What is Asset Performance Management (APM)?
Asset Performance Management (APM) refers to a strategic methodology employed by businesses to enhance the efficiency and reliability of critical assets utilized in daily operations. Companies leverage APM to optimize the functionality of diverse assets such as infrastructure, machinery, vehicles, and digital systems to maximize productivity and minimize downtime.
APM, is all about pairing modern maintenance software with technology like sensors to amplify asset management. Collecting condition monitoring data and analyzing it with software analytics can help reduce asset failures and unplanned downtime, and ultimately extend an asset’s useful life.
Most maintenance teams already utilize a Computerized Maintenance Management System. CMMS software puts all of an organization’s maintenance information, processes, and tasks in one place. From work orders to inventory management and much more, CMMS software is a vital component of optimizing a maintenance strategy. Asset Performance Management software takes CMMS to the next level by feeding in real-time machine health data.
When you know how and when your assets are likely to fail, you can plan and take action, reduce risks, and increase your reliability.
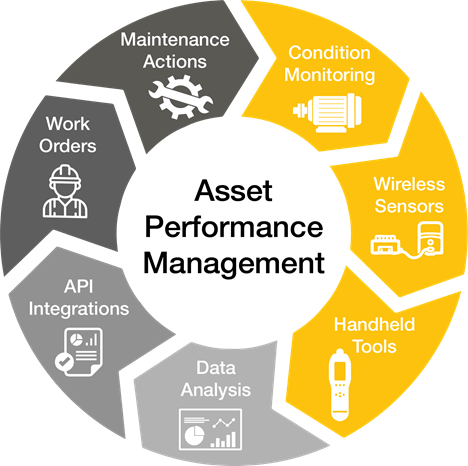
Asset Performance Management and Predictive Maintenance
Today, maintenance teams are increasingly turning to predictive maintenance. By using condition monitoring sensors and software to monitor asset health, they can catch potential failures before they cause damage or unplanned downtime.
A recent study by the Deloitte Analytics Institute showed that, “On average, predictive maintenance increases productivity by 25%, reduces breakdowns by 70% and lowers maintenance costs by 25%.”
Productivity, uptime, unplanned downtime, and maintenance costs are a few metrics organizations can track to learn how effective their maintenance strategy is. When a team is tracking their metrics and monitoring their effectiveness, they can find opportunities for continuous improvement.
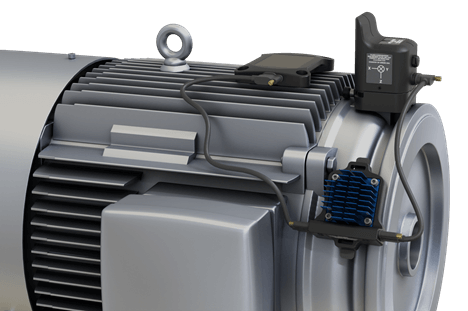
Integrating Condition Monitoring sensors and software
However, many organizations have cobbled together an ad hoc suite of tools over the years to manage and monitor their assets. This increases the likelihood of blind spots, where organizations are missing out on key insights about their assets. Operational silos keep teams from being able to truly leverage asset performance management.
As a result, it’s critical to integrate all of your tools into a centralized system to gain accurate insights and have a clear sense of priorities to act on. APM makes that possible.
What are the benefits of using APM software?
With Asset Performance Management software, it’s possible to turn data into insights. Data alone is not truly valuable until it is given context—and made actionable. APM makes it easier to make better decisions and take the right actions at the right times.
Making the most of asset performance means reducing the costs and risks at all stages of an asset’s lifecycle, from design to decommissioning. APM helps teams use real-time knowledge to not just tackle today’s challenges, but to look ahead and prepare to handle tomorrow’s.
How to leverage Asset Performance Management
An increasing, and increasingly accessible, number of technologies are shaping asset performance management today and making it possible for more teams to make the most of their assets.
Data
Cloud storage
Condition monitoring sensors
Artificial intelligence
Augmented reality
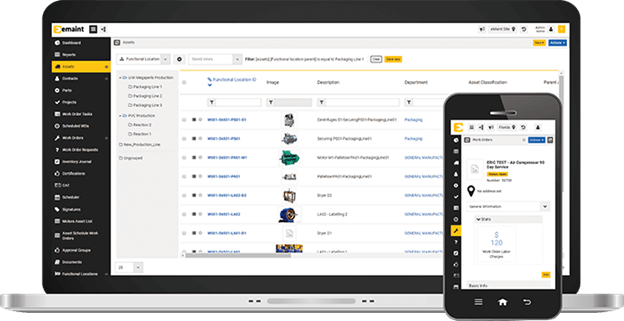
What is the difference between APM and EAM?
Enterprise Asset Management (EAM) is a strategy, not a software. Following an EAM strategy helps organizations monitor and track their assets and overall asset health in order to maximize asset performance and lifespan. Work order management is one of the key elements of EAM. Digital management of work orders increases on-time work completion, improves response times, and streamlines the process of maximizing peak performance.
EAM, as indicated by “enterprise,” has a wide scope that goes beyond asset lifecycle management to include areas such as safety initiatives and financial management. And “assets” can refer to anything from machine components to buildings and plants. Assets are simply physical assets an organization needs to carry out its mission. EAM is a broad strategy that touches many areas of an organization.
APM, on the other hand, is different in two main ways. It has an explicit focus on helping organizations reach operational excellence by getting the most out of every asset. The insights and decisions that APM focuses on are those that maximize asset availability and uptime. The other way APM is different from EAM is that it is more focused on real-time insights and data about assets, and less on record-keeping and communication.
Remote Condition Monitoring, done at scale, is one way organizations can gain the real-time insights into asset health they need in order to keep their assets operating at peak performance.
As technologies such as AI and condition monitoring sensors become more and more accessible, APM will be an attainable strategy for more organizations.
How to implement APM software
Demand for APM software is increasing as more organizations realize the value of combining software and sensors to maximize asset performance. APM software helps asset-intensive organizations get a connected, centralized view into all of their assets and their needs.
To make the most out of an APM software implementation, your organization will need to pilot and adopt IIoT technologies like vibration sensors that can monitor assets. You’ll also need to find a maintenance software that can integrate that machine health data with your organization’s other maintenance management processes.
The implementation process looks different for every organization, though the markers of success are often the same. Clearly-defined needs and goals are crucial to a successful implementation. Identify specific places where you seek to improve—such as reducing spending in a particular area of your maintenance budget—in order to help focus your work and planning during the implementation process.
The two main factors that contribute to failed implementations are poor project planning and lack of long-term vision.