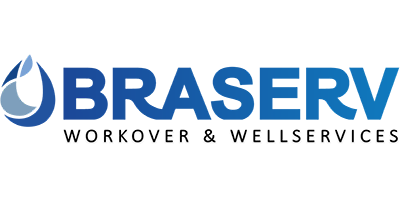
Braserv Petróleo Leverages eMaint to Maintain the Reliability of their Critical Assets
Customer Since: 2019 | Industry: Oil & Gas
Braserv Petróleo, established in Colombia in 2012, provides support services for the oil and gas sector. Until 2016, their operations were primarily focused on the Campo Guando oil field and carried out by just four rigs. From there, the company experienced a period of rapid growth, and by the end of 2018, they had deployed 15 rigs across several other high-production oil fields. To keep up with the growth of the business, Braserv needed a modern, scalable way to improve their asset maintenance strategies and ensure the continued high quality of their services. eMaint was the perfect solution.
BACKGROUND
Headquartered in Bogota, Braserv Petróleo operates in the most productive oil fields in Colombia, with the two largest fields combining to produce approximately 350,000 barrels of oil per day. With 620 employees deployed across 15 worksites, Braserv seeks to use cutting-edge technology to make their commitment to safety, efficiency, and the environment a reality. Petroleum engineer Juan Dangon joined Braserv in 2017, and he was later appointed to oversee the company’s newly created reliability and integrity sector.
CHALLENGES
One of Dangon’s primary tasks was to lead the implementation of a powerful, user-friendly CMMS that could strengthen the company’s maintenance program. The company had attempted using another maintenance management system in the past, but they were disappointed when it did not meet even a fraction of their needs.
Braserv’s most critical assets include their workover and well servicing unit, drawworks, hydraulic winch, traveling block,
mud pumps, BOPs, and choke manifold. If any of these assets were to fail unexpectedly, the costs would be extremely high in terms of lost production time and emergency maintenance expenses. Failure could also put the people who use the equipment at risk of injury. In total, about 20% of all Braserv assets are considered critical assets, so they needed a reliable solution to help them mitigate risk and avoid unplanned downtime.
IMPLEMENTATION
More than half the records now in Braserv’s deployment of eMaint relate to asset inspections for their maintenance, operations, and Health, Safety, Environment, and Quality (HSEQ) programs. eMaint enables weekly scans of all the company’s critical assets. This has made it possible for Braserv to keep a pulse on the health and reliability of their critical equipment and greatly improving key performance indicators (KPIs) like mean time between failures (MTBF). In addition, with eMaint, the Braserv has visibility into their critical assets from any location.
Within 12 months of implementing eMaint under Dangon’s supervision, Braserv began seeing lower maintenance costs, increased data traceability, and greater worker satisfaction. “That is what we are looking for with the platform: An information system that we can all access from anywhere in the country, access from the cloud, any user in the field,” said Dangon. “Any working person has access to the entire database, certifications, resumes, and manuals. As we feed and grow, this system will obviously be increasingly useful and more usable for each of the users we have.”
But Dangon also notes Braserv has not yet unlocked the full capability of eMaint. “When is my equipment less reliable and why is it failing so often? What are those failure modes? What are those failure reports?” says Dangon. “That is the next stage we want to reach with eMaint, which [will] allow us to reach a root-cause analysis of failures and allow us to optimize resources.”
RESULTS
Now that the Gee Whiz team is equipped with Fluke Mobile, teams can work efficiently at remote work sites, like a ranch the team visits weekly that is two hours away and doesn’t have reliable internet service.
Gogert recommends eMaint to maintenance teams working in specialized fields like Food & Beverage manufacturing.
“Change is hard for a lot of people. But eMaint isn’t hard to learn. It’s very easy, very customizable, so I think that a company in any field would be able to configure this to make it work for them, which was very important to us.”
BENEFITS
“I always saw from the beginning the potential of eMaint, in that it is a very flexible platform, programmable, and configurable to the needs of each organization. And I think it has allowed me to work on it, to develop it, to the vision we have at Braserv.”
– Juan Dangon, Maintenance Specialist, Braserv Petróleo