Today’s plants and facilities often have critical machines that bear the brunt of production activity while other equipment sits idle or is hardly used. Yet, the lightly used machinery is still scheduled for routine/calendar-based maintenance no matter how much or how little it operates.
A research study found that up to 30% of maintenance activities are wasted because they’re scheduled too frequently. But there’s also a flip side, which is when equipment doesn’t receive enough maintenance.
Over-maintained assets – Preventive maintenance intervals are too frequent or not effective. The consequence is wasted labor and parts resulting in unnecessary expenses.
Under-maintained assets – Preventive maintenance interval frequencies are too low and don’t enable failure detection or prevent equipment breakdowns. The result is unplanned production shutdowns and decreased output. Safety also becomes a risk factor.
What is usage-based maintenance?
Usage-based preventive maintenance, sometimes called planned maintenance, avoids over-maintenance of lesser-used assets. When applied to specific equipment, the maintenance strategy will decrease costs and increase maintenance of hard-working machinery, better-ensuring reliability. The difference lies in the scheduling of PM activities.
The approach enables maintenance professionals to adjust and optimize PM scheduling to fit actual equipment usage instead of basing maintenance on broad OEM calendar-based recommendations.
Benefits of usage-based maintenance:
- Weeds out unnecessary preventive maintenance activity, reducing overall operational expenses
- Increases preventive maintenance of hard-working critical assets, ensuring peak performance and health
- Enables better maintenance planning, e.g., repair time, and integration into the scheduling process
- Significantly reduces unnecessary spare parts expenditures and labor costs
- Optimizes maintenance resources, freeing up team members to work on other important projects
- Automated notification reminders enable maintenance managers to plan for upcoming preventive maintenance and technicians to prepare for servicing equipment
A typical way to explain the strategy is to consider the recommended oil changes for your car. If you follow them, the auto manufacturer might suggest changing it every three months or every 5,000 miles, whichever comes first. However, you wouldn’t change your oil based on a calendar date if you didn’t use your car because you were sent overseas for three months on a job.
Calendar-based/time-based maintenance – Triggers PMs based on calendar dates and times: weeks, months, quarters. No matter what, equipment is slated for maintenance based on the absolute time elapsed since the last activity, even if the equipment isn’t used. For example, a commercial fleet may change the oil in each vehicle on the first of every month, regardless of how many miles each vehicle has driven.
Usage-based/meter-based maintenance – Triggers PMs based on the actual equipment usage. Equipment is slated for maintenance after reaching a certain specific value unit, such as the number of miles driven or number of parts produced. A PM is automatically generated when a piece of equipment reaches a defined usage milestone. So instead of changing the oil for a whole fleet on the first of the month, a commercial fleet would track the miles driven and change the oil in each truck when it has driven 3,000 miles.
What industries routinely adopt usage-based PM strategies?
Many industries can benefit from usage-based maintenance, even though it’s often specific to certain equipment and particular needs. Here are four of the top sectors that leverage usage-based maintenance regularly.
Industry case studies and examples:
1. Fleet Management – A leading construction company sought to improve its planning procedure and perform maintenance on more than 1,000 pieces of heavy equipment, including a fleet of over-the-road and off-road trucks. The organization and eMaint CMMS experts developed a system for importing usage data based on hours run, fuel usage, and mileage for specific equipment. PMs are triggered automatically based on predefined criteria alerting maintenance members that it’s time for service. (more)
Oil & Gas – A leading oil and natural gas producer in the United States and a subsidiary of one of the world’s largest oil and gas companies, apply meter-based PMs to track its compressors. eMaint automatically generates a work order when the machine hits 2000 hours. The CMMS also tracks critical spare parts needed for compressor repairs to ensure availability. (more)
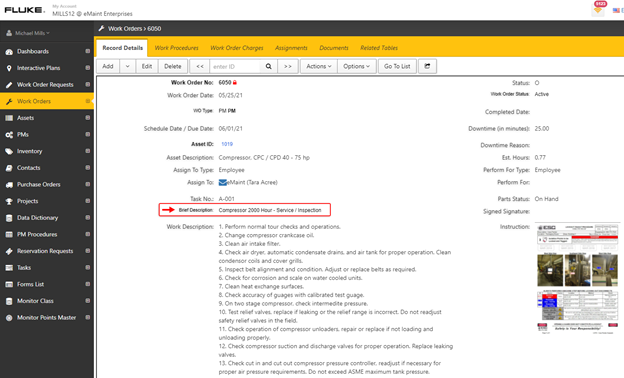
A work order is generated automatically at 2,000 hours.
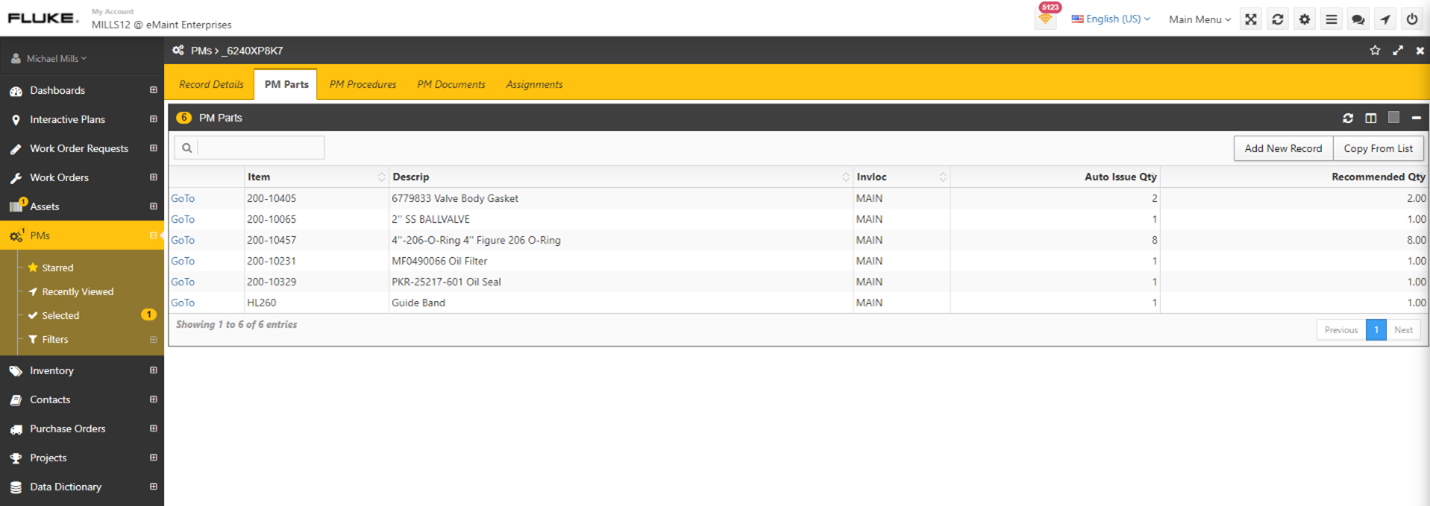
Work orders also show the parts needed to complete the task.
2. Facilities – An independent tools, products, and services provider helps its grocery store customers save money by applying meter-based PMs to critical store equipment, avoiding misspent labor and parts. (more)
3. Manufacturing – A tubing manufacturer imports meter reading measurements (temperature, pressure, fluid levels, suction) from critical equipment. The CMMS automatically triggers priority work orders and inspections when values fall outside predefined parameters.
How do you import meter-based or usage-based data into the eMaint CMMS?
If you decide to apply usage-based/meter-based strategies to your preventive maintenance program, you’ll need to consider how you’ll feed the data to the CMMS. The eMaint API facilitates back and forth communication between individual software systems. Integration must be designed and implemented to fit your company’s unique requirements.
- Connect2Assets: The Fluke Reliability Connect2Asset software can automatically pull meter readings from PLC machines, building automation systems, building management systems, SCADA systems, GPS systems, and more. Then, it moves the data to eMaint. When predetermined thresholds levels are met, the CMMS automatically creates a work order.
- API Integration (Application Programming Interface): The eMaint Computerized Maintenance Management System API facilitates back and forth communication between individual software systems, which can be customized to fit an organization’s unique requirements.
- eMaint MX Mobile software: The eMaint mobile software solution lets field technicians upload meter readings into the CMMS via their smartphone or tablet, whether they’re on-site or working remotely.
- Import from a spreadsheet: Data stored on a spreadsheet, such as meter readings, can be easily imported into eMaint and used to generate usage-based or meter-based preventive maintenance work orders automatically.