive calendar. Assign work quickly. Make sure your assignments, schedules, and spare parts availability work in harmony.

Automatically see and resolve conflicts
Learn of schedule conflicts ahead of time with notifications, so you can resolve them right away. Get notified of overscheduling. Optimize your maintenance planning by level-loading work distribution and planning ahead for spare parts needs.
Our Global Maintenance Storeroom Has Your Back
eMaint unites your inventory across worksites, giving you access to more parts and powerful visibility.
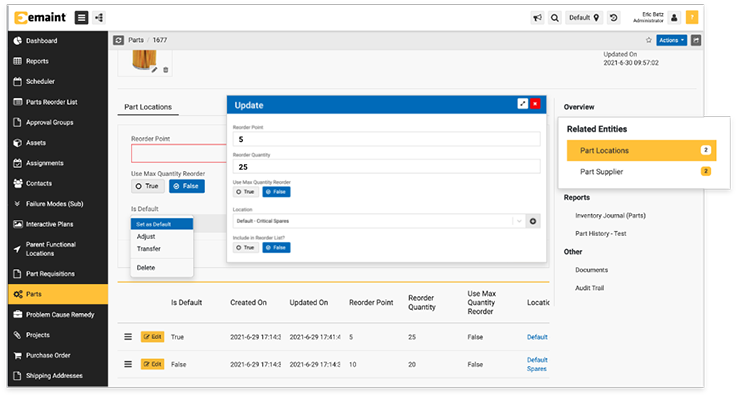
A critical asset goes down, and the spare you need is missing. Thankfully, you have eMaint.

Get what you need quickly in emergencies
Request and share spare parts across worksites in multi-site businesses. Discover if other sites have key critical spares when you need them right away and face costly downtime.

Your parts inventory command center
Manage spare parts across the enterprise. Send reqs, POs, and charges between sites. View and analyze inventory levels in individual storerooms, across regions, or throughout the organization.

Simple reporting drives powerful changes
Report on spare parts inventory with easy-to-use analytics and dashboards. Build enterprise-level reports, streamlined thanks to data standardization. Discover trends in parts charges, inventory levels, MTTR, and more maintenance KPIs that can improve strategy across the business.
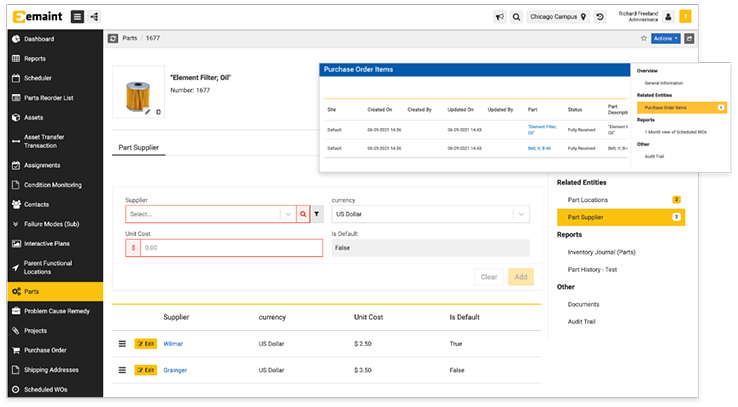
Seamless Purchasing & ERP Integration for Your Parts Inventory Management System
eMaint connects to your key business systems, from SAP to Salesforce and Power BI.
Say goodbye to data entry errors, dueling inventory systems, and complex, costly integrations

Simplified integration that unites MRO & finance
eMaint brings MRO and purchasing or finance teams together. Connect to 1000+ apps, including ERP platforms like SAP, Oracle NetSuite, or Sage Intacct. Trust in the helpful eMaint API or rely on eMaint’s low-code, iPaaS integration offering.

Track & update your inventory across software
Automatically update inventory data between eMaint and your ERP. Get rid of data entry errors. Eliminate miscommunications and confusion over maintenance vs. financial records.

Easy purchase reqs, POs, and charges
Route purchase requisitions and orders from maintenance to inventory or accounting, ensuring financial traceability for your maintenance work. Build workflows between eMaint and your accounting system to strengthen visibility on labor costs. Send parts reqs directly to purchasing to speed up process in maintenance emergencies.