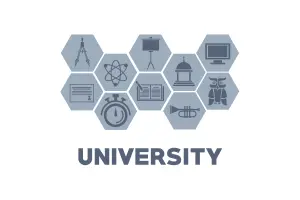
University boosts existing maintenance software with eMaint CMMS
Customer Since: 2018 | Education
Thousands of students pour into and out of universities every year. While graduating classes are leaving overworked microwaves behind, others are entering dorm rooms expecting properly working assets. At one university, equipment maintenance paper trails were commonplace, and asset tracking was difficult.
The existing maintenance request software, Star Rez, could not supply the details necessary to manage work requests made by students effectively. The customizable eMaint Computerized Maintenance Management System (CMMS) provided the integration capabilities required and expanded asset management features the housing office needed.
BACKGROUND
The university’s multi-use dining halls contained commercial appliances, and its thousands of dorm rooms were outfitted with kitchenettes or mini-refrigerators and microwaves. Properly operating plumbing was critical, as were heat pumps to handle the cold Pennsylvania winters. Although the university had an automated student work order creation system, the tickets lacked the information to resolve maintenance issues effectively.
The goal was to implement computerized maintenance management system (CMMS) software to streamline work order and asset management and ultimately add a predictive maintenance program. The university’s assistant director of Facilities Management was asked to help research and recommend an asset and maintenance management system for the housing office. The learning institution chose eMaint CMMS software because of its ability to overhaul maintenance processes, and because it could integrate with the Star Rez software used to support student requests for maintenance.
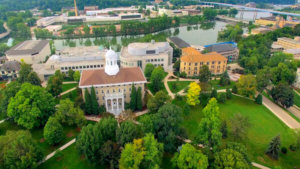
THE CHALLENGE
A combination of paper tickets and spreadsheets were commonly used by the university’s employees to manage maintenance requests. Other maintenance issues were sometimes reported by custodians. Personnel had to shuffle through a three-ring binder to view asset maintenance histories.
More than 5,800 rooms needed to be entered as assets to create a work order base. Room data had to be downloaded from the Star Rez database and imported into the eMaint CMMS. Once all the rooms were entered, the thousands of other assets—such as heat pumps, water heaters, and other appliances—had to be assigned to the rooms and entered.
The university went live with the CMMS starting with one complex. With the successful launch underway, the other complexes followed, and by the end of the month, all of them were operational.
RESULTS
The university’s assistant director built the asset database, while the eMaint CMMS software implementation specialists developed an integration piece to automatically merge work requests from Star Rez into the eMaint CMMS.
By integrating the Star Rez data with the eMaint CMMS, the university maintenance teams now see comprehensive descriptions of maintenance issues and understand the work that needs to be done. The CMMS enables housing facility managers to assign work orders to technicians instantly using a mobile device or a PC with just a few clicks.
BENEFITS
“The CMMS system will help us create budgets, decide where maintenance should be done, and forecast equipment replacement. It is so customizable; We can easily tailor it to fit our needs.”
– Facilities Management