What is Preventive Maintenance?
Also called planned or preventative maintenance, PM is conducted throughout an asset’s normal operating conditions. This helps avoid unexpected breakdowns and their pricey consequences, such as unplanned downtime.
Preventive maintenance is not based on a machine’s condition. Instead, it is based on recommendations from the asset manufacturer or on the average life cycle of an asset. Basing maintenance on a calendar means that some maintenance tasks are done when they aren’t strictly needed. It also means that teams can ensure that they have the budget, inventory, and scheduling to perform the tasks.
Preventive maintenance software, including a computerized maintenance management system (CMMS), can simplify preventive maintenance even more through features such as auto-scheduled work orders. Streamlining maintenance practices reduces emergency, reactive work and increases worker safety and efficiency.
Performed consistently, preventive maintenance services, also called preventative maintenance services, can help your organization avoid expensive downtime and disruptions.
Types of Preventive Maintenance and Preventive Maintenance Examples
- Calendar- or Time-based preventive maintenance
These types of preventive maintenance are completed at regular or scheduled intervals with help from preventive maintenance software. While all critical equipment should have PM, regularly checking equipment critical to production will help decrease breakdowns.
A motor-pool may have required fleet maintenance every 4 months. This is a great example of preventive maintenance. - Usage-based preventive maintenance
Another type of preventive maintenance example is called usage-based, where a machine’s statistics are used to determine corrective actions. Usage statistics can include cycle counts, runtime, miles/kilometers traveled, or hours, among others.
For example, one kind of PM could be where an industrial maintenance technician checks machine usage statistics. Then, depending on measurements and usage readings gathered in rounds, maintenance may be scheduled.
Preventive Maintenance Software
Preventive maintenance software, such as eMaint’s CMMS, is a key tool to moving away from reactive maintenance and daily disruptions. With the right program, maintenance teams can reduce costs and increase uptime. Preventive maintenance software is important because it allows maintenance teams to set calendar- and/or meter-based PM tasks for every asset. Within the preventive maintenance task record, users add a detailed description that can include important information like task procedures and guidelines.
Preventive maintenance software also reduces data entry by eliminating the need to create new tasks for every PM schedule. The preventive maintenance software simply associates a PM task with multiple PM schedules.
It also lets users maintain consistency in their processes. Preventive maintenance software enables teams to create a sequence of procedures for every preventive maintenance task. That way, technicians have a step-by-step guide to completing their work.
How Does Preventive Maintenance Work?
Organizations avoid cost overruns by scheduling preventive maintenance. And all parts and maintenance resources can be planned and accounted for to streamline the process.
Preventive maintenance is a relatively straightforward strategy to establish and set in motion. Managers schedule PMs based on calendar dates or usage, often at the manufacturer’s recommendation. Teams shut down equipment during a specified date and time. Then, they perform the outlined tasks on that piece of equipment.
Managers can set up PMs with breakdown and time-based triggers. CMMS software triggers alarms to alert employees of required maintenance. Software triggers a breakdown PM when equipment cannot be used until maintenance is performed. Scheduled maintenance is triggered whenever the calendar rolls over to a pre-specified date with a time trigger.
For example, forklift manufacturers may suggest performing maintenance every 150 to 200 hours of use, establishing a time-based trigger. Performing this maintenance can mean extending the life of assets, increasing productivity, improving overall efficiency, and reducing maintenance costs.
Preventive maintenance does not require additional tools other than the manufacturer’s recommendations and a team willing to adopt new maintenance processes. To achieve buy-in from the group, it is important to outline the benefits of a PM program and identify how a preventive maintenance schedule will make the jobs of technicians, mechanics, and engineers much more manageable.
Teams leveraging a computerized maintenance management system (CMMS) trigger periodic preventive maintenance inspections based on calendar intervals or usage (for air compressors and forklifts) or mileage for company vehicles. This company has increased its planned maintenance percentage from 20% to 80%, and their on-time completion rate for PMs is 85% and continues to improve.
Preventive Maintenance Benefits
The benefits of preventive maintenance solutions are numerous.. An effective PM program helps organizations reduce costs while improving their processes and operations. Some of the specific, quantifiable preventive maintenance benefits include:
Pros of preventive maintenance
- Increased safety
- Longer equipment lifecycles
- Decreased unplanned downtime
Cons of preventive maintenance
- Requires time investment for planning
- Frequency of planned maintenance may need fine-tuning
- Learning curve for workflow changes
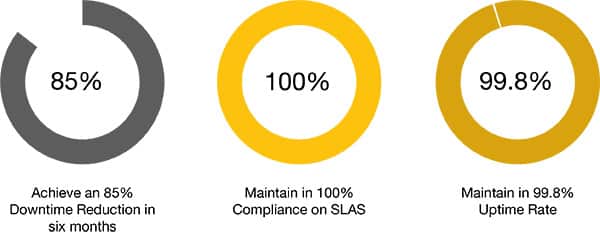
Extended asset life and increased equipment uptime
- Enhanced productivity and efficiency
- Diminished paperwork and manual data entry
- Stronger work execution
- Reduced unexpected breakdowns
- Improved audit compliance
Preventive maintenance is the simplest and most straightforward maintenance strategy to implement. It requires following manufacturer recommendations and establishing a standard maintenance schedule for critical assets and equipment. A PM program helps maintenance teams boost their planning and efficiency while reducing unplanned breakdowns and lost production. Switching to preventive maintenance can be done one step at a time, starting with the most critical assets.
Your Guide to Preventive Maintenance
What is preventive maintenance or preventative maintenance?
Preventive maintenance is a kind of proactive maintenance strategy. The purpose of preventive maintenance is to ensure optimal equipment health is achieved for longer durations.
Why is preventive maintenance important?
Preventive maintenance is important because it allows teams to plan actions prior to equipment breakdowns. An efficient PM schedule manages downtime so that it won’t impact production. Planning preventive maintenance also includes planning resources, such as needed supplies or parts.
Will preventive maintenance eliminate all breakdowns?
While PM will not eliminate all breakdowns, it will substantially reduce unplanned downtime and breakdowns. By planning preventive maintenance before a breakdown can occur, teams can avoid many kinds of breakdowns.
What is the difference between preventive and reactive maintenance?
Reactive maintenance is not proactive. Reactive maintenance only happens after a breakdown occurs. Instead, preventive maintenance is a strategy of completing maintenance at such an interval to avoid breakdowns altogether.
Many organizations have moved away from run-to-failure or reactive maintenance modes. However, a majority of organizations still use this method today. Reactive maintenance involves repairing equipment after it has broken down to restore normal operation.
On the surface, it may seem less expensive to operate reactively — and it is in some situations. Still, in general, planned maintenance can be much less costly. Studies observe that reactive maintenance typically costs five to eight times more than preventive or predictive maintenance.
Maintenance managers know there’s a variety of other costs associated with unplanned outages. Lost production, overtime, idle equipment, expedited shipments, and other “hidden” expenses, which can include:
- Safety issues
- Uncontrollable and unpredictable budget costs
- Shorter life expectancy for equipment
- Greater chance of inspection failure
- Increased downtime for equipment and employees
- Repeat issues and breakdowns
Organizations avoid cost overruns by scheduling preventive maintenance. And all parts and maintenance resources can be planned and accounted for to streamline the process.
What is the difference between preventive maintenance and predictive maintenance?
Preventive maintenance is a good way to move from reactive to predictive maintenance. Predictive strategies (PdM) use condition monitoring tools and data analysis to determine the right time for maintenance. A proper preventive maintenance strategy can lead to predictive maintenance programs.
While preventive maintenance determines schedules based on manufacturer recommendations or the average life cycle, predictive maintenance is very different. Teams track equipment conditions to identify when to schedule and perform maintenance.
Additionally, technicians perform preventive maintenance tasks during planned machine shutdowns, allowing PMs to occur during normal operations. Predictive maintenance also utilizes various advanced techniques such as infrared thermal imaging, vibration analysis, and oil analysis to predict failures.
The most effective maintenance programs leverage reactive, preventive, and predictive methods. This requires analyzing tasks to identify which method is best based on disruption due to equipment downtime, cost of parts, labor time, and equipment history.
REACTIVE MAINTENANCE
PREVENTIVE MAINTENANCE
PREDICTIVE MAINTENANCE
Examples of Preventive Maintenance Programs
Often, preventive maintenance is just one strategy practiced by a maintenance team. Some of the best maintenance programs take a proactive approach, where 60% or more of all maintenance activity is preventive. This decreases fire drills and disruptions to a less-than daily occurrence. A world-class maintenance program reflects an organization’s goals, and works toward them through planning, implementation, and evaluation. This strategy helps organizations improve quality and output, increase equipment uptime and Overall Equipment Effectiveness (OEE), reduce costs, and more.
Equipment Inspections
Routine machine inspections are one of the most common preventive maintenance examples. Maintenance teams frequently conduct calendar-based inspections of critical machines. These regular inspections help ensure a facility stays up and running.
Equipment Cleaning
Mechanical systems don’t do well when dirt and dust is allowed to accumulate. As contaminants build up, it creates friction and causes wear, eventually damaging machine components. Maintenance teams regularly clean these contaminants off to help avoid premature wear.
Lubricate Parts
Lubricants are vital for keeping machine parts moving. Without lubrication, bearing failure can damage equipment and lead to downtime. Ensuring regular lubrication is one of the best preventive maintenance examples for keeping machines healthy.
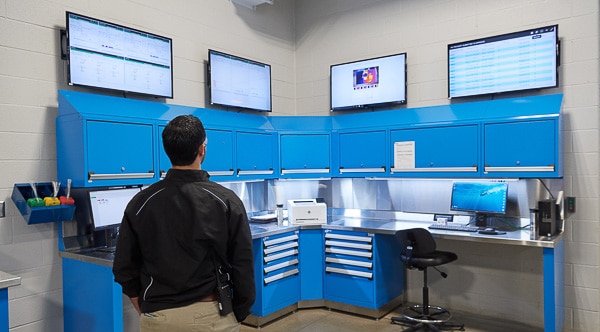
Preventive Maintenance Advantages and Disadvantages
Preventive maintenance (PM) is a reliable approach for managing equipment on a consistent schedule to lower the frequency of failures. There are many advantages of preventive maintenance, including helping lengthen asset lifespan, reducing unplanned downtime, and increasing operational efficiencies across the board.
While there are many advantages of preventive maintenance, it’s not 100% foolproof and won’t eliminate all risk of unexpected breakdowns. It’s also a labor-intensive method, and it requires time and resources to execute effectively.
The potential for over-maintenance is there, too: When you have to change the filter on an HVAC unit, you already know when to clean it without using PM. Letting it run to failure would cost relatively the same for a replacement. Arguably, you could save your resources for the breakdowns that are a greater threat to operations. The best policy is to weigh your options and get familiarized with various failure modes before you execute a usage-based PM plan.
What Does Preventive Maintenance Achieve in Practice?
Preventive maintenance solutions promote the health and safety of workers while improving productivity and saving costs. Some types of preventive maintenance are performed at regular intervals to measure criticality whereas other types are usage-based instead, taking corrective actions only when machines fall below accepted parameters. Unlike reactive maintenance, PM predicts equipment failure long before it holds up the rest of the production pipeline. In junction with a CMMS, this system can automate scheduled inspections, cleaning, and part lubrication.
What are the Advantages of Preventive Maintenance?
When manufacturers implement a preventive maintenance program, they typically see continuous improvements in machine longevity, which are visible in their KPIs. Over time, this lessens the effects of asset depreciation, as the team makes better procurement decisions in response to adjustments or replacements. In short, it makes the jobs of engineers, operators, and technicians much easier.
Five Advantages of Preventive Maintenance
1. Increase Asset Lifespan
A longer asset lifespan is a major advantage of preventive maintenance because it detects minor defects that throw a wrench into machine capacity. Maintaining good asset health assures that you have a shorter mean time between failures (MTBF). This KPI lends a hand in you making informed decisions for the next steps, instead of panicking about emergency work orders. It saves you the trouble of replacing expensive pieces and sets the precedent for ongoing regulatory compliance.
2. Save Money
Maintenance costs can put financial stress on the infrastructure, especially if there are complex mechanical systems in multiple buildings. To bring down asset spending, preventive maintenance lets technicians organize a larger number of tasks and complete them with more accuracy. For cleaning, it could show signs of leaks or rust accumulation on metal surfaces. And for the spare parts inventory, you won’t need to purchase stock as often to handle a complete replacement.
3. Reduce Disruptions
Another advantage is lessening interruptions on integral workflows. Rather than halting production when fulfilling requests, you should schedule maintenance around expected downtimes to optimize equipment availability. To conserve resources, have each technician focus on one project while giving them access to the required assets. Plan accordingly by identifying the failure mode and assigning employees with matching skills to quickly finish the work order.
4. Regulate Asset Runtimes
Organizing a floor plan means needing to estimate how long assets will run and making sure machines don’t fall out of their specifications. This is crucial for modifying the rate of production in case of rust build-up, uneven heat transfer, friction between surfaces, and other factors. Regular maintenance puts a stop to this by saving energy at the factory and generating less scrap or waste. The outcome is fewer faulty and damaged products reaching the consumer.
5. Reduce Equipment Downtime
Lastly, preventive maintenance minimizes overall downtime because your technicians don’t have to shut everything down just to conduct a maintenance session. Compared to reactive measures, you aren’t facing downtime from having to ship items or waiting for a specialist to arrive on-site. Instead, it gives you an opening to schedule activities after operations have ceased for the day. PM singles out areas that need attention so you don’t have to bring backup assets to pick up the slack. For more information, learn how to optimize and improve a preventive maintenance program.
What is a PM Schedule?
A preventive maintenance schedule is a plan to do maintenance after a specific duration, such as time or usage.
As a preventive maintenance example, consider a vehicle’s user manual that has a schedule for maintenance, such as oil changes every 3 months or 3,000 miles. The manual has both a time-based PM (3 months) and a usage-based (3,000 miles) PM schedule. For maintenance teams, this would be done at an equipment level for production-critical assets.
The focus of maintenance shifts from reacting to problems to continuous improvement through performance analysis and other methods. Preventive maintenance — and preventive maintenance software — enables this through providing planning, scheduling, coordination, and reliability.
Some preventive maintenance examples with real-world client successes include:
- Reducing downtime 85% in six months
- Maintaining a 99.8% uptime rate
- Achieving a 100% compliance on SLAs
Designing and launching a preventive maintenance program requires time and effort. You’ll have to develop procedures, schedule training, and communicate with your team. According to Life Cycle Engineering, every hour of effective planning saves three hours in labor time, or an equivalent savings in materials and production downtime.
Tips to Start a Preventive Maintenance Schedule
- Establish equipment list and determine best PM candidates: To get started, take note of all of the equipment throughout your organization to establish inventory. Within this list, you will ask yourself the above questions to help decide which pieces of equipment you will include in your future preventive maintenance plan.
- Refer to manufacturer recommendations: Take a look through manufacturer recommendations to establish an effective preventive maintenance schedule and to help figure out the necessary tasks and desired frequency of maintenance. Referring back to the original example, this could be getting an oil change for your car every 10,000 miles, or as recommended by your owner’s manual.
- Start with your heavy hitters: To effectively leverage a preventive maintenance schedule, it is important to begin with your most critical pieces of equipment one step at a time. Once you get started with those critical assets, create long term plans such as annual schedules.
- Fill in short term plans: With long term plans established, you can begin creating weekly plans for your crew. Teams should assign and schedule tasks, with all parts and maintenance resources accounted for.
With preventive maintenance scheduling software like CMMS, organizations have experienced benefits such as:
- Extended asset life and increased equipment uptime
- Decreased manual data entry
- Less paperwork with mobile and barcoding capability
- Consistent maintenance tasks and procedures
- Increased productivity and efficiency
- Improved audit compliance with extensive documentation
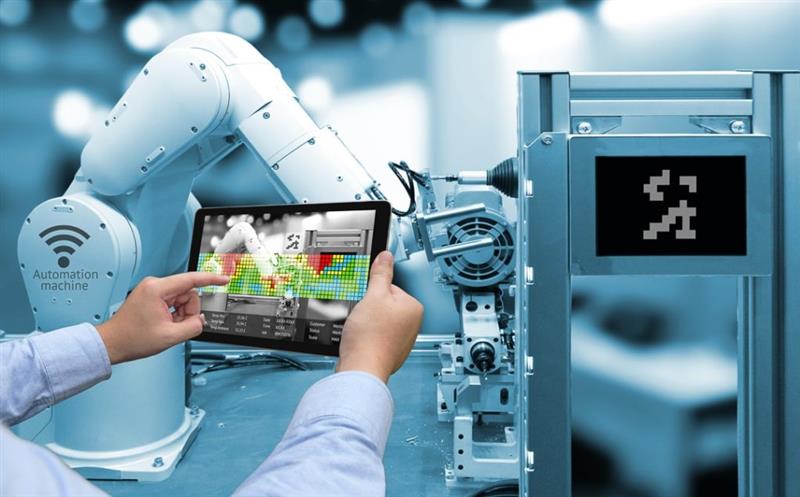
How to Create a Preventive Maintenance Plan
eMaint has developed six steps to create an effective, world-class preventive maintenance program.
- Identify the end goal
- Complete an asset criticality assessment
- Establish job and labor resources
- Start with the BIG picture: long-term scheduling
- Drill down: short-term scheduling
- Offer training to employees and clearly communicate goals
Start with the end in mind: What does your company want to accomplish? Define your procedures clearly to align with organizational goals.
For example, many manufacturing organizations focus on improving work efficiency. This goal helps guide your processes to reap benefits. With the right preventive maintenance plan, you could reduce equipment downtime, improve work completion rates, and maximize production time available per machine.
How to Implement a Preventive Maintenance Program
One of the best ways to implement a successful preventive maintenance service, also called preventative maintenance service, is to start small with a pilot program. Choose a few select pieces of equipment that are critical to operations and plan out your upcoming preventive maintenance schedule.
With data from the preventive maintenance software used in your pilot program, you’ll be able to sell the concept to leadership with data. You’ll have your own real-world examples of preventive maintenance success. And, hopefully, the proof will push them to expand the PM program within your organization.
Achieve Your Short-term and Long-term Maintenance Goals
Over time, a preventive maintenance program helps organizations achieve both short-term and long-term maintenance goals and achieve quantifiable results. These include:
- Reducing manual data entry
- Minimizing paperwork with mobile maintenance capability
- Increasing productivity and efficiency
- Improving audit compliance with extensive documentation
Learn more about the benefits of predictive maintenance.