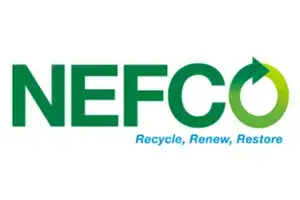
NEFCO Standardizes CMMS Data Across Six Treatment Plants with eMaint
Customer Since: 2015 | Industry: Energy
The New England Fertilizer Company (NEFCO) designs, builds and operates biosolids processing facilities. The company was looking for a CMMS to help ensure standardization, stability and consistency throughout all NEFCO plants. After engaging in various eMaint training options, the company implemented eMaint CMMS in six NEFCO plants. Since then, NEFCO experienced the ability to track key business metrics, maintain optimized inventory levels and more.
BACKGROUND
The New England Fertilizer Company (NEFCO) designs, builds and operates biosolids processing facilities, and is responsible for treatment of municipal wastewater byproducts, producing high quality Class A fertilizer. Bill Hollman is the Corporate Operations Manager at NEFCO.
THE CHALLENGE
Hollman and his team wanted a “state of the practice” CMMS to help analyze their current status, manage maintenance and support corporate-wide continuous improvement goals, including ensuring standardization, stability and consistency throughout all NEFCO plants. NEFCO also needed 24/7 access delivered on a user-friendly SaaS model with the ability to expand and mature with the organization.
IMPLEMENTATION
In the early stages of his eMaint partnership, Hollman and other NEFCO staff members attended a eMaint Boot Camp training session to learn best practices and gain practical knowledge about eMaint. In the new Detroit, MI project the NEFCO-eMaint team performed an eMaint KickStart, which includes reviewing CMMS goals, developing a high-level implementation road map timeline, and establishing a project plan. To begin implementation, Hollman extracted all information from the old maintenance management system at the NEFCO Quincy plant as a baseline. Hollman and the Detroit Plant Manager and staff established Preventive Maintenance schedules, and input contacts and inventory locations. The team created a database of standardized information, and built personalized forms to use across all locations, which made bringing other plants onboard with eMaint was a streamlined process.
RESULTS
To date, about 100 NEFCO employees utilize eMaint. Office Managers use eMaint’s purchasing feature for office supplies, mechanics login to access work, and upper management uses reports and dashboards to analyze key business metrics. All parties appreciate the system’s ease-of-use and consistent access. Hollman also reports that the number of hard copy records has been reduced rapidly since switching to eMaint – helping the company to “go green.”
NEFCO leverages the capability of eMaint to track a variety of key business metrics, including: work order types, Mean Time Between Failures (MTBF), Mean Time Between Repairs (MTBR), and open work orders monthly. The company also tracks critical spare parts, and plant managers automatically receive alerts when a part reaches a reorder point. This way, each plant avoids downtime associated with not having the right parts in inventory.
NEFCO uses eMaint’s document storage feature to clearly illustrate how they maintain equipment to comply with even the strictest of standards. Hollman and Plant Managers also leverage the document storage capability to offer easy access to Standard Operating Procedures (SOPs), technical manuals and safety how-to’s. In the innovative Detroit plant, mechanics have tablets, so they can review these SOPs, as well as open and close out WOs via electronic signatures in the field. After successful implementation of these practices in the latest plant, the plan is to spiral this development into legacy plants.
BENEFITS
“eMaint is our state-of-the-practice CMMS. It allows us to track key business metrics, helps us comply with environmental standards, and ensure work is completed on-schedule. About 100 employees interact with eMaint, and everyone in NEFCO appreciates eMaint’s ease of use and 24/7 access.”
Bill Hollman, Corporate Operations Manager, NEFCO