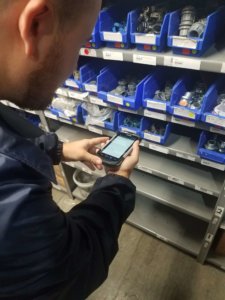
A logistics clerk uses a handheld device to issue parts management inventory.
A maintenance storeroom is the central hub for a maintenance team, ideally providing a clean, organized, safe, and secure environment to house materials. A smoothly operating maintenance storeroom is vital for more than spare parts management. It can be key to operational efficiency for many enterprises.
The goal of a maintenance storeroom is to ensure your maintenance teams always have access to the right tools and parts, in the right quantity, exactly when and where they need them. If maintenance technicians are wasting their valuable time acquiring or tracking down mislabeled or misplaced parts, it can significantly increase costs, as well as result in excessive asset downtime.
Another vital aspect of successfully managing a maintenance storeroom is ensuring all inventory records are accessible and visible to everyone who needs to view them, ranging from maintenance technicians to procurement professionals to financial analysts.
Organizations that prioritize maintenance storeroom visibility often utilize a computerized maintenance management system (CMMS) software that makes integrations easy and enables connected reliability — a framework that joins hardware, software, and systems through the enterprise.
Materials Management 101: Storeroom Visibility
The materials management process consists of three main stages: acquisition, control, and movement. And throughout every stage, a wide range of stakeholders need quick and easy access to any relevant storeroom records or data to effectively perform their jobs. In other words, they need visibility into their storeroom.
The acquisition stage may not seem like it involves a maintenance storeroom. However, planners require access to real-time information on storeroom inventory levels, as well as future maintenance work orders, to proactively forecast upcoming materials needs. Procurement professionals also need detailed part information, as well as approved vendor records, for every piece of storeroom inventory to quickly make purchases and ensure maintenance technicians have exactly what they need without delay.
The control stage begins when a part arrives at a storeroom, where it should be immediately cataloged and stored in the appropriate place. The use of scannable barcodes or QR codes paired with computerized inventory management software can greatly improve the efficiency and accuracy of storeroom record-keeping. And by standardizing storeroom layout and organization (e.g. Labels above or below each product?), workers will be able to more quickly obtain the correct parts, saving time for everyone involved.
The movement stage occurs when a storeroom part is needed in the field. After being requested by a technician, personnel then locate and transfer the necessary materials to their final destination, ensuring the required parts arrive when they should, where they should. In most organizations, maintenance storeroom personnel are responsible for tracking down and moving materials. But no matter who owns the movement stage, a smoothly operating logistics process is vital to the success of any maintenance operation.
Every stage of the materials management process depends on many individuals spread across many departments working in harmony. Maintenance technicians, procurement specialists, storeroom workers, logistics specialists, leadership teams, and finance personnel all require quick and easy access to complete and accurate data to effectively do their jobs.
And the best way to ensure such connected reliability across your entire organization is through a union of software and hardware into one cloud-based ecosystem.
Using CMMS for Maintenance Storeroom Success
A well-run maintenance storeroom is at the heart of any successful maintenance operation. Unreliable pen and paper documents used to be the lifeblood of every storeroom. But many modern storerooms today rely on CMMS software to achieve success.
By seamlessly integrating with handheld smart tools, IIoT sensors, parts management software, financial enterprise resource planning (ERP) systems, and other essential systems, CMMS software like that from eMaint simplifies the tracking, procurement, storage, and transportation of all storeroom parts.
Such computerized, cloud-based systems allow users to:
- set up customizable reorder points;
- auto-generate purchase orders;
- instantly enter or review data using barcode or QR code scanners;
- set up parts kitting orders (bundling multiple components) to streamline purchases or returns;
- and much more.
But perhaps most importantly, a CMMS approach to managing your maintenance storeroom ensures there is visibility across your entire enterprise. By linking storeroom inventory levels to maintenance work orders, supplier databases, financial management software, and other integrated systems, a cloud-based CMMS helps automate workflows while providing all stakeholders with valuable insights that would have been unimaginable just a few decades ago.
Don’t wait, get eMaint to improve your maintenance storeroom management process today.