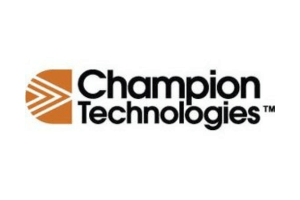
Champion Technologies Finds eMaint CMMS a Breath of Fresh Air; Generates Documentation to Meet Regulatory Compliance Demands
Customer Since: 2007 | Industry: Oil & Gas
Champion Technologies is an environmentally responsible global oilfield production chemical company. Champion Technologies needed a system for maintenance requests and work orders, as they were issued only by word of mouth and a paper process. The company chose eMaint to better manage tracking information, and maintain accountability. Champion uses the eMaint Scheduling Tool daily to assign and reassign work orders, generate reports, keep track of work orders and to document maintenance history of assets.
BACKGROUND
Champion Technologies is an environmentally responsible global oilfield production chemical company. In 2007 Texas-based Champion successfully rolled out eMaint CMMS in four Texas facilities and subsequently rolled out eMaint at sites in Canada, Brunei and Scotland. The Fresno, TX plant, Champion’s largest manufacturing and blending facility, was one the original sites included in the initial 2007 roll-out of the eMaint CMMS System.
THE CHALLENGE
Prior to the implementation of eMaint CMMS, maintenance requests and work orders were issued by word of mouth and a paper process. These rudimentary processes did not allow for any historical tracking of information on the maintenance activities performed at the facility. It was essential to maintain accountability for all maintenance activities performed throughout the facility in order to meet stringent environmental standards and safety regulations.
IMPLEMENTATION
Champion began by importing over 800 assets—including tanks, pumps, reactors and forklifts—and defining calendar-based PM schedules for the tanks and pumps. Champion uses the eMaint Scheduling Tool daily to assign and reassign work orders.
Subject to numerous environmental and safety audits from both internal departments and outside agencies, Champion uses the reporting tool to generate reports needed for regulatory and ISO compliance. To meet the Responsible Care Audit environmental standard, Champion pulls all key information documenting maintenance history of assets to meet their air quality and environmental compliance objectives. Champion also uses eMaint CMMS to manage work requests from all operations and engineering personnel. eMaint CMMS keeps track of work orders including repairs, PM’s, inspections and engineering projects.
BENEFITS
“Our Planner/Scheduler relies on eMaint as a scheduling tool to prioritize, assign, and adjust work assignments on a daily basis for the entire maintenance team!.”
Kandice F., Plant Maintenance Admin, Champion Technologies Fresno, TX