By Michael Mills, Technical Solution Manager at Fluke Reliability
Updated: July 16, 2025 • Originally Posted: 2021 • 10 min read
Quick Summary: What Is Preventive Maintenance?
- Preventive maintenance, sometimes referred to as preventative maintenance or PM, is the practice of performing regularly scheduled maintenance on assets to reduce the chance of failure.
- Instead of waiting for equipment to break down, teams use planned maintenance tasks—like inspections, cleanings, and part replacements—to catch issues early, avoid costly downtime, and extend asset lifespan.
- Typical PM tasks include inspections, lubrication, calibration, and part replacements—based on time, usage, or condition.
- There are four common types: time-based, usage-based, condition-based, and predictive maintenance.
- A CMMS like eMaint helps schedule, track, and document PM tasks—turning maintenance from reactive to proactive.
Why Preventive Maintenance Matters
Preventive maintenance (or preventative maintenance) isn’t just about cutting downtime—it’s about protecting your people, your production, and operational performance across an entire facility.
By performing routine upkeep before failure occurs, maintenance teams can avoid disruptions, extend asset life, and reduce long-term costs. Whether it’s a simple oil change or a scheduled calibration, PM shifts the focus from replaces “fix it when it fails” with “fix it before it does.” The result is safer operations, stronger performance, and a more resilient facility.
In This Guide, We’ll Cover:
- Preventive vs. Reactive Maintenance
- Preventive vs. Predictive Maintenance
- The 5 Types of Preventive Maintenance
- When and How to Use Preventive Maintenance
- Preventive Maintenance Examples by Industry
- Benefits and Drawbacks of Preventive Maintenance
- How to Build a Preventive Maintenance Program
- Common Preventive Maintenance Tasks
- PM Schedules: Fixed vs. Floating
- Preventive Maintenance Software and Systems
- Preventive Maintenance FAQs
Whether you’re creating your first PM schedule or refining an existing one, this guide will give you the foundation to build a program that supports long-term reliability.
Preventive Maintenance vs. Reactive Maintenance
One of the easiest ways to understand preventive maintenance is by comparing it to the alternative: reactive maintenance. While reactive maintenance—also known as run-to-failure or corrective maintenance—waits until equipment breaks down to take action, preventive maintenance is all about staying ahead of the problem.
Instead of dealing with unplanned shutdowns, emergency repairs, and safety risks, preventive maintenance relies on scheduled tasks—based on time, usage, or condition—to prevent failure before it happens.
The point of preventive maintenance is to reduce breakdowns, improve asset reliability, and free up your team to focus on planned work.
While reactive maintenance may seem cheaper or simpler upfront, it often results in higher costs and more downtime in the long run. Preventive maintenance programs allow teams to plan ahead, reduce firefighting, and create a more reliable and efficient maintenance operation.
Preventive Maintenance vs. Predictive Maintenance
While preventive maintenance (PM) is based on fixed schedules or usage triggers, predictive maintenance (PdM) takes it a step further. Instead of servicing assets at regular intervals, predictive maintenance relies on real-time data to determine exactly when maintenance should be performed.
The key difference? Preventive maintenance (or preventative maintenance) follows a schedule. Predictive maintenance happens when the data says it should.
Condition-monitoring tools like vibration sensors or thermal imaging help identify early signs of wear, making PdM a smart strategy for critical assets.
Many modern programs use both strategies—preventive maintenance to cover the basics, and predictive tools to optimize timing and reduce over-maintenance.
5 Types of Preventive Maintenance (with Examples)
- Time-Based Maintenance (TBM): Tasks occur on a fixed calendar schedule, regardless of equipment usage.
Example: Inspect HVAC filters every 3 months to prevent airflow issues before peak season. - Usage-Based Maintenance (UBM): Tasks are triggered by actual equipment use—like hours run, cycles completed, or miles driven.
Example: Service a forklift every 200 hours to maintain safe and efficient operation. - Condition-Based Maintenance (CBM): Maintenance is performed only when sensors or inspections detect early signs of wear or failure.
Example: Replace a bearing when vibration levels spike, preventing unplanned downtime. - Predictive Maintenance (PdM): Advanced tools use real-time data and trend analysis to forecast failures in advance.
Example: Use thermal imaging to detect overheating components before they cause damage. - Prescriptive Maintenance: AI not only predicts what’s likely to fail—it also recommends the best action to take.
Example: Adjust conveyor speed and replace a seal to avoid an impending breakdown.
So how do you turn these strategies into real-world action? Let’s break down the five core types of preventive maintenance.
When and How to Use Preventive Maintenance
Preventive maintenance is best for equipment that:
- Has a known wear pattern (like belts, filters, seals)
- Plays a critical role in production, operations, or safety
- Becomes more likely to fail the longer it runs
- Can be cost-effectively maintained on a schedule
It’s not ideal for equipment with purely random failure modes (like circuit boards) or low-cost items that can be replaced quickly. That’s why not every asset needs a preventive approach—or the same kind of schedule. So when does preventive maintenance make the most sense?
Before You Begin: Key Questions to Ask
Before you start assigning tasks or building preventative maintenance schedules, take a step back and ask:
- Which assets are most critical to operations or safety?
- What maintenance tasks are needed to keep them running smoothly?
- Who will be responsible for each task—and how often?
- What tools or systems (like a CMMS) will help automate and manage the work?
Having answers to these questions up front will save time, reduce guesswork, and lay the groundwork for a stronger, more strategic maintenance PM program.
Preventive Maintenance Examples by Industry
See how PM is applied across different sectors in these real-world preventive maintenance examples:
Manufacturing
Regular lubrication and calibration of production lines, conveyors, and press machines prevent costly stoppages and support quality control.
Automotive
Fleet maintenance tasks like oil changes, brake inspections, and mileage-based part replacements help avoid unexpected vehicle downtime.
Healthcare
Scheduled testing and calibration of medical devices (like MRI machines or defibrillators) ensure accuracy, compliance, and patient safety.
IT and Data Centers
Airflow checks, UPS battery testing, and scheduled firmware updates help prevent power loss and overheating in mission-critical systems.
Construction
Routine inspections of heavy equipment like cranes and excavators, plus usage-based servicing, reduce risk on busy job sites.
Benefits of Preventive Maintenance
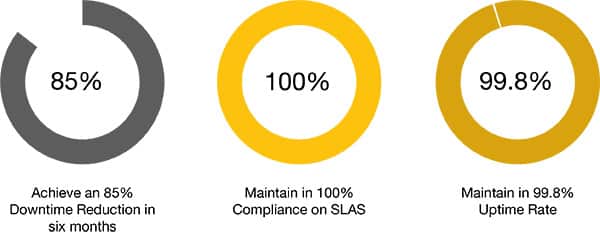
Preventative maintenance delivers tangible, long-term value to teams across every industry. Here’s what a well-run maintenance PM program can unlock:
- Increases asset lifespan
By addressing wear and tear before it leads to failure, preventive maintenance keeps equipment running longer and more reliably. - Reduces equipment downtime
Scheduled PM tasks help avoid surprise breakdowns and allow teams to plan around production windows. - Real-World Impact
Hoyt Archery used eMaint CMMS to increase preventive maintenance compliance by 77% and cut equipment downtime by 40%—all while streamlining parts inventory and auto-reordering.
👉 Read the case study - Lowers maintenance costs
Though there’s an upfront cost to planning and scheduling, PM reduces the need for emergency repairs, overtime, and expedited parts orders. - Improves workplace safety
Regular inspections and servicing reduce risks like leaks, fires, or mechanical failures that can harm personnel or damage property.“Since implementing eMaint, we’ve hit 97% on-time PM across our plant. It’s given us more control over failures and fewer surprises on the floor.”
— Asahi Kasei Plastics North America
👉 See how they did it - Streamlines resource planning
Knowing when maintenance is coming up helps teams assign the right techs, order the right parts, and avoid last-minute scrambles. - Boosts OEE and compliance
PM improves uptime, quality, and performance—all critical components of overall equipment effectiveness. - From Reactive to Reliable
L3Harris Ocean Systems improved on-time maintenance PM completion by 46%, streamlined contractor work orders, and eliminated manual audit prep—all by switching to a digital CMMS.
👉 Explore the case study
Challenges of Preventive Maintenance
- Risk of over-maintenance
- Upfront cost
- Labor requirements
- Requires cross-team buy-in
- Scheduled downtime can still impact operations
Preventive maintenance (or preventative maintenance) isn’t just a best practice—it’s foundational to effective asset care. According to the Society for Maintenance & Reliability Professionals (SMRP), preventive maintenance plays a key role within the “Equipment Reliability” pillar of its industry-standard Body of Knowledge. For organizations aiming to achieve world-class maintenance, PM is one of the most essential tools in the toolkit.
- Create an equipment inventory
Document all assets across your facility, including make, model, location, age, and usage data. This gives you a complete picture of what needs maintaining. - Prioritize critical assets using asset criticality analysis
Focus your efforts where failure would hurt most—on equipment tied to production, safety, compliance, or cost. Rank assets by their risk and importance. - Refer to OEM guidelines
Use manufacturer recommendations to set baseline maintenance intervals and service tasks. These are a good starting point before you adapt to your environment. - Choose maintenance triggers
Decide how you’ll schedule PM—based on time (e.g., every 90 days), usage (e.g., 500 run hours), or condition (e.g., vibration thresholds). - Build a PM schedule
Lay out daily, weekly, monthly, and annual maintenance plans. Assign responsibilities, parts, and tools so that nothing gets missed. - Use a CMMS to manage schedules and track completion
A CMMS simplifies scheduling, tracks work history, generates work orders automatically, and helps teams stay organized—especially as you scale.
Once your core preventative maintenance process is up and running, it’s time to fine-tune your approach with advanced scheduling options—and ensure your overall strategy supports long-term uptime and efficiency.
Common Preventive Maintenance Tasks
As your program matures, certain routine tasks will show up again and again—regardless of industry. These recurring PM actions form the backbone of any solid maintenance strategy and are often bundled into reusable checklists or digital work orders.
Typical examples include:
- Replacing worn belts or bearings
- Cleaning filters, ducts, and vents
- Lubricating moving parts
- Inspecting and tightening fasteners or electrical connections
- Testing emergency systems (e.g., alarms, backups)
- Checking for compliance issues or wear patterns
Want to make these tasks easier to manage? Here’s how to create a preventive maintenance checklist that keeps your team on track.
Of course, what matters just as much as what you do is when you do it—which is where scheduling strategies come in.
PM Schedules Explained: Fixed vs. Floating
Most programs use a combination of fixed and floating schedules. Fixed schedules trigger maintenance at consistent intervals (e.g., every 30 days), while floating schedules shift based on the completion of previous tasks.
Both have their place when matched to the right type of preventive maintenance. If you’re unsure how to manage both, preventive maintenance software can help automate the entire process and keep your team on track.
So how do you choose the right approach? That starts with understanding the five main types of preventive maintenance and how each one fits into your overall strategy.
Preventive Maintenance Software and Systems
As your PM program grows, managing it manually—using spreadsheets, paper logs, or memory—quickly becomes unsustainable. That’s where preventive maintenance software comes in.
A CMMS (Computerized Maintenance Management System) is software that centralizes and automates maintenance workflows. It simplifies scheduling, tracks work history, generates work orders automatically, and helps teams stay organized—especially as you scale.
A CMMS helps teams:
- Create PM schedules
- Automate work order generation and assignments
- Track task completion
- Store checklists and documentation
👉 What should you consider before selecting a CMMS?
For larger or growing facilities, preventive maintenance software is the backbone of a scalable PM program.
Looking for a preventive maintenance solution?
Let us put our experience to use for you.
Let us put our experience to use for you.
About the Author
Michael Mills is a Technical Solutions Manager at Fluke Reliability, leading a team of solutions engineers dedicated to innovation and excellence in applying maintenance, reliability, and operations (MRO) strategies to CMMS and EAM implementation. With over a decade of experience in Enterprise Asset Management (EAM), Reliability Centered Maintenance (RCM), Condition-Based Maintenance (CBM), Integrated Condition Monitoring (ICM), Mills is an authoritative thought leader in the realms of asset management, mobile CMMS deployment, and IIoT monitoring.
Preventive Maintenance FAQs
1. What is an example of preventive maintenance?
A common example is changing HVAC filters every three months or rotating vehicle tires every 10,000 miles—both pre-emptively prevent wear-related failures.
👉 Related: 5 Preventive Maintenance Examples in Action
2. How do I create a preventive maintenance plan?
Start by listing your equipment, ranking assets by criticality, and referring to OEM guidelines for service intervals. Then build a schedule using time-, usage-, or condition-based triggers. A CMMS can automate work orders, track history, and keep your plan on track.
👉 Related: How to Build a Preventive Maintenance Program
3. What’s the difference between preventive maintenance and predictive maintenance?
Preventive maintenance is scheduled at fixed intervals, whereas predictive maintenance uses real-time data (like vibration or temperature) to trigger tasks when they’re actually needed.
👉 Related: Preventive vs. Predictive Maintenance
4. What types of equipment benefit from preventive maintenance?
Assets that wear over time—like motors, HVAC systems, pumps, and fleet vehicles—are ideal for PM. If failure is likely to disrupt operations or pose safety risks, preventive maintenance is worth considering.
5. What tools are used in preventive maintenance?
Key tools include inspection checklists, temperature/vibration sensors, lubrication tools, and a CMMS. A CMMS centralizes scheduling, documentation, and asset history.
👉 Learn more: Best Preventive Maintenance Software
6. Is preventive maintenance always cost-effective?
Not always. For low-cost or non-critical assets, reactive maintenance may make more sense. But for most equipment, the long-term savings from reduced downtime and emergency repairs outweigh the upfront planning effort.
7. What industries use preventive maintenance the most?
From global manufacturers and utility companies to hospitals and data centers, preventive maintenance (or preventative maintenance) supports uptime, safety, and compliance across sectors. Even construction firms and logistics providers rely on structured PM to protect equipment and crews.
8. What are PM checklists and how do they work?
PM checklists guide technicians through routine maintenance steps—like inspections, cleanings, or part replacements. A CMMS can store reusable checklists to standardize quality and ensure nothing gets missed.
👉 Learn more: What Is a Work Order?
9. What are the main goals of preventative maintenance?
The main goals are to reduce unexpected equipment failures, extend asset life, improve safety, and lower overall maintenance costs. Preventative maintenance helps teams move from reactive “firefighting” to planned, efficient upkeep that supports operational stability.
10. How often should preventive maintenance be performed?
The ideal frequency depends on the asset type, manufacturer recommendations, usage levels, and criticality. For example, HVAC filters might be checked every 3 months, while high-use equipment could require weekly or even daily tasks.
11. What’s the difference between preventive and corrective maintenance?
Preventive maintenance happens before a failure occurs—based on time, usage, or condition. Corrective maintenance happens after something breaks. While corrective fixes are sometimes unavoidable, a strong PM program helps reduce the need for them.
12. Can preventative maintenance reduce downtime?
Yes. Regular PM tasks help catch issues early and reduce surprise breakdowns. Teams that prioritize preventative maintenance typically see shorter outages, fewer emergency repairs, and more control over production schedules.
Ready to Build Your Program?
Explore More:
Want to see how preventive maintenance works in real facilities?
👉 Browse eMaint customer success stories
Talk to an Expert:
Need help building your PM program?
👉 Request a CMMS walkthrough