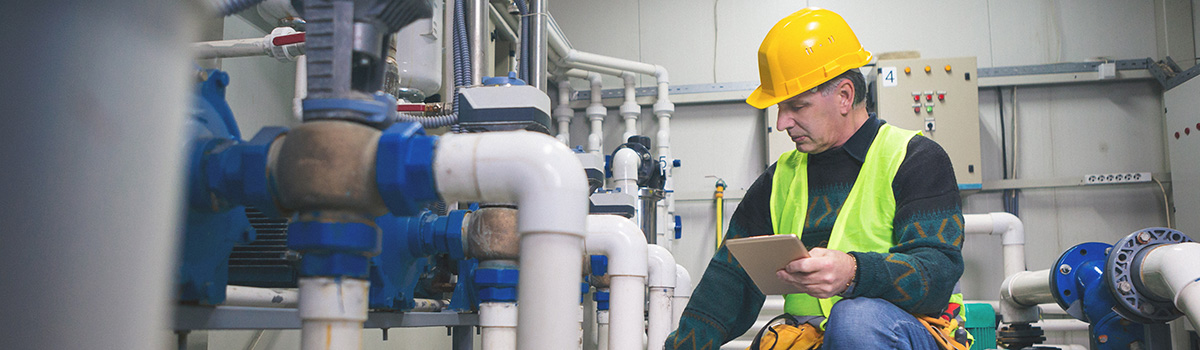
Deferred maintenance refers to postponing maintenance tasks — whether planned or unplanned — usually due to lack of budget. Over time, deferred maintenance tasks accumulate, creating a maintenance backlog.
Keeping a maintenance backlog has long been accepted as normal; however, regularly deferring maintenance comes with risks. As the maintenance backlog continues to grow, it becomes more difficult to get caught up and prioritize tasks effectively. With deferred maintenance, important tasks can fall through the cracks, and small problems can escalate to equipment failure if they are not addressed in a timely manner.
Some companies have even chosen a run-to-failure maintenance strategy that allows machines to continue operating until they fail. However, this practice accelerates equipment wear, reduces asset lifespan, and increases the risk of unexpected failure and downtime. Often, deferred maintenance costs more time and money than simply keeping up with maintenance would have cost in the first place.
Fortunately, Computerized Maintenance Management System (CMMS) software makes it possible to keep your maintenance both up-to-date and on budget.
Now that we’ve outlined the broad strokes, let’s take a closer look at the specific factors that contribute to deferred maintenance and how modern management tools offer viable solutions.
When Can Maintenance Be Deferred?
There are few compelling reasons to routinely defer maintenance for long periods—an approach that generally leads to increased time and resource expenditure. However, specific circumstances may justify a temporary deferment, such as aligning maintenance schedules with operational priorities or budget cycles.
These scenarios often fall into two main categories:
- Strategic Deferred Maintenance Strategic deferred maintenance involves deliberately postponing less critical maintenance tasks to allocate resources to more urgent ones. For non-critical components, it may make sense to allow a machine to operate until failure. This strategy is used when the downtime caused by a failure does not significantly disrupt operations or when the cost of preventive maintenance outweighs the cost of replacing the unit. It requires robust preparation, including having the necessary parts and personnel ready to manage failures effectively and minimize downtime.
- Involuntary Deferred MaintenanceIn contrast, involuntary deferred maintenance occurs due to uncontrollable factors such as sudden budget cuts or unexpected resource constraints. This type of maintenance deferment is unplanned and can lead to a cascade of issues—minor problems escalate, leading to major disruptions and increased repair costs.
What pushes an organization towards one of these types of deferred maintenance? Here are the contributing factors.
Reasons for Deferred Maintenance
- Budget Constraints
There are many reasons organizations choose to defer maintenance, but the leading reason is cost. When financial resources are tight, maintenance managers often need to make difficult choices about which tasks to prioritize.High-priority tasks with significant maintenance criticality might take precedence, while less urgent repairs and replacements are postponed. Although deferring maintenance might seem like a short-term solution, it’s important to consider the long-term consequences to your budget. Emergency repairs, which are far more expensive than routine maintenance, often result from deferred tasks. Moreover, unplanned downtime can leave workers idle and halt production, leading to substantial productivity losses.
- Inefficient Decision-Making Even when additional funding can be requested, slow approval processes can delay maintenance activities. If it takes weeks for management to approve necessary funding, pending tasks can easily accumulate in the maintenance backlog. Efficient decision-making and swift approvals are crucial to prevent maintenance deferrals.
- Company policies Even for companies that don’t intentionally operate a run-to-failure strategy, hold orders can be placed on work for any number of reasons, hindering the team’s ability to proceed with a maintenance task.
- Lack of planning
Poor planning frequently results in a lack of resources, whether parts or technicians, to complete maintenance tasks on time, leading to them being deferred.For example, without proper spare parts inventory management, teams may not have replacement parts on hand, which can lead to tasks being put on the back burner as they can not be completed until the parts can be ordered and delivered.
Similarly, insufficient staffing can leave teams without the required personnel to complete maintenance tasks on time. Additionally, certain analysis or repairs may be too complex for the existing team, necessitating the use of third-party contractors, who may not always be available and can be expensive.
- Unforeseen Emergencies Unexpected events can divert attention and resources away from routine maintenance tasks. Emergencies might require reallocating funds from planned maintenance to address the immediate issue. For example, if critical medical equipment malfunctions, ensuring safety for technicians would take precedence over non-urgent maintenance tasks like servicing a functional HVAC system.
- A Corrective Maintenance Mindset Relying solely on corrective maintenance, which addresses issues as they arise, can also contribute to deferred maintenance. Without a proactive maintenance plan, identifying the root cause of breakdowns becomes challenging. Additionally, budgeting for corrective maintenance is difficult, as the costs are unpredictable and can escalate quickly without proper data and documentation.
- A Lack Of Performance Data Repairs can easily slip through the cracks and be neglected without a metrics-driven approach and an effort to track maintenance KPIs.
Now that we know what might cause maintenance to be pushed back, let’s shift gears and look at how to spot when it’s actually happening.
Recognizing the Signs of Deferred Maintenance
Common signs to watch for include unusual noises or odors from machines, which might indicate the need for routine upkeep. Visible wear and tear, such as peeled paint, cracked walls, and rusted surfaces, also suggest a growing maintenance backlog.
Noticing these signs is one thing; ignoring them can lead to serious repercussions.
What Are The Risks of Deferred Maintenance
Across industries, key risks of delaying maintenance include:
- Cost of Repairs:Delaying maintenance can lead to more expensive emergency repairs. Additionally, the cost of spare parts will likely increase over time due to inflation.
- Reduced Overall Equipment Effectiveness (OEE): Postponing necessary repairs can decrease equipment effectiveness. Deferred maintenance can result in lower machine availability, disrupted production schedules, and compromised product quality.
- Safety Risks: Improperly maintained equipment can pose significant safety hazards, increasing the likelihood of accidents and potential OSHA violations and expensive fines.
Example of Deferred Maintenance: Denver International Airport
At Denver International Airport (DIA), a vivid example of the challenges and consequences of deferred maintenance unfolds. Despite billions spent on expansions, the airport has struggled with maintaining its existing infrastructure. A city audit revealed that the airport has fallen behind on maintaining its buildings and equipment, with more than 7,000 maintenance tasks backlogged over three years.
This maintenance neglect has led to out-of-order escalators and moving walkways, impacting the flow of passengers and the overall functionality of the airport. The maintenance team, understaffed by 23%, has been diverted often to emergency repairs, which leaves routine inspections and preventive work unaddressed.
The situation at DIA illustrates the snowball effect of deferred maintenance: minor issues escalate into major disruptions, costing more in the long run due to emergency repairs and decreased equipment life expectancy. The airport’s focus on large projects while neglecting basic upkeep serves as a cautionary tale of the importance of balancing expansion with the essential task of maintenance.
5 Steps to Decrease Deferred Maintenance
Looking at the repercussions at DIA, it becomes clear that effective management strategies are crucial to prevent similar outcomes. Here are key steps to consider implementing at your facility – – while some may be obvious suggestions, others might be less apparent but equally crucial.
-
Step 1: Log Maintenance Activity
Centralizing data around assets, equipment, work requests, and work orders is critical for reducing a deferred maintenance backlog. Investing in a CMMS or EAM system captures crucial information like wrench time, time to complete, maintenance costs, and warranties, which are helpful for audits and ROI cases.
-
Step 2: Conduct an Audit
Gathering data allows you to audit the scale of maintenance-related issues. Key questions to consider include whether there are warranties about to expire, the frequency and unpredictability of equipment failures, and the safety threats or impacts on staff and production.
-
Step 3: Prioritize the Backlog
Categorize the backlog into immediate and delayed attention tasks. Use criteria like cost, time to repair, asset lifecycle, and repair dependencies to prioritize effectively.
-
Step 4: Start or Increase Preventive Maintenance (PMs)
Preventive maintenance tasks are crucial for avoiding emergency and deferred maintenance. CMMS systems facilitate easy PM scheduling, customized checklists, and runtime-based PMs.
-
Step 5: Secure Additional Budget
Show where your current budget is allocated to secure additional funds. Demonstrate how investing in maintenance saves money in the long run by avoiding costly repairs and downtime.
How to Combat Deferred Maintenance with CMMS and IIoT
Computerized Maintenance Management System (CMMS) software helps maintenance teams keep on top of work orders and scheduling, as well as monitoring maintenance KPIs to be sure work is being completed on time.
IIoT devices, like condition monitoring sensors, can be installed on your machines to automatically collect key data, like changes in vibration and temperature that indicate the health of your equipment. Data analytics software can then analyze sensor data to make accurate predictions about your equipment’s maintenance requirements.
These technologies become your eyes and ears, giving you visibility into equipment performance and maintenance requirements based on data from the machines themselves. This allows you to prioritize maintenance more effectively and reduce the risks of deferred maintenance.
Speak with a specialist today to learn how our software and sensors can transform your business.