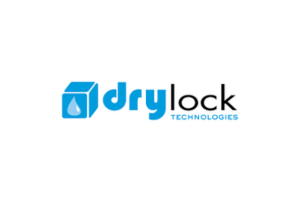
Drylock Technologies Ltd. Moves Toward World-Class Manufacturing with Support from eMaint CMMS
Customer Since: 2013 | Industry: Manufacturing
Drylock Technologies Ltd, designs, manufactures, and sells disposable adult incontinence products. One of the most critical challenges for Drylock was creating a change from firefighting to a more proactive maintenance culture. The company began implementation by scheduling work and labeling assets with numbers and descriptions to help make entering work simple and streamlined. With eMaint, the Drylock team is able to process nearly 1,200 work orders monthly and manage that work effectively.
BACKGROUND
Drylock Technologies Ltd, designs, manufactures, and sells disposable adult incontinence products. Jason Anderson is the API Maintenance Manager, and his team includes 12 technicians across four shifts, a Planner/Scheduler, Parts Room Coordinator, Preventive Maintenance Coordinator, and Mechanical/Electrical Group Leaders.
THE CHALLENGE
One of the most critical challenges for Drylock was creating a change from firefighting to a more proactive maintenance culture. To support this shift, Drylock wanted a CMMS system to link pictures, procedures, and documents to work orders. They also needed the ability to export data from the system when necessary. When Jason found eMaint, he leveraged the system’s robust feature set to receive buy in from management.
IMPLEMENTATION
Jason began implementation by scheduling work within eMaint, and labeling assets with numbers and descriptions to help make entering work simple and streamlined. The team also made sure that the core fundamentals of the system, such as asset structure and nomenclature of spare parts, were standardized. Jason used a two-pronged approach to change company culture: he leveraged eMaint to encourage the philosophical change to proactive maintenance, and revamped Drylocks’ planned downtime procedures.
To help accelerate the shift in philosophy, Jason’s team slowly integrated new, eMaint-centric procedures into employees’ daily lives, such as emailing work orders to technicians and production from the system. Today, technicians and operators rely on eMaint to do their jobs effectively. Technicians and operators use scheduling tools and eMaint dashboards such as “Operator Work.” This live widget filters all open work for operators for each specific line to see open work orders, and when the jobs need to be completed. Operators can click on the work order to open it with work instructions attached. Training videos are also embedded on eMaint dashboards.
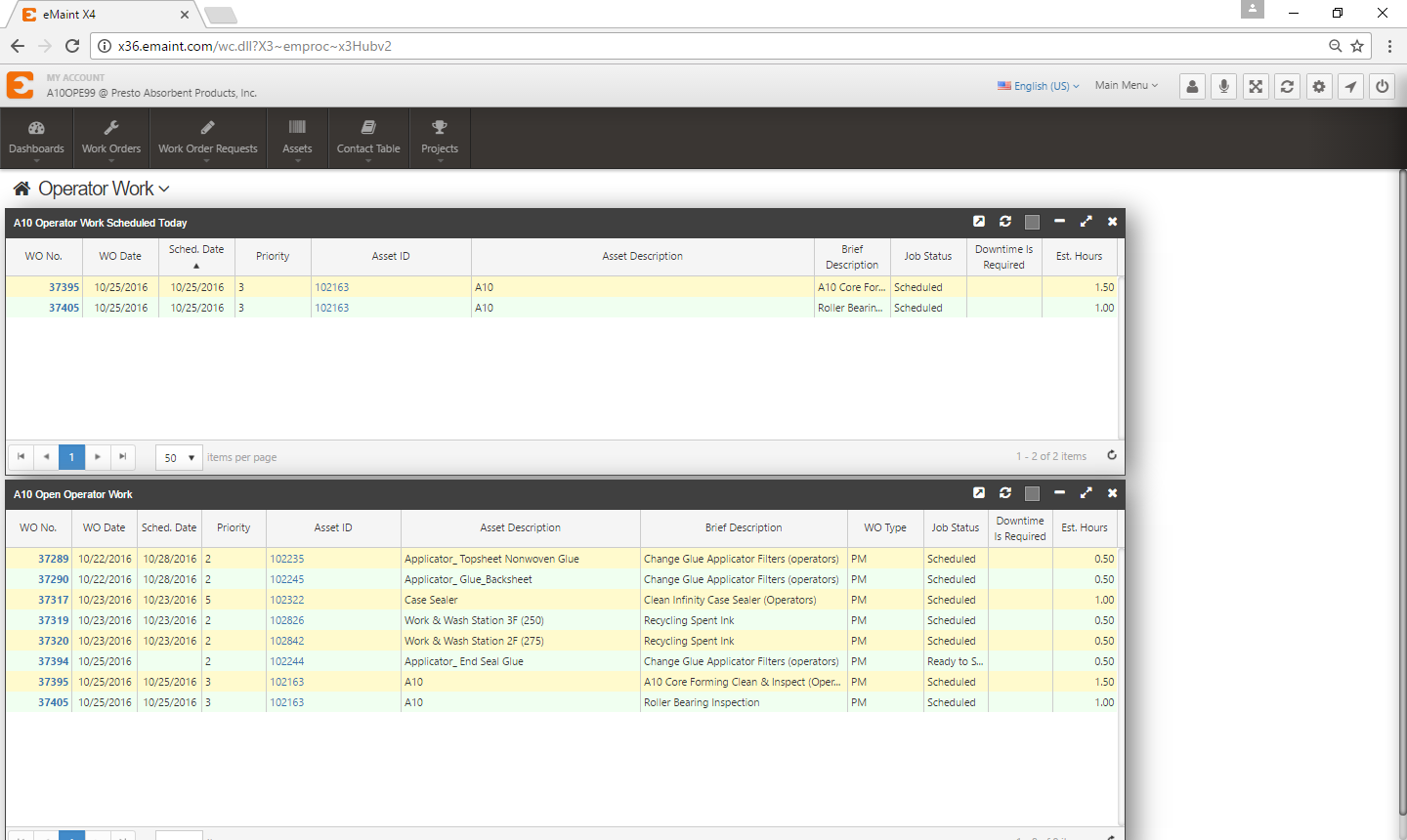
Jason also developed a dashboard for the entire team to see when PMs and production are planned, and to make scheduling for group work easier.
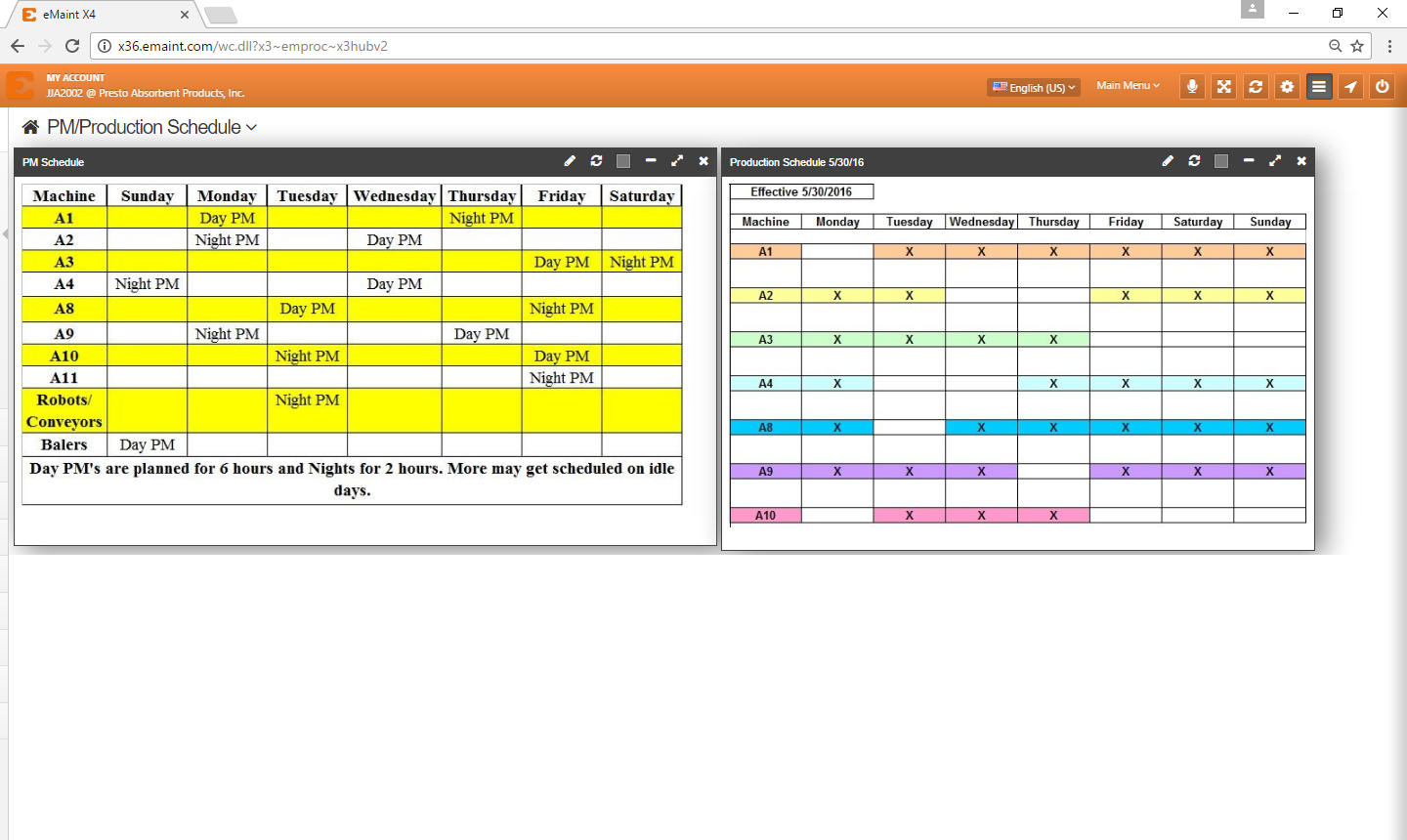
Prior to eMaint, Drylock scheduled maintenance once a week, with long periods of equipment shut down. With eMaint, Drylock schedules equipment shut downs more frequently in smaller time increments, and ultimately increases equipment and employee productivity. Jason created a dashboard to track the trends of productivity in the short and long term for maintenance.
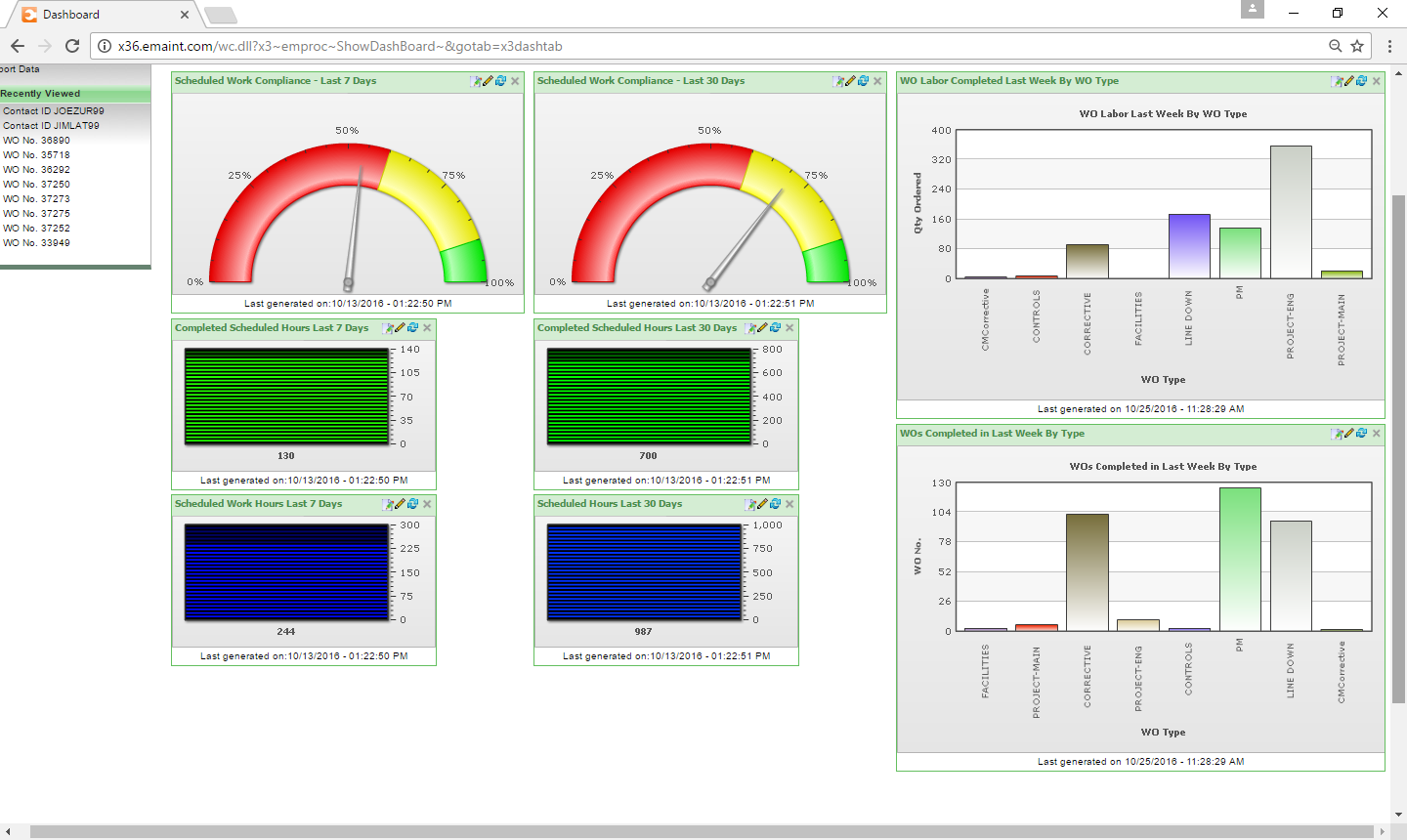
RESULTS
This boost in productivity can been seen in the 50% reduction in waste/scrap from manufacturing lines and the company’s ability to easily schedule 50-70% of technician work and over 900 preventive maintenance tasks for operators and maintenance. Drylock has successfully integrated operators into preventive maintenance efforts and schedules over 700 hours per month of preventive maintenance work orders across the factory just for production operators. This has resulted in a big gain in machine reliability and early detection of items wearing out.
Across the company’s 24/7 operation, Jason and his team track 2,637 assets including robotics palletizing, packaging conveyors, baggers and main manufacturing assembly lines within eMaint. They have seen a steady improvement in productivity, and are empowered to make incremental improvements to efficiency and effectiveness.
Jason extensively uses reports and dashboards to stay up-to-date on work performance across his maintenance crews and outside contractors. For example, his dashboard “Crew Labor By WO Type” shows what work is being focused on with each crew. This data enables Jason to analyze performance variances from crew to crew, and helps justify staffing or training needs.

With eMaint, the Drylock team is able to process nearly 1,200 work orders monthly and manage that work effectively. Jason is consistently impressed by the support and flexibility of the software, and plans to continually expand the company’s usage.
BENEFITS
“I couldn’t imagine being without eMaint. It is an integral part of our maintenance processes. My entire team relies on it everyday.”
Jason Anderson, Maintenance Manager, Drylock Technologies Ltd