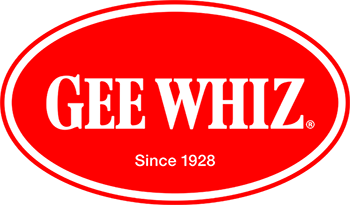
Gee Whiz Mobilizes Maintenance with eMaint’s CMMS App
Customer Since: 2022 | Industry: Food & Beverage
Gee Whiz is a producer of Washington apples and cherries that manages more than 1,000 assets across its orchards and facilities, from trucks to tractors.
A new maintenance administrator arrived to find paper work orders, insufficient asset management, and a true need for a mobile CMMS.
Researching their options, Gee Whiz found that eMaint CMMS had it all: digital work order management, asset tracking, and especially a CMMS app, Fluke Mobile, that teams could use when working in the field and offline.
BACKGROUND
Gee Whiz is a premium producer of Washington apples and cherries.
The Gee Whiz maintenance team manages over 1,000 pieces of equipment for their orchards and nearly 100 homes for on-site workers.
Working on the go is part of daily life for the Gee Whiz team. They travel long hours to visit ranches with unreliable internet connection.
Sandi Gogert, Fleet and Housing Administrator at Gee Whiz, set out on a mission to find work order software that served her mobile team and could save the company time and money.
And that’s when she found eMaint CMMS.
CHALLENGES
Gee Whiz needed a mobile CMMS—and eMaint was the clear leader.
“Your system is by far the best that I could find. I’m so pleased with how eMaint works, especially having access to the mobile app for smartphones and tablets,” Gogert said.
Fluke Mobile, the eMaint app, empowers users to complete and track work orders in the field. They can also work offline. The app automatically syncs changes into the CMMS when a connection is reestablished.
“Offline work is another thing that pushed us your way,” Gogert said. “Other companies didn’t offer that, and we’re sometimes out in the middle of nowhere.”
When Gogert arrived at Gee Whiz, work orders were all done on pen and paper. Gee Whiz sees an average of 40 new work orders a week, so tracking those work orders was a challenge—especially in the field.
“I wanted to make it easy for our mechanics. I didn’t want them having to spend a lot of time away from the repairs, doing paperwork,” Gogert said.
A mobile CMMS gives insight into problematic assets, like a concrete mixer that constantly breaks, but goes unnoticed without proper tracking.
“If you don’t have a strong work order system, you have less visibility over what you’ve been fixing. You could be fixing the same thing over and over again and not realize it, and waste money.”
IMPLEMENTATION
Realizing eMaint was powerful, easy-to-use, and had everything Gee Whiz needed, Gogert worked with eMaint on implementation.
eMaint helped Gogert to configure a simple work order form ideal for field work, build a database for Gee Whiz’s hundreds of assets, and train her workforce on the Fluke Mobile app.
“They were able to set it up to fit us, which was huge for me,” Gogert said.
Gogert’s journey with eMaint is just beginning—the eMaint team continues to support her and her team.
“The people in the eMaint support team, they’ve all been great,” she said. “eMaint gets right back to you. They don’t just jump in and fix it—they show you how they fixed it, too. They’re hands on and want to help you.”
RESULTS
Now that the Gee Whiz team is equipped with Fluke Mobile, teams can work efficiently at remote work sites, like a ranch the team visits weekly that is two hours away and doesn’t have reliable internet service.
Gogert recommends eMaint to maintenance teams working in specialized fields like Food & Beverage manufacturing.
“Change is hard for a lot of people. But eMaint isn’t hard to learn. It’s very easy, very customizable, so I think that a company in any field would be able to configure this to make it work for them, which was very important to us.”
BENEFITS
“Your system is by far the best that I could find. I’m so pleased with how eMaint works, especially having access to the mobile app for smartphones and tablets.”
– Sandi Gogert, Fleet and Housing Administrator at Gee Whiz