
Based on 268+ reviews



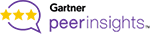
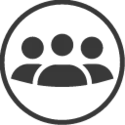
150,000+
USERS
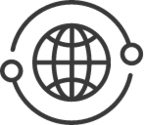
116
COUNTRIES
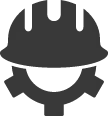
7,400+
MAINTENANCE TEAMS HELPED
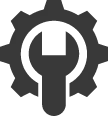
3.4 Million
MACHINES FIXED
eMaint CMMS gives you the power of a CMMS and EAM in the palm of your hand.
Manage work orders, view asset details, work offline, and much more.
Missing information and siloed teams lead to maintenance nightmares — and that’s where a mobile-first CMMS comes in.
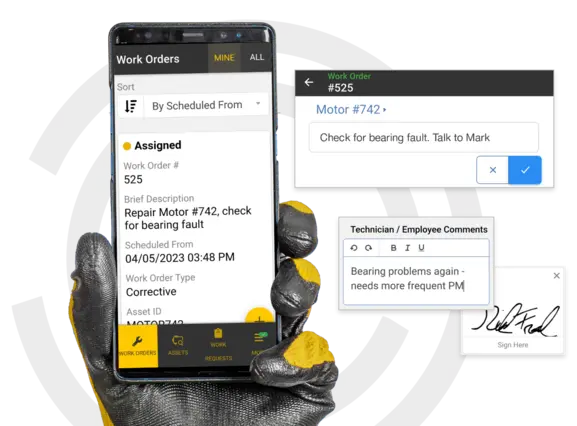
Mobile Work Orders Make
Life Easy
Manage work orders and work requests. Explore, create, assign, and complete on the go, adding pictures and checking off inspection lists.
Track your work in a few taps, preventing your team from going dark in the field.

Simplify your work, save time, and connect your teams
Manage, edit, and assign work orders in the field. Build work orders from your desktop and send them out to your team on the factory floor. Receive push notifications for important updates.

Snap a photo, add a checklist, and upload documents
Quickly and easily add photos and videos to your work orders. Design PM checklists and routine inspections, with personnel checking off tasks as they go. View and upload key documents.

Do it all, from work requests to booking spare parts
Scan asset QR codes to submit a work request to inspect failed equipment. Book spare parts for jobs, streamlined by eMaint’s ERP integration. Track work hours and require digital signatures for work order completion.
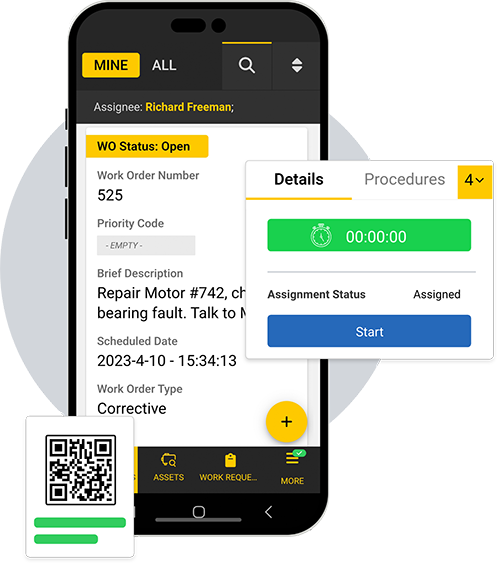
Asset & Part Details at Your Fingertips
Simplified asset and spare parts management. Browse your asset inventory, see maintenance history with barcode scanning, or submit work requests with QR codes.
Find a failed asset or a critical spare with a quick search.

Take the helm of an asset command center
Explore your asset details and recent maintenance history. Attach assets to work orders. See other open work orders for nearby assets when you’re already in the field. Gather data in the field with select Fluke tools integration.

Searchable, flexible spare parts inventory
Find the spare parts you need quickly. See recommended parts for specific assets and rely on the eMaint parts reorder list to optimize inventory levels. Take a look at what’s on hand, both in the storeroom and across your global organization, and request critical spares from throughout your work sites.

Found a failed motor? Scan QR codes for work requests, barcodes for asset details
Walking around the facility, eMaint users can scan barcodes to view asset or spare part details and history. And all personnel, regardless of whether they are an eMaint user, can scan a QR code on problematic assets to submit a work request.
Manage Work in the Field, Offline, and Across the Enterprise
Global businesses love eMaint. Work offline and your updates will sync once a connection is re-established. Manage international teams and tap into a global parts storeroom. Enterprises can enjoy the simplicity of single-sign on (SSO) and trust in strong security controls.
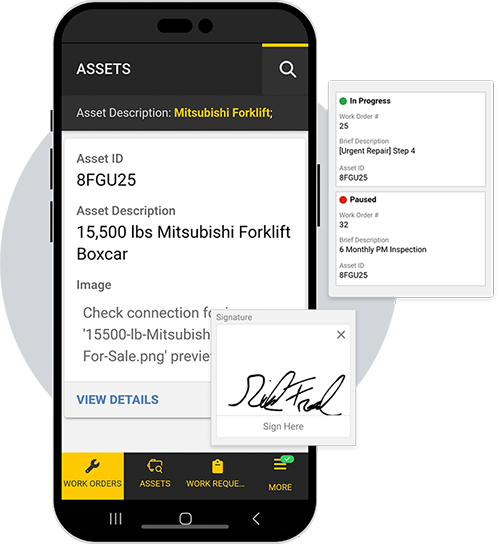
Maximize efficiency in remote work sites and network-unfriendly areas

Configurable, flexible, offline work orders
eMaint is built to support maintenance personnel who need to work offline, track their progress, and not worry about syncing results later. Complete work orders, edit asset information, and upload photos, with eMaint taking care of synchronization when a connection is re-established. Audit trail tracks actual time of actions, providing clear records and accountability.

Simplify compliance with permissions, e-signatures, and automatic audit trail
Manage permissions, control field-level security, and standardize compliant practices. Require password-protected e-signatures for key actions. Route work orders through levels of approval and across departments. eMaint’s audit trail captures user actions in a detailed, time-stamped lineage perfect for accountability and audit reporting.

Global maintenance standardization and enterprise asset & part management
Discover powerful insights with enterprise reporting and standardize a winning maintenance strategy across all your work sites. Work across languages, currencies, and time-zones. Manage your global mobile workforce with ease.