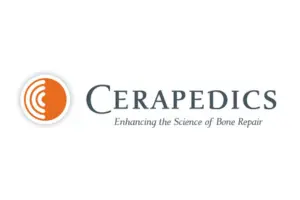
Cerapedics Simplifies Spare Parts Management with eMaint
Ortho-biologics company Cerapedics streamlined the management of more than 750 spare parts with eMaint CMMS
Customer Since: 2022 | Industry: Life Sciences
Cerapedics is a global bone-graft technology company who faced a maintenance inventory challenge: How could they develop a system for streamlined, strategic spare parts management?
Using eMaint, they’ve been able to organize, track, and simplify parts management for the team, getting critical spares into the hands of techs faster.
Now parts management is quick and efficient at Cerapedics, saving the team time on finding parts and making sure critical spares are available when maintenance emergencies happen.
BACKGROUND
Cerapedics is an ortho-biologics company revolutionizing bone repair with bone-graft technology that heals bones faster and at higher rates of success. Cerapedics products are utilized in more than 4 million annual orthopedics, trauma, spine, and interventional procedures around the world.
John Espinosa is the Maintenance Manager at Cerapedics. He arrived in summer 2022 and discovered an opportunity to optimize the parts management system—ensuring precious time and labor wasn’t spent finding the right part for the right equipment, and the team could quickly access critical spares.
CHALLENGES
Espinosa had a vision for a spare parts system where workers could find the parts they needed quickly, without spending their valuable time navigating Cerapedics’ inventory of more than 750 parts. He recognized the need for part tagging, location tracking, and a central organizing system for the storeroom.
“I wanted people to be able to say, ‘I need a three- horsepower motor,’ and be able to go into a system, and navigate to that part quickly, easily, and see exactly where it’s at—the shelf, the room,” Espinosa says. “That’s critically important to what we do.”
“We have plenty of other things to have to think about without having to navigate this labyrinth of spare parts. I wanted that to be simple.”
IMPLEMENTATION
Espinosa soon found that Cerapedics didn’t just have access to an industry-leading CMMS software—they also had a team of experts just a phone call away.
“eMaint’s biggest strength is support,” Espinosa says. “When I run into a problem, the chat feature is right there, and the individuals I’ve interacted with are experts on the platform. I’ve never been involved with a CMMS where that was available.”
He worked with eMaint to organize and track Cerapedics’ spare parts, establishing a streamlined and standardized system that would save his team time and labor. Finding critical spares during maintenance crises became a simple process of searching the eMaint spare parts database.
Espinosa has never experienced this level of customer care with a CMMS platform before. “No other CMMS that I’ve used has the wonderful customer support eMaint does.”
RESULTS
Now the Cerapedics storeroom is organized and tracked with eMaint.
Espinosa’s maintenance team can quickly search for a critical spare, determine its status and exact location, and even look at historical analysis on previous work orders. Spare parts can be attached to relevant assets and integrated into standard work orders and PMs.
Maintenance and business interactions have been simplified, too—eMaint now works in harmony with Cerapedics’ purchasing system. Spare parts have pricing, and Espinosa can quickly see what he’s running low on in the eMaint Parts Reorder list. Maintenance can easily create purchase orders and purchasing can fulfill their invoices.
Why does Espinosa recommend eMaint above the competition for maintenance programs facing the same challenges? “Flexibility,” he says. “Flexibility, and the level of support eMaint offers in the field.”
“I still have friends in maintenance departments at old jobs, and I take no small amount of glee in sending them eMaint snapshots and saying ‘Hey, look what I can do!’”
OUTLOOK
“I still have friends in maintenance departments at old jobs, and I take no small amount of glee in sending them eMaint snapshots and saying ‘Hey, look what I can do!’“
– John Espinosa, Maintenance Manager at Cerapedics