In recent years, consumers have gotten used to ordering something online and having it arrive on their doorstep two days later. Most consumers never thought about the supply chain or all the moving pieces involved. Product inventory management seemingly worked seamlessly. A predictable supply chain is vital to the operations of manufacturers and other businesses as well. Concepts such as lean manufacturing and just-in-time delivery depend on getting what you need when and where you need it. But, as has become clearer than ever, the global supply chain is a delicate network with many potential vulnerabilities.
The more complex something is, the more ways it can fail. From the COVID-19 pandemic to labor shortages to extreme weather events, widespread supply chain woes have recently challenged assumptions that businesses once banked on. More companies are looking forward, focusing on the resilience of their supply chains rather than optimizing them to be lean.
What is a Supply Chain?
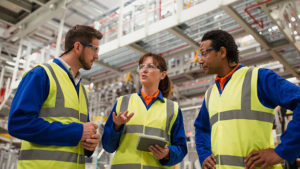
Credit: Getty Images
A supply chain is a network that creates products or services and delivers them to buyers or end-users. The supply chain includes organizations, individuals, processes, information, and technology. Even the simplest product has a number of steps and segments involved in its production.
An optimized supply chain helps a company stay competitive by reducing costs and making faster production cycles possible. The supply chain woes have disrupted these benefits and made them harder to achieve.
How Does the Supply Chain Impact Maintenance?
Supply chain disruptions as a result of the pandemic, natural disasters, and extreme weather have forced some factories to shut down. Other factories have had to take machines offline. In extreme circumstances, teams even share parts among different machines because they don’t have enough inventory to keep it operational.
Inventory Management and the Supply Chain
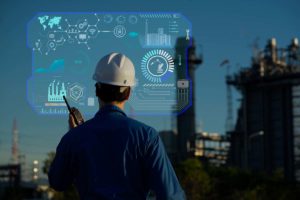
Credit: Getty Image
Having the best inventory management practices doesn’t necessarily mean foreseeing every possible eventuality — such as one of the world’s most heavily used shipping lanes becoming suddenly blocked and impassable for nearly a week. Envisioning worst-case scenarios and acting as though they will all become true would lead to businesses hoarding, creating artificial scarcity, and ultimately exacerbating shortages.
According to the Wall Street Journal, “Sourcing [semiconductor] chips has turned almost into a lottery, leading to over-ordering that creates more supply strain, industry experts say.” Stockpiling for the sake of stockpiling has its own ripple effects and having too much on hand is not a solution — it’s just a different kind of problem.
Meeting today’s supply chain challenges, and preparing for the future, means being adaptable. With prices and availability less predictable than they used to be, inventory management may become even more of a balancing act.
The Plight of the Pasta
For example, early in the pandemic, there was a bucatini shortage — less of it was being produced, according to New York Magazine’s Grub Street. Because of its shape, bucatini is more complex to produce than some other types of pasta. Between sky-high demand for pasta during early lockdowns and social distancing requirements impacting staffing, multiple manufacturers scaled back on bucatini production in favor of shapes that are simpler to produce, such as spaghetti.
Every business will need to decide its top priorities when choosing how to adjust and adapt to today’s challenges. For some, maybe that means making less bucatini.
The Role of Inventory Management Software
It may be harder than in the past to optimize an inventory, but there are some tools that can help. Organizations that know what they have on hand, in what quantity, and where it all is in real-time can make decisions and judgment calls that eliminate some of today’s guesswork. Accurate forecasting and projecting can help organizations decide where and how to spend to meet their needs.
Even prior to all these disruptions, optimizing an inventory meant taking numerous factors into account for every item:
- Lead time
- Consumption rate
- Shelf life
- Storage costs
- Potential costs and consequences of not having the part
- And more
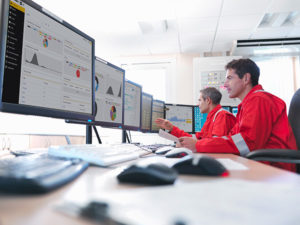
Credit: Getty Images
An inventory management software, such as a Computerized Maintenance Management Software (CMMS) system, centralizes information about spare parts, supplier information, and transaction history. Having all this information located in one place makes audits and reporting easier. It also makes identifying trends and bottlenecks simpler.
Several other eMaint features streamline remote inventory management. Materials requests can be made within work orders. And, when the amount on hand falls below a set reorder point, parts are automatically pushed to a reorder list. Both functions simplify planning. Adding images to parts records reduces the likelihood of errors and miscommunication. Reducing manual data entry also improves accuracy. A CMMS can integrate with other tools as well.
Collaboration and communication among several departments can help organizations navigate today’s supply chain challenges. Maintenance, procurement, and accounting teams, among others, all need to work together to plan and prioritize. Having actionable data is one of the foundational needs of any organization hoping to make the most of its inventory management.
How Some Companies are Coping
Supply chain issues can impact the materials available to produce goods and the parts available to repair and replace assets. Some products can be made but not sold because their manufacturers cannot get the necessary packaging.
Many raw materials have increased in price. Even if companies can produce their goods, as usual, the backups at ports and lack of truck drivers means that fulfilling orders can be harder or take longer.
It may be feasible for organizations with multiple sites to move materials, parts, and other goods among sites to maximize production, fulfillment, and maintenance.
To learn more, speak to one of our experts. We can show you how eMaint CMMS organizes inventories, simplifies work orders, streamlines ordering, and alleviates the stress of supply chain woes.