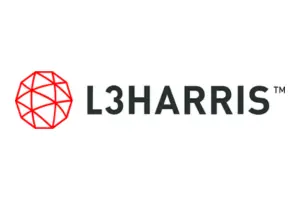
U.S. defense firm retrains on eMaint to optimize usage, eliminate paper, streamline compliance
Customer Since: 2012 | Industry: Defense
L3Harris, based in Melbourne, Fla., delivers advanced defense and commercial technologies across air, land, sea, space, and cyber domains. It is the seventh-largest defense contractor in the world, according to a 2018 list published by the Stockholm International Peace Research Institute.
In 2012, the company implemented eMaint Computerized Maintenance Management System (CMMS) software to streamline maintenance at its Ocean Systems facility in Southern California. The business unit manufactures sonar and acoustic sensing and tracking systems.
The CMMS was not consistently optimized, and as a result, became overburdened with unresolved PM work orders and outdated asset information. In November 2019, business-unit facility management personnel attended an intensive five-day eMaint CMMS boot camp retraining event. Upon completion, the team harnessed the system’s extensive capabilities to enable a fully compliant PM tracking system.
BACKGROUND
L3Harris, a Tier 1 supplier to commercial and military industries, performs various domestic and international defense contract work and services. In 2012, eMaint CMMS was selected to help manage and maintain equipment at the 253,000-square-foot Ocean Systems facility in Sylmar, Calif., about 35 miles northwest of Los Angeles.
Bill Knaack, Product Support and Assurance Director for L3Harris’ Sylmar business unit, manages quality, environmental health and safety, industrial security, and the company’s continuous improvement program. Due to colleague retirements, he now oversees the Ocean Systems facility’s internal and external maintenance, including its cooling towers, pumps, air handlers, humidifiers, HVAC infrastructure, and roof.
THE CHALLENGE
Along with the maintenance responsibilities, Mr. Knaack inherited a powerful but inefficiently leveraged eMaint CMMS. He also faced a consistent string of disappointing internal audit reviews. Although the needed regulatory tasks were performed and documents assembled for external audits, the maintenance team could not produce the more in-depth proof that corporate leaders at L3Harris required.
Mr. Knaack explored the eMaint CMMS capabilities and recognized that the system could solve many problems—such as managing the thousands of unclosed work orders, updating the asset list, and filtering out irrelevant data.
IMPLEMENTATION
Fortunately, when the business unit’s data was initially entered into eMaint, it was structured and set up correctly, making necessary extractions simple. With the help of an eMaint expert, the Sylmar maintenance team swiftly eliminated out-of-service equipment, PMs attached to inactive assets, and obsolete work orders.
“We blew out every PM that no longer had an active piece of equipment and added a significant number of assets that were not captured in the legacy database,” Mr. Knaack says. “We eliminated all work orders that were obsolete and reduced our active PM list from 714 to 432.”
RESULTS
CMMS users now manage Ocean System facility equipment and associated documents, including critical regulatory compliance data, instantly using eMaint.
“We’re strictly using this program to set up and maintain our PMs, our procedures, and our work orders for both preventive maintenance and corrective maintenance. We use it to maintain our document repository of all of the artifacts of completion, which now makes auditing the system a snap,” Mr. Knaack says.
Ocean Systems employs contractors regularly. Because the CMMS is configured to automatically send a notification when it’s time for preventive maintenance, eMaint easily tracks contractor work and can attach or retrieve relevant work order data and quickly create reports.
“Now, the auditor comes in, and he says, ‘Show me your last cooling tower PM.’ I go to work orders; I filter on historical, I filter on the contractor who does the cooling towers, I pull up the last one, take him to the linked document, I open it up, he checks a box. Done. Next.”
– Bill Knaack, Product Support and Assurance Director, Sylmar, Calif., business unit, L3Harris