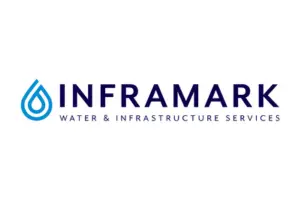
Water services company standardizes and connects its 75+ utility operations using eMaint CMMS
Customer Since: 2018 | Industry: Water and Wastewater Infrastructure Services
Inframark will soon complete the final phase of its ambitious multi-site eMaint CMMS software implementations for the company’s 75-plus water and wastewater operations. How did Inframark overcome the challenges of such a mammoth undertaking? Detailed preparation, organization, joint teamwork, the right CMMS, and a relentless commitment to reliability.
BACKGROUND
Inframark provides water and wastewater services to municipal and commercial clients in 16 states. The company has two corporate offices, one in Horsham, Pa., and the second in Katy, Texas, and employs more than 1,500 people.
The company needed CMMS software powerful enough to standardize maintenance operations. Furthermore, the system required a centralized, system-wide view of all asset management activities. The right platform would enable them to collect, store, and leverage the data to achieve its continuous improvement goals.
After comparing the strengths and weaknesses of several computer maintenance management systems, Inframark chose cloud-based eMaint CMMS software because of its all-encompassing capabilities.
THE CHALLENGE
When Shaun Niles, Director of Operations Solutions at Inframark, and Pamela Curry, Manager, Special Projects and Change Programs, took on the multi-site implementation project, the selection of eMaint CMMS software was in its final stages.
Previously, all of Inframark’s contract operations used a maintenance management system, but each one was independent, preventing the organization from having visibility across all business units. Because corporate support staff members could not access the individual systems, if an issue arose they would have to interrupt an onsite staff member’s day with a phone call or fly a technician to the site.
Inframark’s aggressive goals, coupled with the number of planned CMMS implementations, made preparation crucial to success. The logistics, coordination, and rollout of the seven separate phases needed to flow as designed to minimize disruption to local operations as much as possible.
IMPLEMENTATION
The Inframark team, headed by Niles and Curry, took a highly strategic approach. The organization started with one pilot project at its Danville, Va., location. Once the implementation team and the facility’s maintenance staff felt confident in the CMMS, Inframark built out a master system. Next, the rest of the facilities were grouped and divided into phases, and timelines were created.
“A lot of effort went into planning the process and identifying roles, responsibilities, and holding people accountable,” Niles says. “And that is key to how we were able to accomplish the amount of work that we got done in the timeframe that we did.”
Training Inframark personnel to use the CMMS effectively was also critical to a successful implementation. To its benefit, the company was able to count on the same eMaint product trainer throughout each phase. The growing familiarity between the company and the eMaint experts worked to enhance communications between the teams and streamline the executions.
“We’ve been very fortunate in that we’ve been able to have the same eMaint product trainer for all of our implementations,” says Curry. “That provides some really beneficial consistency in terms of how the message is presented.”
All maintenance professionals received an eMaint training guide customized by Curry to fit its standard configuration and system functionality. It should be noted that prior to eMaint, Curry had never seen or used a CMMS. As the administrator, she quickly learned how to make changes to the system and became an expert at wielding its powerful capabilities.
Assets were categorized using a criticality assessment, and the software was configured to recognize priority work orders based on an asset’s rank. The company can then provide this information to its clients to help them make annual capital expenditure decisions.
The Inframark implementation team also includes two field technicians, Hunter Fulton and Frank McKenzie, who perform eMaint CMMS demonstrations and ongoing support to enhance effective use of the system. Collaboration among organizers, office personnel, and the technicians helped considerably to drive home this goal and many others.
RESULTS
With a standardized platform in place, Inframark is tracking KPIs that will empower it to make quality data-driven maintenance decisions on more than 30,000 assets in the combined 46 eMaint systems. The company maximizes its custom-built backlog report, designed by eMaint and Inframark, to fit its unique needs. Maintenance professionals can quickly see how many work orders are in the backlog at the start of a month and track the total number of work orders created, completed, canceled, closed, or past due.
As Inframark continues to evolve, it is now developing a CMMS assessment tool for setting annual system-wide goals. This includes minimum requirements and best practices, to imbed its culture of continuous improvement further.
BENEFITS
“I’ve been extremely pleased with eMaint. The configurability has just been so dynamic. I can go to Pamela with the most unique, off the wall request for data possible, and within 24 hours, she’s produced what I’ve asked for.”
– Shaun Niles, Director of Operations Solutions
“If I can’t configure the needed data, then I can contact eMaint support, and they’ll do it for me.”
– Pamela Curry, Manager, Special Projects and Change Programs