By Michael Mills, Technical Solutions Manager at Fluke Reliability
Updated: July 16, 2025 • Originally Posted: 2021 • 10 min read
Quick Summary: What Is a Work Order?
- A work order is a documented request to perform maintenance, repair, or inspection on equipment or facilities.
- It typically includes task details, assigned personnel, resources needed, location, and scheduling.
- Work orders are essential for organizing maintenance, tracking progress, and keeping assets running reliably.
- Common types include preventive, corrective, inspection, and emergency work orders.
- A CMMS like eMaint helps automate, assign, and document work orders—making maintenance more efficient and accountable.
Work orders might seem simple but they’re the foundation of reliable, efficient maintenance. They assign responsibility, clarify tasks, and create a traceable record of work done on critical assets. Whether you’re managing a school, hospital, or factory floor, a clear and consistent work order process can have a measurable impact.
But not all work orders are created equal.
From maintenance supervisors to field techs, everyone benefits when work orders are structured, accessible, and digital. Switching to a modern system can reduce downtime, extend asset life, and help your entire team work smarter. Let’s walk through what that means—step by step. Here’s what we’ll cover:
In this guide, we’ll cover:
- Work Order Definition
- What Is a Work Order Used For?
- What Should Be Included in a Work Order?
- Work Order Example
- Why Are Work Orders Important?
- Benefits of Work Orders
- Common Types of Work Orders
- Work Order Process: From Submission to Close-Out
- Work Order Best Practices
- Digitalize Work Orders to Improve Efficiency
- Managing Digital Work Order Requests
- How CMMS Software Supports Better Work Orders
- Building a Work Order Process That Scales
- Real Results from Smarter Work Orders
- Frequently Asked Questions
Work Order Definition
Before we dive deeper, it helps to clearly define what a work order is.
A work order is a formal request to perform a specific maintenance task—like replacing a belt on a conveyor or fixing a broken light fixture.(Definition adapted from Merriam-Webster and industry standards such as those outlined by Society for Maintenance & Reliability Professionals (SMRP).)
Some organizations use the term “works order” or even “maintenance job card”—but the purpose is the same: to manage maintenance work in a structured, trackable way.

What is a Work Order Used For?
Work orders are used to formally track maintenance, repair, and service tasks across an organization. They provide detailed instructions, assign responsibility, and allocate resources so that each task is carried out systematically and efficiently.
By using work orders, maintenance teams can schedule labor and materials, share instructions with technicians, and document every step of the job. Over time, these records build a complete maintenance history for each asset—supporting better planning, budgeting, and decision-making.
What Information Should a Work Order Include?
A good work order description turns a vague task into clear action steps. For work order maintenance to succeed, the form must include all relevant details up front because a well-structured work order doesn’t just guide technicians, it becomes a valuable record for compliance, accountability, and long-term asset care. To be effective, it should include:
- A clear task description – What needs to be done and why
- Asset details – Equipment ID, location, and service history
- Priority level – Critical, high, medium, or low
- Estimated labor and parts – Time required and materials needed
- Assigned technician or team – Who’s responsible for execution
- Scheduled start and due dates – Timing and deadlines
- Completion notes and follow-ups – Documentation for traceability
When these fields are consistently filled out, the result is not just better task execution, but a complete, searchable history of your maintenance operations. “Standardized work orders give you more than just a checklist—they give you confidence that every technician is working from the same playbook, every time,” says Michael Mills, Technical Sales Team Leader at Fluke Reliability. “It’s how you turn maintenance tasks into reliable, repeatable results—no matter who’s on shift.”
Work Order Example
So, what does all that look like in practice?
Let’s say a technician spots a worn drive belt on a production line. Instead of fixing it ad hoc, they create a maintenance work order in the CMMS. To do that, they will need to answer the following questions:
- Which asset needs to be repaired? Where is the asset located?
- Which parts, if any, need to be replaced? Are they in stock?
- Which tools will the maintenance crew need?
- How many workers are needed to perform this job? What kinds of skills do they need? Will you need to call in outside support?
- What’s the timeline for performing this job? Is this a preventive maintenance project that must be done on a fixed date? Is this an urgent repair on a key asset that needs to be handled immediately?
- What costs are involved?
- Who requested and authorized the work?
When those questions are answered, your work order goes from basic form to clear field instructions—like this:
Work Order #: 002347
Type: Preventive Maintenance
Asset: HVAC Unit #12 (Main Office)
Location: Building A – Rooftop
Requested By: James McCallister
Priority: Medium
Assigned To: Dana Williams – HVAC Technician
Scheduled Date: August 20, 2025
Estimated Time: 2 hours
Description:
Perform quarterly maintenance on rooftop HVAC Unit #12. Clean coils, replace air filters, inspect belts and motor, check refrigerant levels, and log findings.
Tools/Materials Required:
- Coil cleaner
- Standard tool kit
- Replacement filters (Model: AF-22)
- Safety harness
Safety Notes:
Use fall protection on rooftop. Shut off power before starting any internal inspection.
Completion Notes:
Dana completed all tasks, replaced 2 filters, and noted minor wear on the fan belt. No urgent action needed but suggest monitoring belt tension next quarter.
Looking at this work order, here’s what jumps out:
- You know exactly where to go—Building A rooftop—and which unit to work on.
- The task list covers all key steps, so you won’t overlook something like refrigerant levels.
- You’re told what to bring (coils, filters, harness), so there’s no guessing or extra trips.
- The safety callouts remind you to shut off power and use fall protection—no surprises mid-job.
- The structured format also shows how a maintenance technician understands the order of work, which reduces delays and keeps safety top of mind.
It’s the kind of work order that lets you show up, get to work, and do the job right.
Why Are Work Orders Important?
Looking at the example above, it’s clear that when a work order is filled out with that level of clarity, it does more than get the job done—it sets the stage for better coordination, fewer delays, and smarter decisions down the line. From the field to the front office, that shared understanding is what makes maintenance operations truly click.
Here’s what that means in practice:
- Clear accountability. Everyone knows who’s responsible for what and when it’s due. No more missed tasks or finger-pointing.
- Smarter planning. Work orders help maintenance planners anticipate labor, parts, and downtime needs—especially for preventive tasks.
- Better documentation. With accurate digital records, audits are easier, warranty claims are smoother, and compliance is more straightforward.
- Less downtime. Clear instructions and better scheduling mean less back-and-forth, faster repairs, and more uptime for critical assets.
- Stronger decision-making. Looking back on past work helps you make better calls about when to repair, when to replace, and how to budget.
Digital work orders take it a step further. With a modern Computerized Maintenance Management Systems (CMMS), many of the details—like asset ID, location, service history, and assigned technician—can be auto-filled. This doesn’t just save time. It reduces errors, improves tracking, and helps maintenance teams stay proactive rather than reactive. We’ll dive deeper into the role of CMMS platforms in a later section.
But no matter how sophisticated the system, the core purpose of a work order stays the same: to assign, track, and complete a specific type of maintenance task. And not all tasks are created equal. That’s why work orders are typically grouped into categories, each designed to handle a different kind of need, from routine upkeep to urgent fixes.
Common Types of Work Orders
Understanding the different types of work orders—and what each work order is for—helps your team prioritize the right task at the right time.
Work orders generally fall into several categories: preventive, corrective, emergency, inspection, and more—each with its own purpose, urgency, and resource needs. These categories reflect widely accepted standards in the maintenance world, including those outlined by the Society for Maintenance & Reliability Professionals (SMRP). Here are six of the most common types of work orders used in maintenance programs today.
1. Preventive Maintenance Work Orders
What it is: Work orders for preventive maintenance are scheduled in advance to keep equipment running smoothly and reduce the risk of unplanned downtime. They can include routine cleaning, lubrication, and other preventive maintenance tasks to guarantee consistent asset performance. They’re usually based on time intervals (like every 90 days) or usage triggers (like every 1,000 hours of operation).
Best for: Routine inspections, oil changes, filter replacements
2. Corrective (Reactive) Maintenance Work Orders
What it is: Corrective maintenance work orders are issued to fix new problems before they become serious. Technicians might discover an issue while performing routine inspections or your AI tools might diagnose a new fault in your equipment. A corrective maintenance work order can include repairing or replacing worn or damaged parts on your equipment.
Best for: Replacing a failed motor, fixing a leaking pipe
3. Inspection Work Orders
What it is: Inspection work orders schedule a technician to come and inspect a particular asset. If a problem is detected during an inspection work order, a new work order is created to resolve the issue. What triggers an inspection order will depend on your maintenance strategy.
Best for: Visual inspections, safety checks, compliance audits
4. Emergency Work Orders
What it is Emergency work orders are created in response to an unexpected breakdown. These work orders require an immediate response to avoid costly downtime. When responding to emergency work orders, technicians should record why the asset failed, what was done to restore its normal operating condition, and provide recommendations for preventing this type of failure from occurring again.
Best for: Power outages, gas leaks, critical equipment failures
5. Electrical Work Orders
What it is Electrical work orders are focused on the repair or installation of electrical equipment. This can be installing new wiring, fixing lights, or dealing with any power supply issues.
Best for: Installing wiring, repairing electrical panels, fixing lighting and power issues
6. Special Project Work Orders
What it is Special project work orders are all about new and improved equipment. This is the type of work order that is required whenever a new asset needs to be installed. They can be used for any number of reasons such as improving the efficiency of operations or replacing aging equipment.
Best for: Installing new equipment, upgrading systems, infrastructure improvements
The best-run maintenance programs don’t rely on one type of work order—they use the full range strategically. But knowing the type is just the start. What happens next, from submission to close-out, is what determines success.
The Work Order Process: Step-by-Step Guide
There are six steps in the process of creating and approving a work order:
Step 1: Identify the ask
Whether submitted by a technician, machine operator, or building occupant, every work order should begin with a clearly defined request. However, it can also be triggered by predefined activities like preventive maintenance tasks or routine inspections. The process is much simpler when the maintenance is planned and resources can be allocated ahead of time.
Step 2: Create a new work request
Once the task is identified, a maintenance request is submitted to the maintenance team. For example, if a machine breaks down unexpectedly, a work request to repair it is submitted. If the task is part of a planned schedule, a CMMS like eMaint can automatically issue the request at the right time.
Step 3: Prioritize the work
Not every job is equally urgent. When requests are submitted, it’s up to the maintenance team to evaluate and prioritize. A solid process includes triage: categorizing the request, assigning priority, and getting quick approval based on safety or business impact. Some tasks are more time-sensitive than others, depending on their downstream effect. Once approved, the proper personnel and parts are assigned, and the request is converted into a work order.
Step 4: Create a Work Order
Once the work request has been approved and properly prioritized, a work order is officially created. It should have all the information required to complete the task, with resources already allocated and ready.
Step 5: Complete and document the work
The work order is then assigned to a technician to take action. They will perform the work, follow any standard procedures, and log key details such as labor hours, parts used, notes, and photos. This is vital for asset history and reliability tracking.
Step 6: Analyze the results
Supervisors review the work order to confirm completion, add any follow-up steps, and close it in the system. This step often includes generating reports or triggering follow-up PMs.
“Don’t stop there”, cautions Michael Mills, Technical Sales Team Leader at Fluke Reliability. “Your work order history offers valuable insights into your equipment and your existing processes to drive continuous improvement. Be sure to measure and adjust as needed.”
Bonus Tip: Automate Where You Can
Automated workflows and mobile access remove bottlenecks and keep work orders from getting lost in the shuffle. The fewer manual steps, the faster your team can respond.
When every step is handled with care—from request to close-out—you reduce delays, improve accountability, and keep operations running smoothly.
6 Work Order Best Practices from the Field
Once the steps are in place, the next challenge is doing them well. To make the most of your work order process, keep these proven tips in mind—many of which echo industry best practices shared by professionals in Plant Engineering and Reliable Plant.
1. Standardize your fields and templates: Use consistent formats for task descriptions, asset tags, and technician notes so everyone can read and act on them quickly.
2. Link work orders to asset history: Technicians perform better when they know what happened last time. A connected CMMS makes that context instantly available.
3. Include photos or attachments: Add pictures, manuals, or wiring diagrams so techs have everything they need on the job.
4. Automate preventive work orders: Use your CMMS to auto-generate work orders based on time, usage, or sensor data. This keeps PMs on track—no guesswork. For example, eMaint makes it possible to automatically schedule work orders based on equipment health data, so you can resolve problems early before they lead to failure.
5. Track time, cost, and completion: Don’t just close the work order—capture the time spent, materials used, and any follow-up actions needed.
6. Train teams on expectations: Make sure everyone knows how to fill out and close a work order properly. Clear standards reduce rework and boost performance.
Every work order follows the same core lifecycle—from request to closeout. Whether you’re managing this flow manually or using a work order system like eMaint CMMS, having a defined process helps you stay on top of maintenance, reduce downtime, and keep teams aligned. We’ll dive into this a little deeper in the next section.
Digitalize Work Orders to Improve Efficiency
Manually created work orders have long been part of the maintenance world. Though paper-based work orders can be easier in some ways, they do not perform well at scale. Paper-based work orders can result in communication delays, extra costs for data entry, and a headache from trying to store all of them safely. Most of all, they’re just plain slow. In today’s fast-paced maintenance world, paper-based work orders are inefficient — not to mention environmentally unfriendly.
A CMMS can help organizations embrace the power of cloud-based, online work order software and put an end to repeated phone calls, sticky notes, and missing paperwork. Centralizing and streamlining the work order process improves clarity and gets more work done on time.
Work Order Apps
Furthermore, a work order software app, also known as a mobile CMMS, is the smartphone or tablet version of a work order software can further help to streamline maintenance. Work order software apps allow technicians to enter data from mobile devices as they complete work orders. For planning and scheduling preventive maintenance tasks, technicians can use their devices to track in-progress work orders, as well as assets that still need to be serviced. The app provides them with information about the historical performance and inspection records right at their fingertips, making on-site maintenance easier than ever.
From fieldwork to request intake, the entire workflow benefits from going digital. Whether a technician is logging completed tasks or a facility team member is submitting a new request, a centralized system creates transparency across every stage.
But even with planned tasks running smoothly, unexpected work will always surface. That’s where digital request management steps in—capturing, prioritizing, and tracking reactive work in real time.
Managing Digital Work Order Requests
As not all work can be planned ahead of time, there has to be a request system for when corrective work is required or customer needs arise. Maintenance managers should tailor workflow processes for request submission, approval, rejection, and completion to the specific needs of their organization. Identifying a workflow process ahead of time ensures:
- Standard Operating Procedures (SOPs) are adhered to by all users
- Work goes through an approval process
- Areas of responsibility and expectations are clear for users
- Periodic process auditing is performed
- Valid data is being entered into a CMMS
- Efficient communication flow between all parties
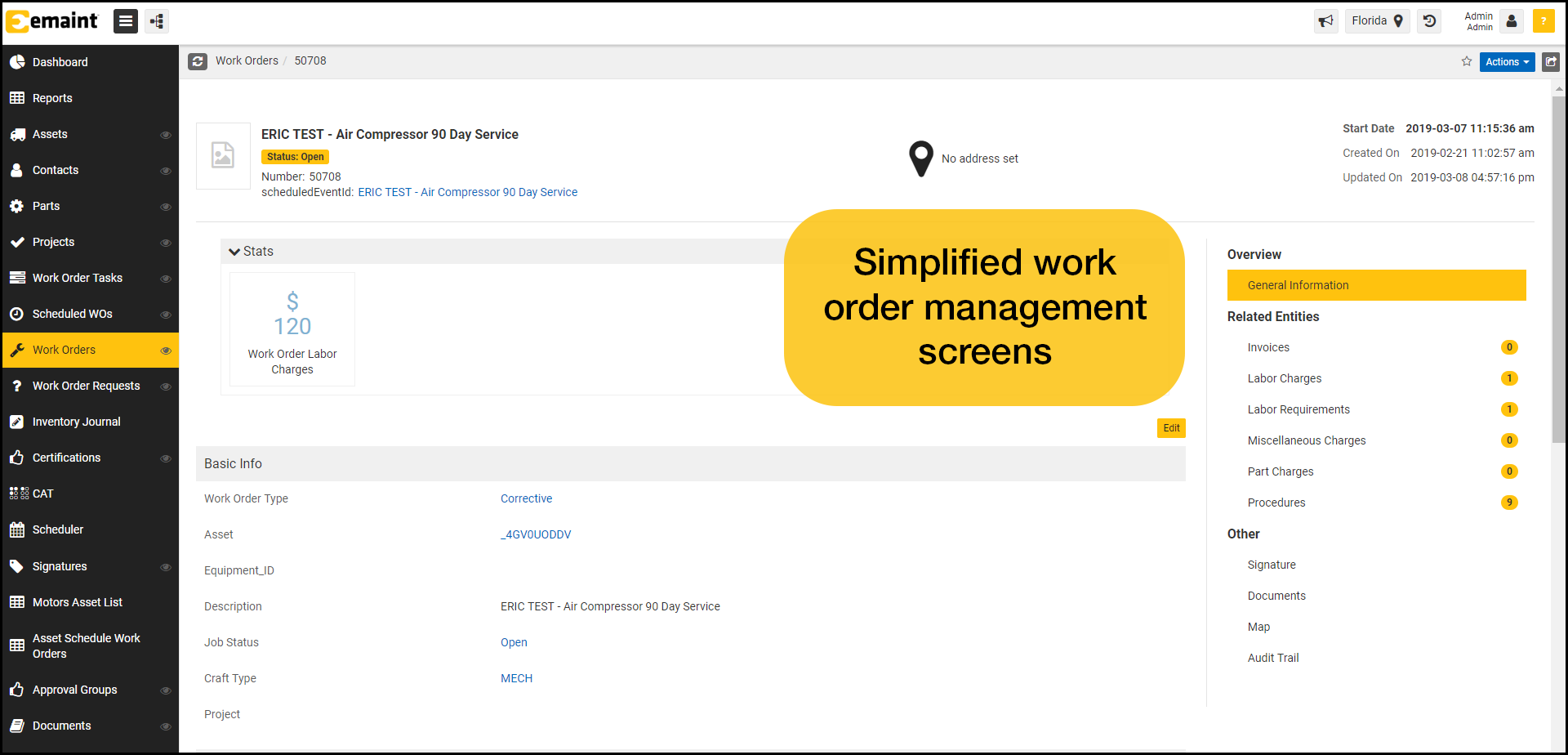
Screenshot of simplified eMaint work order management screen showing list of work orders with asset IDs, status, and scheduling columns
With eMaint, organizations can choose from three work order request submission options:
- Work requestors are given an eMaint user login that allows them to submit requests and view the history and status of those requests
- Work requestors send an email to a designated email address that gets converted into an eMaint work request
- Work requestors submit requests to eMaint through a customized web form embedded on a company’s website or intranet
Work request tools like these reduce communication errors. Organizations can send requestors automated email alerts when a work request is approved or rejected, followed by an automated email alert with a satisfaction survey once work has been completed.
With modern mobile CMMS solutions, requestors can submit work order requests whenever and wherever they are using their mobile device. Requestors can attach pictures to their requests, including the equipment needing repair.
How CMMS Software Supports Better Work Orders
A modern work order software system like eMaint simplifies every part of the work order process, from creating a maintenance work order to tracking performance over time. Here’s how:
✅ Centralized Access and Visibility
Everyone works from the same source of truth. Technicians can see open tasks, supervisors can track status, and stakeholders can view asset history—all in one platform.
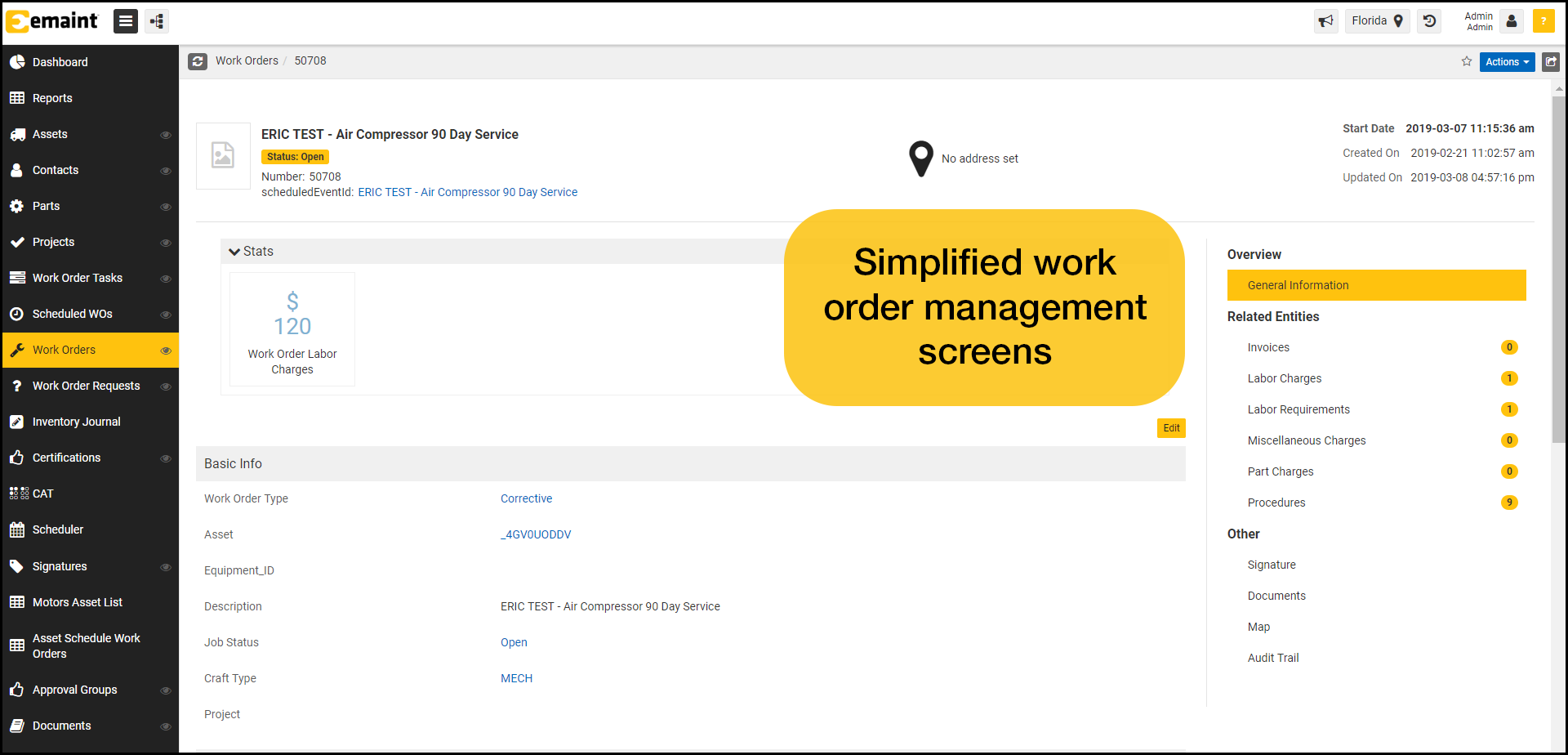
Screenshot of simplified eMaint work order management screen showing list of work orders with asset IDs, status, and scheduling columns
✅ Work Order Assignment – Using features such as eMaint’s maintenance scheduling tools, maintenance planners and schedulers can directly assign work orders to staff, contractors, or vendors for specific days, times, and locations. Assigned and unassigned work orders can also be viewed on a calendar display, and work can easily be reassigned when necessary.
✅ Scheduling Calendar – View a calendar by day, week, or month with all labor resources and open work orders. You can also adjust calendar views and filter work by employee, work order type, and more. Organizations can also use the PM Projection feature to plan upcoming work and ensure the right parts, labor, and tools are available.

eMaint CMMS scheduler interface showing dynamic drag-and-drop work order control by technician and date, with color-coded tasks and calendar view.
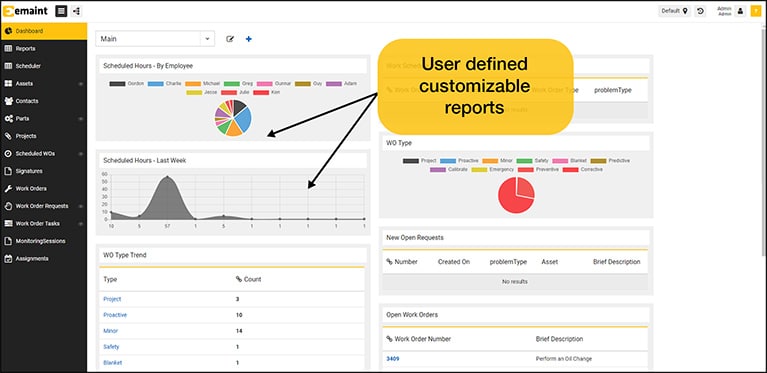
eMaint CMMS dashboard displaying work order metrics, real-time asset status, and visual performance indicators with customizable widgets.
✅ Mobile Maintenance – Using mobile CMMS maintenance services such as eMaint’s MX Mobile, organizations can access real-time data and perform functions throughout their facilities and on the road, including submitting and approving work requests, signing and closing out work orders, and more.
✅ Tracking Projects – Major overhaul and renovation projects can be a headache, but the management process doesn’t need to be. With eMaint’s project management tools, organizations can easily create projects and assign and track work orders from project inception to completion. Assets, inventories, and actions that impact operational goals can all be handled from one platform. With Gantt Charts, users can get a clear visual understanding of work order completion rates compared to a project’s end date.
Because a CMMS is connected to your asset register and parts inventory, you’re not just assigning work—you’re solving problems holistically.
Fact: Teams using eMaint often see a 20–50% reduction in downtime after switching to digital work orders.
That kind of impact doesn’t happen by chance—it happens when work order processes are built to grow with your team and technology. So, how do you set up a work order program that doesn’t just work today—but still works when your team, your workload, and your asset list grow?
Building a Work Order Process That Scales
Whether you’re starting from scratch or upgrading from sticky notes and spreadsheets, building a strong work order process is one of the smartest steps a maintenance team can take. But the key isn’t just setting up a system—it’s setting it up to scale.
Here’s how to get there:
Start with what you’ve got
Don’t wait for a perfect asset list or fully built inventory. Begin with your most critical equipment, document the most common tasks, and build momentum from there.
Choose the right work order system
Look for a CMMS that’s flexible enough to grow with you. eMaint, for example, lets you start small—managing work orders digitally—and expand into asset tracking, condition monitoring, and inventory management when you’re ready.
Train your team, not just your tech
Even the best system won’t help if it’s not used. Involve technicians early, provide hands-on training, and make sure the process works for them—not just management.
Track, review, improve
Use your work order history to spot trends, make better decisions, and continuously improve. The more you learn from past work, the less reactive your team becomes.
Connect the dots
As your program matures, link work orders to preventive maintenance schedules, inventory levels, and asset histories. That’s when the real efficiency gains kick in.
And when all those pieces come together—from smart starting points to team training and system integration—the payoff can be dramatic. The right approach to work orders doesn’t just improve maintenance operations in theory. It drives measurable results in the field.
Real Results from Smarter Work Orders
When digital work orders are done right—and supported by the right system—they do more than document tasks. They drive efficiency, accountability, and long-term gains.
Here’s how organizations across different industries used eMaint to turn better work order management into measurable impact:
Bemis Company
Before eMaint, Bemis wrestled with a backlog of over 120 overdue work orders and a staggering 20% unplanned downtime. Within six months of switching to automated PM and digital work orders in eMaint, they achieved:
- 85% reduction in equipment downtime (from 20% to 3%)
- Technician utilization rose from 50% ➝ 80%
- Work orders closed within 30 days jumped from 13% ➝ 73%
- Weekly report prep time cut from ~5 hours to just 30 minutes
Hoyt Archery
With a lean team and a demanding production schedule, Hoyt Archery needed reliability without complexity. Since adopting eMaint in 2009—with structured work orders tied to asset history and preventive maintenance schedules—they’ve seen:
- 40% reduction in equipment downtime
- 77% increase in preventive maintenance compliance
- Far better control over backlog and maintenance costs
“eMaint has given me a complete & permanent record of assets … which assists in annual budget forecasting.” — Rick G., Facilities/Maintenance Manager
XTO Energy
A 24/7 oplant struggled with misplaced orders and scattered handwritten logs. After moving to eMaint:
- Work order completion soared from 70% ➝ 100%—without hiring extra staff
- Backlog visibility improved dramatically
- Safety PMs became automated
Pratt & Whitney
In aerospace, the margin for error is zero. eMaint helped the team at Pratt & Whitney tie every task—PMs, repairs, inspections—to precise work orders that triggered notifications, documented activity, and kept schedules on track. The results:
- $100,000 saved on a single project
- Three months of downtime avoided
- Improved inventory accuracy and just-in-time spare parts availability
“Effective inventory management … decreases lead time for critical spare parts.”
— Bruce G., Maintenance Facilities Supervisor
Troy Design & Manufacturing
When you’re managing calibration, PMs, and safety tasks across four different locations, visibility is everything. TDM used the eMaint automated work order system to:
- Achieve a 96%+ work completion rate
- Eliminate paperwork with digital notifications and mobile access
- Track and improve service quality using built-in survey tools
“Everything is very visible … helped us better manage maintenance at our four locations.”
— Bill G., Facilities Manager
Work Order Benefits: What a Well-Run System Really Delivers
When you step back from the daily grind, work orders become more than just task trackers. They’re the engine of a smarter maintenance operation—helping teams prioritize, communicate, and build long-term reliability.
Every type of work order—emergency, corrective, PM—plays a role in moving from reactive to proactive. And when that work is structured, visible, and digital, it doesn’t just get done—it drives impact.
Here’s what a good work order process makes possible:
- A shared understanding of priorities across technicians, planners, and leadership
- Clear accountability for what’s done, when, and by whom
- Insight into trends, recurring issues, and improvement opportunities
- Less fire-fighting. More planning. Better outcomes.
And when all those pieces click into place, you get more than task completion. You get traction. That’s what sets the stage for smarter, more scalable maintenance—starting with the next work order.
Ready to take control of your maintenance workflow?
Explore eMaint CMMS or request a personalized demo to see how it fits your team.
Frequently Asked Questions
What is a work order?
A work order is a formal request for maintenance, repair, or inspection. It outlines the tasks to be performed, the assets involved, and the personnel responsible. Work orders are used to track maintenance activities and ensure accountability across teams. They are key to organizing a maintenance strategy.
What is a Maintenance Work Order?
A maintenance work order is a formal directive that authorizes specific maintenance tasks on equipment or facilities. It details the job description, necessary resources, and execution steps, providing a structured approach for maintenance teams. It is essential for tracking, scheduling, and ensuring the accountability of maintenance operations.
What does a good work order look like?
A good work order includes:
- Work Description: Detailed explanation of the task.
- Requestor Information: Who requested the work, and their contact information.
- Assigned Personnel: Names and roles of individuals responsible for execution.
- Timeline: Start and end dates, including any milestones.
- Resources: List of materials and equipment needed.
- Instructions and Standards: Specific procedures or standards to follow.
- Approval Signatures: Sign-offs are required to start and complete the work.
What should be included in a maintenance work order?
At a minimum: the task description, asset details, priority, resources required, and who’s responsible. Good work orders also include completion documentation for full traceability.
How to Fill out a Maintenance Work Order?
To fill out a maintenance work order effectively make sure it includes all of the following information:
- Description of Issue: Clearly describe the problem or maintenance task.
- Location: Specify where the work is to be performed.
- Priority: Assign a priority level to guide timely action.
- Assigned To: Detail who is responsible for completing the task.
- Estimated Time: Provide an estimate of how long the task should take.
- Required Tools and Materials: List all necessary tools and materials.
- Safety Notes: Include any safety precautions or relevant regulations.
What are the Functions of a Work Order?
The functions of a work order include:
- Authorization: Legitimizing the commencement of a task.
- Documentation: Providing a record of tasks, resources, and time.
- Coordination: Ensuring resources are scheduled and available.
- Tracking: Monitoring progress and status updates.
- Analysis: Offering data for operational insights and future planning.
What are the four types of work orders?
The most common types are:
- Preventive maintenance
- Reactive or corrective maintenance
- Inspection or safety checks
- Emergency work orders
Some organizations also use calibration, audit, or project-based work orders depending on their needs.
What’s the difference between a work request and a work order?
A work request is submitted by someone identifying a need (e.g., “The HVAC unit is making noise”). A work order is created after the request is reviewed and approved. It is the formal document issued in response to the work request, authorizing and detailing the specific tasks required. It includes assigned resources, timelines, and instructions, providing actionable steps to complete whatever work is needed.
How does a work order process work?
A typical process includes:
- Submission of a work request
- Approval and prioritization
- Work order creation
- Assignment to technician
- Task execution
- Documentation and closure
How can software help manage work orders?
A CMMS like eMaint work order software streamlines the entire process—automating scheduling, tracking assets, assigning technicians, managing spare parts, and storing historical records. It reduces manual effort and increases accountability.
What does work order mean in maintenance?
It’s a documented instruction to perform maintenance work on an asset or system, including all relevant information and tracking fields.
What is a works order?
“Works order” is a UK-based variation of the term. It refers to the same concept—a task issued for production, repair, or maintenance.
What are common mistakes to avoid when creating a work order?
Common pitfalls include vague task descriptions, missing asset details, unclear priority levels, and lack of completion documentation. These issues can lead to delays, miscommunication, and repeat work.
Can work orders be recurring or automated?
Yes. With a CMMS like eMaint, you can set up recurring work orders based on time, usage, or condition triggers—ensuring that automated maintenance tasks are performed on schedule without manual input.
What is the difference between a preventive work order and corrective work order?
A preventive work order is scheduled in advance to avoid equipment failure (e.g., changing a filter every 90 days), while a corrective work order responds to an identified issue (e.g., fixing a leaking pump after inspection).
Why is documentation important in a work order?
Documenting work orders ensures traceability, supports audits, helps with budgeting and planning, and builds an asset history that guides future maintenance decisions.
What is the difference between a work order and a purchase order or invoice?
A work order, purchase order, and invoice serve very different purposes within an organization. A work order is for maintenance, detailing the tasks to be performed. In contrast, a purchase order is a document sent to suppliers to procure goods or services, specifying the items, quantities, and agreed prices. An invoice is a bill issued by a supplier to request payment for goods or services provided. A work order initiates maintenance tasks, a purchase order initiates purchasing activities, and an invoice facilitates financial transactions and payment processing.
What is the difference between work orders and maintenance orders?
While we have mostly been referring to work orders as they apply to maintenance operations, they are more versatile than that. A work order can apply to various operational tasks, including maintenance, construction, or IT services, a maintenance order refers explicitly to work orders created for the upkeep, repair, or inspection of equipment and facilities. All maintenance orders are work orders, but not all work orders are maintenance orders.
What is the work order?
It’s the formal document created after a work request is approved, outlining the required tasks, timeline, personnel, and asset details involved in performing maintenance.
What is workorder?
“Workorder” is a common misspelling of “work order.” While the meaning is the same, the correct term is two words: work order.