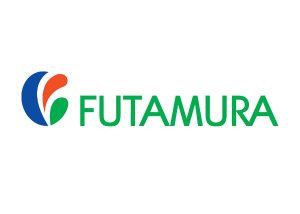
Futamura Achieves 99% Compliance Rates and Goes Mobile with eMaint
Industry: Packaging
Futamura is a leading producer of cellulose packaging film, manufacturing sustainable and customizable fibrous casings.
Futamura has facilities in Japan, the UK, and the United States. The U.S. plant achieved a 99% compliance rating by using eMaint tracking capabilities. It also uses eMaint to reduce downtime, monitor safety-critical assets, and improve work order management via the mobile app.
THE CHALLENGE
The Futamura facility in Kansas, United States, maintains more than 10,000 on-site assets, ranging from cutting-edge automated tools to older, highly specialized equipment. Maintaining such a large fleet of assets is a challenge, especially since many are safety-critical.
Due to Futamura’s manufacturing processes and end product, it is subject to strict national and international regulations and standards. Before implementing eMaint, monitoring compliance was a major challenge for the U.S. plant; It had a 50% compliance rate for on-time completion of PMs.
Today, the Futamura Kansas plant achieves a compliance rate of 99% with eMaint. Additionally, eMaint reduces plant downtime, cuts costs, and facilitates a data-driven maintenance strategy.
IMPLEMENTATION
Paul Whitham is the engineering and maintenance manager at the Futamura U.S. plant. He uses eMaint to plan and schedule mandatory maintenance tasks. Whitham also employs eMaint to monitor safety-critical assets, improve work order management, and standardize workflows.
Maintaining Regulatory Compliance
The U.S. plant relies on eMaint dashboards to monitor all safety-critical equipment. It also uses eMaint to track precisely when lab equipment needs to be calibrated.
Whitham explains, “We have lab equipment that needs to be calibrated to a set standard. We’ve set those assets up in eMaint… this system indicates calibration is needed 30 days and 60 days in advance. As the due date approaches, technicians receive a notification and complete the job. That all feeds into a dashboard that tells us our compliance rate.”
eMaint also provides Futamura with detailed instructions about the tools and procedures each compliance workflow requires. This simplifies the process, ensuring tasks are completed on time.
The Futamura team also uses eMaint to track incident reports and other key data, like upcoming employee training dates, or re-certification requirements. Whitham says he loves how easy it is to configure eMaint to meet his unique needs. With eMaint, he says, the possibilities are endless: “If you can dream it, you can probably do it.”
Work Order Management with the eMaint Mobile App
The eMaint mobile app lets maintenance crews access work orders from anywhere, regardless of internet connectivity status. Futamura uses the app as a repository for asset data, checklists, and instructions for maintenance crews. It’s a great way for new employees to access crucial information from anywhere, including in the field.
Whitham explains, “The mobile app makes structured asset data handheld. It’s instant access to a dozen filing cabinets at the touch of a button.”
The eMaint mobile app also lets maintenance crews remotely close work orders and add notes.
Data Analytics and KPIs
Whitham and the Futamura team collect and analyze plant data with eMaint, reducing costs and increasing uptime. eMaint mobilizes crucial data access, which facilitates data-driven asset maintenance.
Whitham says, “We used to spend hours analyzing the data to then spend five minutes doing something about it. Now we spend five minutes getting the data and we can spend a few hours actually doing the job that we need to do.”
By leveraging eMaint to collect data, the maintenance crew can work faster and resolve problems rapidly, reducing downtime and cost.
RESULTS
Futamura uses eMaint to deliver a 99% compliance rate, along with increased uptime and improved operational efficiency. The team is excited about expanding its use of eMaint, and they’re already looking for new ways to analyze plant data. Whitham says, “we have a wealth of data, but we underutilize it…We don’t use it to drive our decisions from a maintenance perspective. And once we do that, then I think we’ll start to see huge upticks in terms of uptime and reduction in cost to the business.”
“If you can dream it, you can probably do it with eMaint.”
– Paul Whitham, Engineering and Maintenance Manager at Futamura
“The mobile app makes structured asset data handheld. It’s instant access to a dozen filing cabinets at the touch of a button.”
– Paul Whitham, Engineering and Maintenance Manager at Futamura