Dia após dia, os gestores de instalações são pressionados a manter as operações a funcionar sem problemas e de forma eficiente. Mas é difícil progredir quando se está preso no modo reativo, resolvendo os problemas à medida que surgem, sem um sistema claro em vigor.
É aí que entram as avaliações estruturadas. Ao fornecerem um quadro para medir o desempenho, acompanhar o progresso e identificar as áreas a melhorar, estas avaliações fazem mais do que apenas aferir o sucesso - criam um roteiro para melhores resultados.
As avaliações estruturadas criam transparência ao fornecerem scorecards partilhados regularmente, para que todos os membros da equipa tenham acesso a actualizações regulares do progresso e saibam o que se espera que seja alcançado. Este alinhamento promove uma compreensão partilhada dos objectivos a todos os níveis da organização. E embora cada instalação seja diferente, as avaliações estruturadas são flexíveis. A estrutura certa pode adaptar-se às necessidades e desafios únicos da sua equipa, tornando-a uma ferramenta prática para impulsionar um progresso significativo.
Neste guia, vamos explicar como funcionam as avaliações estruturadas e porque é que são a chave para aumentar a eficiência, reduzir o tempo de inatividade e obter resultados mensuráveis.
Porque é que os gestores de instalações necessitam de avaliações estruturadas
Os gestores de instalações lidam com sistemas complexos em que mesmo as pequenas ineficiências podem transformar-se em custos significativos. Embora provavelmente já tenha processos para acompanhar o desempenho, as avaliações estruturadas elevam esses esforços, fornecendo uma abordagem abrangente e escalável.
As avaliações estruturadas adoptam uma abordagem dupla: Destacam as lacunas no desempenho e ajudam-no a ir mais fundo para descobrir as causas fundamentais dos problemas recorrentes. Por exemplo, o seu tempo de inatividade frequente tem realmente a ver com uma falha do equipamento, ou é um sinal de falta de formação do pessoal ou de esquecimento dos planos de manutenção? Uma avaliação pode ajudar a esclarecer as ineficiências do processo.
Estas avaliações são particularmente valiosas em operações com vários locais, onde a normalização pode permitir comparações significativas entre instalações. Simultaneamente, a estrutura de avaliação adapta-se às realidades de cada local, alcançando um equilíbrio entre consistência e flexibilidade.
Mas como é que se sabe o que avaliar? E como é que pode centrar as suas avaliações no que é mais importante? A secção seguinte apresenta um quadro de métricas práticas para orientar as suas avaliações
Critérios-chave para avaliações eficazes
Embora não exista uma fórmula única para avaliar uma instalação, aqui estão sugestões práticas de critérios e uma explicação de como eles ajudam. Quer se trate de melhorar a segurança, simplificar a manutenção ou aumentar a eficiência operacional, estes critérios podem ajudá-lo a avaliar o que precisa de ser corrigido nas suas instalações.
1. Segurança e qualidade
- Métricas de segurança: A taxa total de incidentes registáveis (TRIR) acompanha o número de lesões registáveis por cada hora de trabalho do empregado. Esta métrica dá uma imagem global do desempenho da segurança, mas o valor vem da forma como é utilizada. Quando os incidentes ocorrem, a eficácia com que são investigados, e que medidas preventivas são aplicadas para evitar a repetição de acontecimentos? Os seus processos de segurança estão a cumprir os objectivos da empresa? A inclusão da TRIR nas avaliações também pode ajudar a comparar as instalações, destacando os locais que podem necessitar de formação adicional ou de afetação de recursos.
- Métricas de qualidade: Os defeitos por milhão de oportunidades (DPMO) constituem uma forma concreta de controlar e melhorar a qualidade dos produtos. As tendências dos defeitos estão a ser acompanhadas de perto em cada fase da produção? Que medidas estão em vigor para identificar problemas recorrentes e abordar as causas subjacentes? A inclusão de análises de qualidade regulares ou de comparações entre fábricas pode aperfeiçoar ainda mais as normas de produção e identificar desafios comuns.
- Pessoal e competências de manutenção: As avaliações podem revelar lacunas tanto a nível de pessoal como de competências, começando pelas descrições das funções de manutenção. Estas descrições descrevem claramente os requisitos técnicos de cada função? São ativamente utilizadas durante o processo de contratação? Estes são pontos relativamente fáceis de seguir, uma vez que as instalações podem frequentemente fornecer provas objectivas para mostrar o alinhamento entre as funções e as necessidades operacionais.
Outra área a avaliar é o conjunto de competências da sua equipa de manutenção. Os técnicos conseguem resolver problemas de PLCs em várias plataformas, ler esquemas ou gerir sistemas complexos como circuitos AC/DC?
Os níveis de pessoal são igualmente importantes - se uma instalação estiver a funcionar apenas com 50% da capacidade de manutenção, como é que as tarefas preventivas e as reparações estão a ser geridas sem agravar os atrasos?
A formação e o desenvolvimento da manutenção também merecem atenção. Os técnicos estão a receber a formação contínua de que necessitam para lidar com a evolução das tecnologias e dos requisitos do equipamento? Sem formação regular, as equipas correm o risco de ficar para trás, levando a reparações mais lentas, maior tempo de inatividade e custos operacionais mais elevados.
2. Eficiência operacional
- Margem bruta percentual: A margem bruta mede a eficiência financeira através do controlo da relação entre os custos de material e de mão de obra e a produção. Como é que a sua margem bruta se compara com os valores de referência da divisão? As ineficiências na utilização de materiais ou de mão de obra estão a prejudicar a margem bruta? A avaliação da margem bruta também fornece informações sobre se as suas instalações estão a cumprir os objectivos financeiros a longo prazo, especialmente à medida que a produção aumenta.
- Percentagem de tempo de resposta completo (OTIF): A OTIF monitoriza a fiabilidade da entrega, tornando-a um indicador valioso do alinhamento dos processos de produção e da cadeia de fornecimento. Os produtos são consistentemente entregues a tempo e de acordo com as especificações? Que estrangulamentos na produção, embalagem ou expedição estão a afetar a OTIF? Adicionar esta métrica às avaliações também pode ajudar a sua equipa a compreender os desafios que se colocam aos clientes e a melhorar a colaboração entre departamentos.
- Percentagem de sucata: As taxas de refugo realçam as ineficiências na produção e no manuseamento de materiais, oferecendo uma oportunidade para identificar custos ocultos. Analise mais de perto as causas da sucata na sua operação, quer se trate de estrangulamentos no processo, falhas no equipamento ou erros do operador. Acompanhe também as medidas implementadas para reduzir os resíduos e a forma como os impactos são medidos. As instalações também podem monitorizar a forma como o refugo varia entre turnos, máquinas ou materiais para identificar inconsistências.
- Perda de inventário: As discrepâncias de inventário sinalizam frequentemente problemas operacionais mais graves, desde controlos deficientes a má gestão ou danos. Verifique se os registos de inventário são regularmente reconciliados com a utilização real. Que medidas estão em vigor para resolver quaisquer discrepâncias? A inclusão de rastreio tecnológico, como RFID ou código de barras, pode aumentar ainda mais a precisão do inventário e reduzir as perdas.
3. Manutenção e desempenho do equipamento
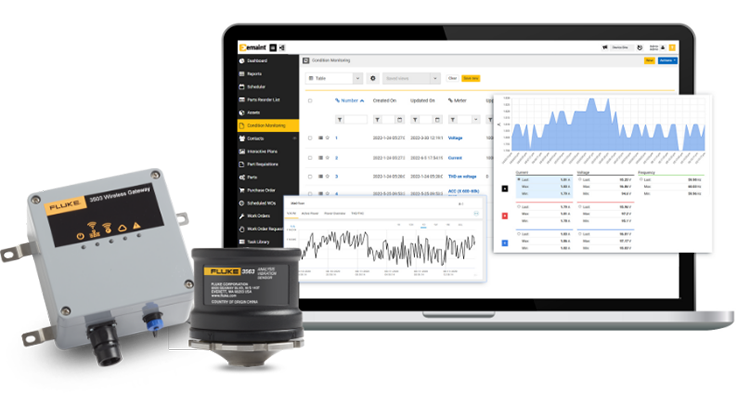
O Emaint ajuda as equipas das instalações a acompanhar o desempenho do equipamento de manutenção
- Cumprimento da PM: A conformidade da manutenção preventiva (PM) verifica se as tarefas programadas são concluídas a tempo. Os atrasos nas tarefas de PM aumentam o risco de tempo de inatividade não planeado, pelo que as avaliações devem considerar se as tarefas em atraso estão a ser priorizadas de forma eficaz.
E lembre-se, a conformidade com a PM não se trata apenas de cumprir um calendário - trata-se de aperfeiçoar constantemente o processo. Por conseguinte, esta métrica de avaliação pode incluir se a sua equipa está a utilizar os conhecimentos obtidos a partir das avarias e do feedback das máquinas para melhorar a qualidade das suas tarefas de PM. Por exemplo, as peças que falham frequentemente estão a ser inspeccionadas ou substituídas de forma mais proactiva? Será útil para a melhoria contínua incluir este nível de detalhe nas revisões de PM. - Rastreamento de ordens de serviço: As ordens de trabalho são uma ferramenta essencial para o acompanhamento das tarefas de manutenção, mas a sua eficácia depende dos pormenores que recolhem. Assim, para esta métrica de avaliação, pode considerar se as ordens de trabalho são consistentemente fechadas com notas suficientes, incluindo a análise da causa principal, para resolver problemas recorrentes. As instalações também podem avaliar se as equipas de manutenção estão a comunicar eficazmente os prazos de resolução.
Este critério também pode incluir a avaliação da eficácia da utilização do seu sistema de gestão de manutenção computorizado (CMMS). Por exemplo, as peças sobresselentes críticas são controladas e substituídas com precisão, evitando o tempo de inatividade causado por faltas? - Tempo de funcionamento do equipamento: Acompanhe a forma como as estratégias de manutenção preditiva ajudam a antecipar e a minimizar o tempo de inatividade. Que padrões nos eventos de inatividade podem orientar as melhorias do processo? A sua equipa de instalações também pode considerar a forma como os objectivos de tempo de funcionamento variam entre tipos de equipamento e, mais importante, se são realistas tendo em conta as restrições operacionais.
- Tempo médio de reparação (MTTR): As avaliações do tempo médio de reparação podem revelar padrões nas avarias que indicam problemas sistémicos, como falhas recorrentes no mesmo equipamento ou métodos de reparação ineficazes. Comece por investigar a eficácia com que os tempos de reparação são controlados e analisados para identificar os estrangulamentos. Os atrasos são causados por desafios de diagnóstico, disponibilidade de peças sobresselentes ou ineficiências do fluxo de trabalho? O controlo do MTTR também pode ser associado à avaliação do CMMS.
- Gráficos de escalonamento: Pode parecer uma métrica invulgar, mas um gráfico de escalonamento é um fator de mudança para manter as operações no caminho certo. A questão-chave é: os operadores conhecem os prazos e as etapas para o encaminhamento dos problemas? As funções e responsabilidades estão claramente definidas para eventos críticos?
Imagine que um operador se depara com um problema de processo, como um ativo que não funciona. Um gráfico de escalonamento pode definir um período de 15 minutos para escalonar o problema para um líder, que tem mais 30 minutos para o resolver antes de envolver a manutenção ou o apoio da supervisão.
O sistema é suficientemente flexível para lidar com diferentes tipos de problemas. Um incidente de primeiros socorros pode necessitar de um escalonamento imediato para as equipas de segurança, enquanto um estrangulamento na produção pode seguir um caminho mais escalonado. Ao incluir gráficos de escalonamento nas avaliações, pode identificar lacunas na comunicação que possam estar a atrasar as respostas. - Manutenção autónoma: Esta prática coloca o ónus sobre os operadores de máquinas para fazerem reparações básicas e manutenção nas máquinas que utilizam todos os dias. A revisão do protocolo de manutenção autónoma ajuda a estabelecer uma maior supervisão sobre se os técnicos têm as ferramentas, a formação e o apoio necessários para desempenhar estas responsabilidades de forma eficaz e consistente.
Enquanto gestor de instalações, deverá documentar se os operadores têm listas de verificação detalhadas para orientar as suas tarefas durante a sua avaliação. Além disso, é importante verificar se cada membro da equipa está a participar ativamente nas actividades de manutenção preventiva. Por exemplo, quando uma linha é encerrada para uma PM, os operadores estão a trabalhar em conjunto com as equipas de manutenção para concluir as tarefas de forma eficiente? - Auditorias periódicas da manutenção autónoma: Não se esqueça de que a liderança desempenha um papel fundamental para garantir que os processos de manutenção autónomos são seguidos de forma consistente. As auditorias e avaliações periódicas podem ajudar a destacar as áreas de melhoria destas práticas.
As verificações de avaliação também mostram aos operadores que os seus esforços são importantes e que as suas responsabilidades de manutenção são levadas a sério. Mas, na sua essência, as verificações regulares indicam que a manutenção autónoma é uma responsabilidade partilhada e essencial para o sucesso da instalação. - Análise da causa raiz (RCA): Esta métrica identifica os factores de falha ocultos, abrindo caminho para melhorias significativas e duradouras. Pergunte a si próprio: quando o equipamento falha, o ativo é simplesmente reparado ou as equipas investigam a razão da falha? Com que frequência é que as avarias são analisadas quanto às suas causas principais?
Pode dar um passo em frente e investigar se as avarias recorrentes indicam falhas nos seus protocolos de manutenção e se os calendários de manutenção estão a ser revistos e actualizados com base neste feedback para melhorar o desempenho. Analise também a fiabilidade das peças - determinados componentes estão a falhar com mais frequência do que o esperado, e será que essas falhas indicam problemas mais profundos no fornecimento ou na aplicação? As respostas a perguntas como estas ajudarão a identificar problemas sistémicos, a aperfeiçoar as decisões de compra e a criar processos mais resistentes.
As soluções de diagnóstico de manutenção, como o Azima, podem simplificar este esforço, identificando as causas principais através de uma monitoramento de condição avançada monitoramento de condição e de uma análise preditiva baseada em IA. Da mesma forma, soluções como o eMaint CMMS incorporam a análise da causa raiz diretamente nas ordens de trabalho. Por exemplo, as equipas não podem fechar uma ordem de trabalho até que uma causa raiz tenha sido documentada, garantindo que ninguém salta este passo crítico.
Transformar as ideias em acções
As avaliações estruturadas fazem mais do que destacar lacunas - fornecem um roteiro para passar do ponto em que se encontra atualmente para o ponto em que pretende estar. No final do processo, as equipas devem emergir com um plano claro e acionável que delineia os passos mais importantes para melhorar o desempenho.
O objetivo não é sobrecarregar as equipas com tudo o que precisa de ser resolvido. Em vez disso, as avaliações ajudam a concentrar-se nos objectivos de maior prioridade que farão a maior diferença. Por exemplo, uma fábrica que se debate com o tempo de inatividade pode aperceber-se de que aperfeiçoar o seu processo de manutenção preditiva ou abordar a gestão de peças sobresselentes produziria as maiores melhorias.
Estes passos direcionados transformam as avaliações numa ferramenta orientada para o futuro. Ao centrarem-se nas acções críticas que mais contribuem para a mudança, os gestores de instalações podem alinhar as suas equipas e afetar recursos onde estes têm maior impacto.
Conclusão
Os gestores de instalações operam num ambiente em que a precisão e a consistência são a base de tudo. As avaliações estruturadas fornecem o enquadramento necessário para eliminar o ruído operacional, abordar as ineficiências e definir objectivos significativos. Não se trata de extras opcionais; são essenciais para impulsionar um progresso mensurável em sistemas complexos.
O trabalho não termina com o diagnóstico. Para obter resultados duradouros, os gestores de instalações devem ligar os dados à estratégia, capacitar as suas equipas e institucionalizar a mudança. As avaliações estruturadas oferecem um caminho claro para avançar - mas o impacto depende da eficácia com que são utilizadas.
Lembre-se, não se trata de perseguir a perfeição. Trata-se de fazer escolhas deliberadas e informadas que posicionem as suas instalações para uma melhoria contínua. A questão não é se deve implementar avaliações estruturadas, mas sim quando é que pode começar.
Este artigo baseia-se inteiramente nos conhecimentos partilhados por Dennis Hughes, gestor de projectos, equipa central de operações comerciais da Pregis LLC, durante a sessão Xcelerate 24, "Definir a Fábrica do Ano - Benchmarking interno das fábricas"